New functions within Claas telematics provide an overview of machine status and settings and, says the company, a convenient solution for reliable data and documentation transfer.
On the Jaguar, telematics allows information on forage quality and volume from an NIR sensor to now be analysed and recorded for each field. Claas says it is now easy to create and transfer clear and highly precise yield maps and the amount of silage additive applied can also be accurately recorded and documented. Data and maps can be exported and transferred in ISOXML format if required.
Using the new Claas API open standard document exchange interface, the telematics platform can also be connected directly to numerous farm management systems. As a result, field boundaries can be automatically transferred to the telematics platform, and the data from the automatic documentation is directly transferred to the respective farm management system. This eliminates the manual export and import of data.
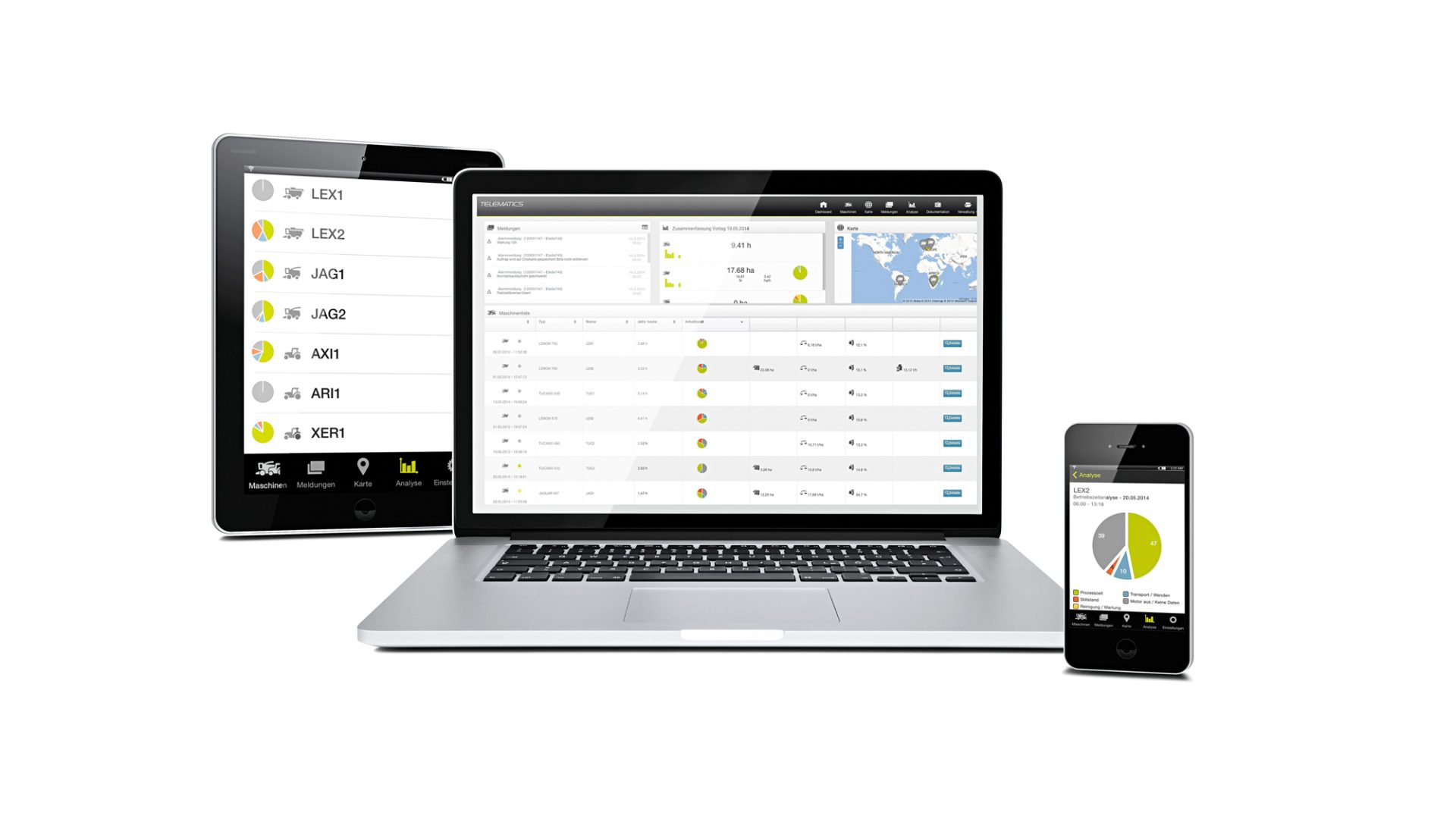
Once the field boundaries have been stored, the system automatically recognises the field in which the machine is located. Based on the field boundaries and recorded tracks for each activity, the telematics platform then creates field-related documentation for various parameters.
The system is fully automated which means that there is no additional work for the driver or in the office and it is possible to automatically export and import application and management information.
Claas says the TONI function in the telematic platform continues to be unique. The ISObus interface can also be used to document data from stored add-on devices such as balers or loader wagons or, if necessary, to export it in ISOXML format.
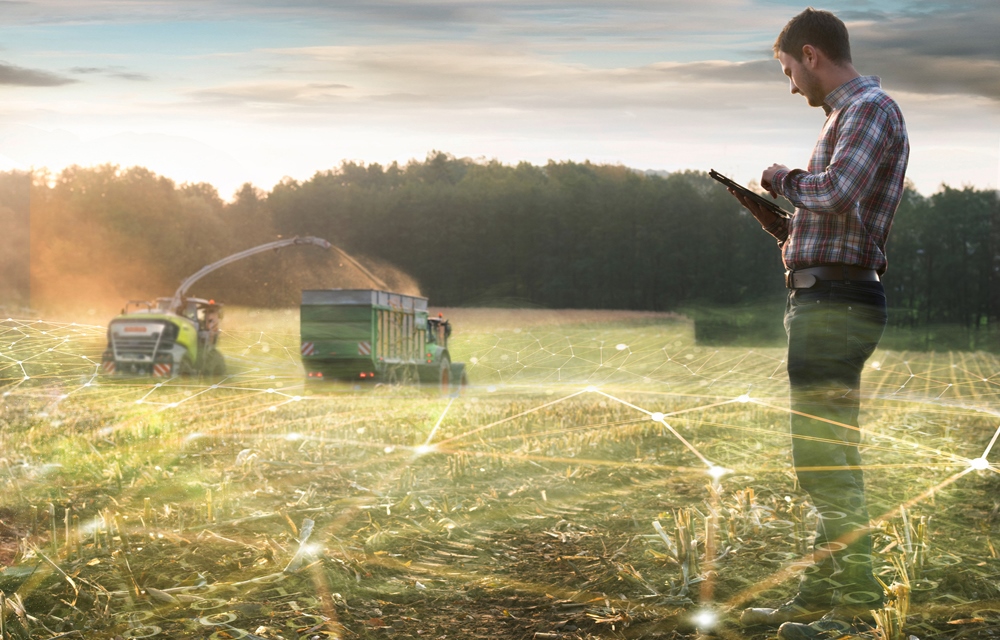
Using DataConnect, it will also be possible in the future to display the mixed vehicle fleets with networked machines from John Deere, Case IH, Steyr and New Holland in telematics.
Telematics is fitted as standard on many Claas tractors and harvesters and, in addition to documentation, also offers digital dealer support through remote service. This includes the transmission of faults to the responsible sales and service partner. A proactive maintenance plan is a further component of the remote service.