The idea of adding a bale collector behind our round baler came to us approximately two years ago when we bought a second-hand inline bale wrapper. The capability to run the wrapper behind the baler prompted us to build a hitch for our Krone Vario Pack. We routed two hydraulic pipes, a multi-core cable for the controls and then another cable for the various lights.
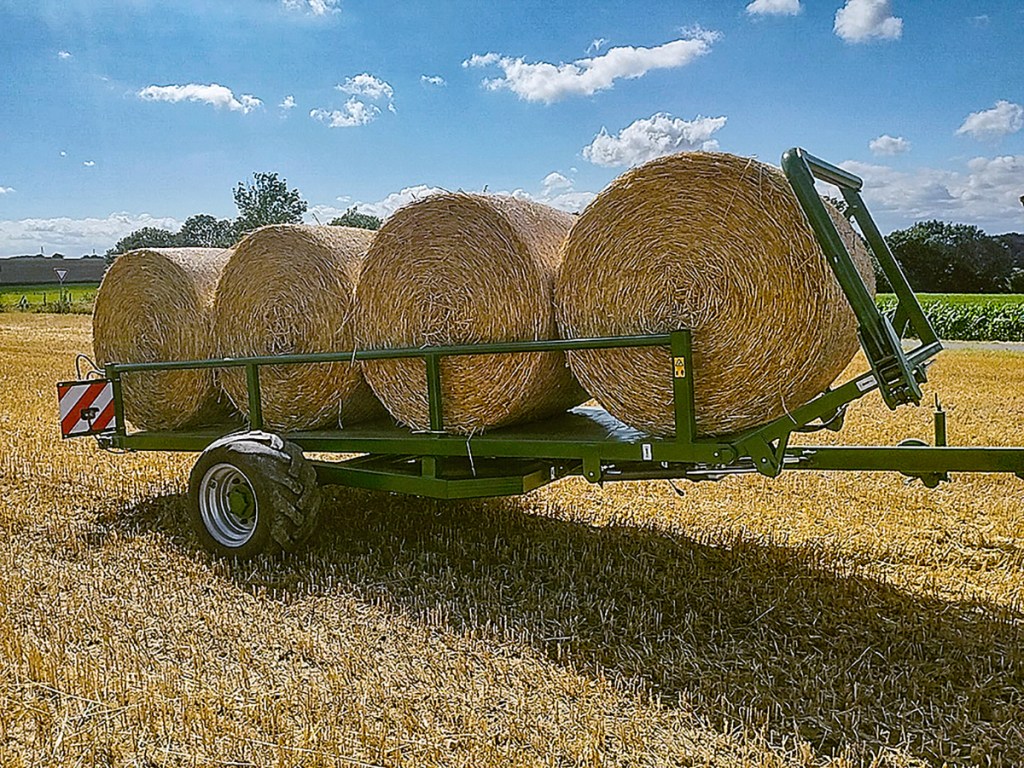
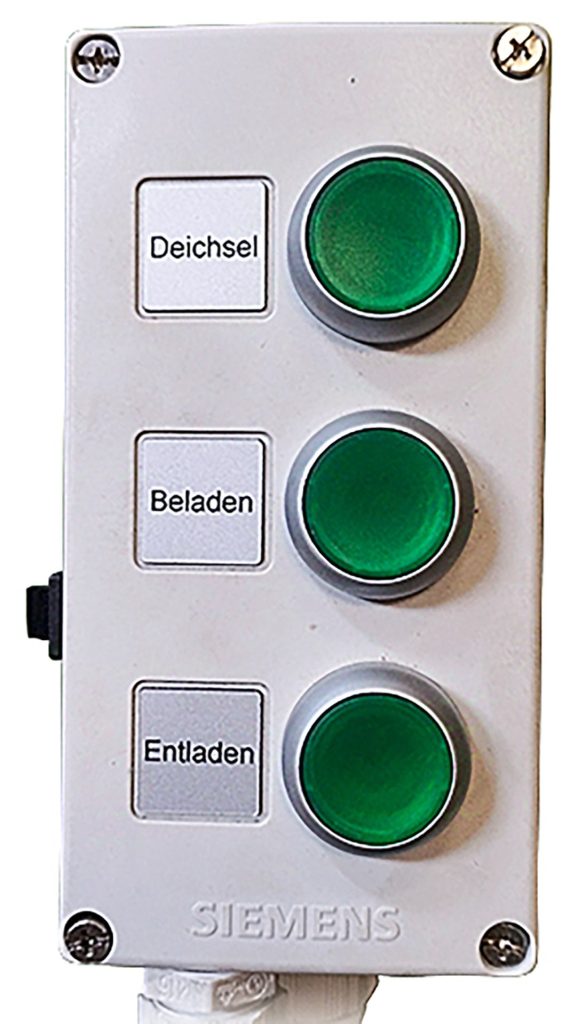
Making use of the axle off a scrapped beet harvester, we designed a simple collector model with a CAD software program. The individual steel tubes were made and cut with a band saw, a mag drill, lathe and a milling machine and then welded to form the various assemblies.
The new hydraulic system consists of two 6/2-way valves and seven hydraulic cylinders. The first service pivots the drawbar so the collector can run behind the baler or offset if using it directly with a tractor. When on the tractor the lifter folds down; sequence control ensures that the lifting arm folds out, too. When lifting the bale, the arm moves in first and then the lifter is raised.
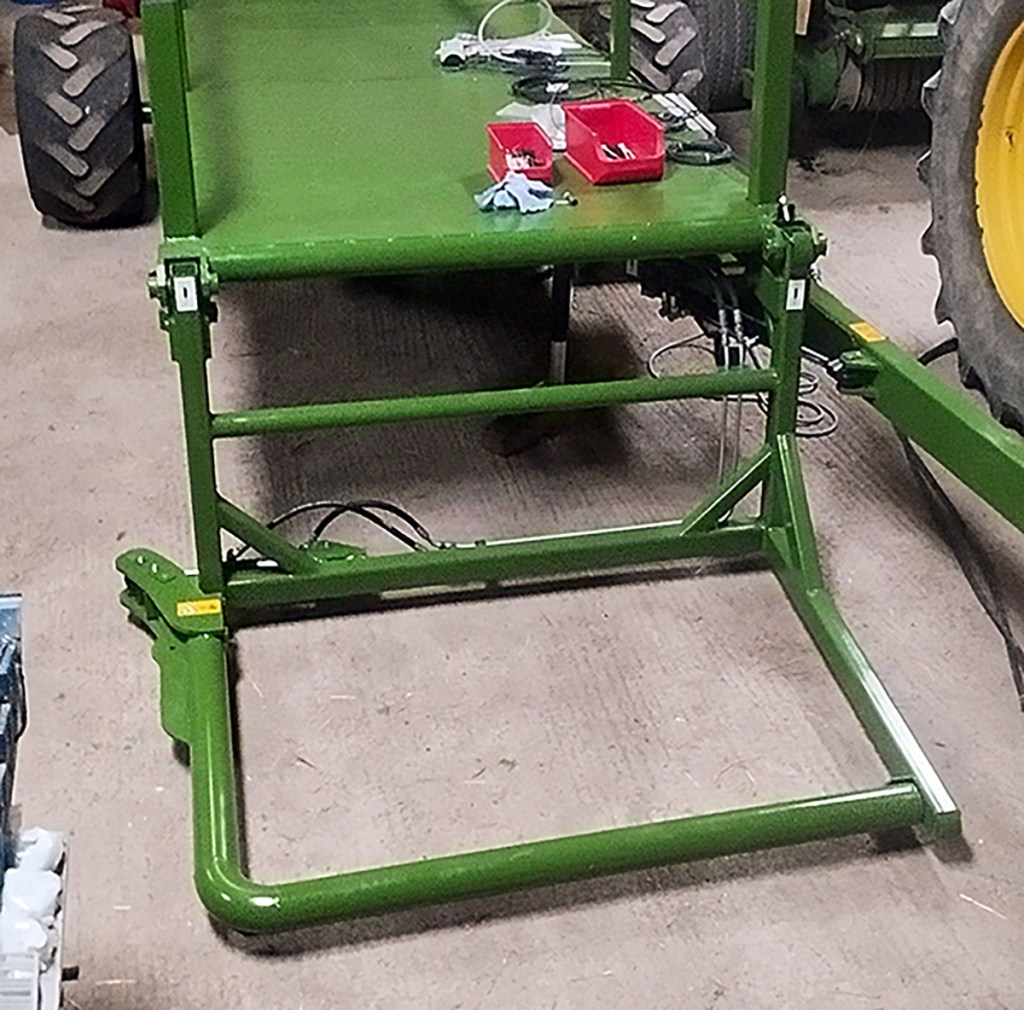
When operated in the field behind the baler, the pivoting arm is locked by a ball valve, because the bales roll directly into the closed lifter. Position of the lifter is monitored by a position sensor so that the drawbar can only be adjusted when the lifter is raised. On the sloped bed, the bale automatically rolls all the way to the rear. Optical sensors and a relay timer issue an audible warning when the collector is full. For unloading (third service), the tailgate opens first, and then the table tips.
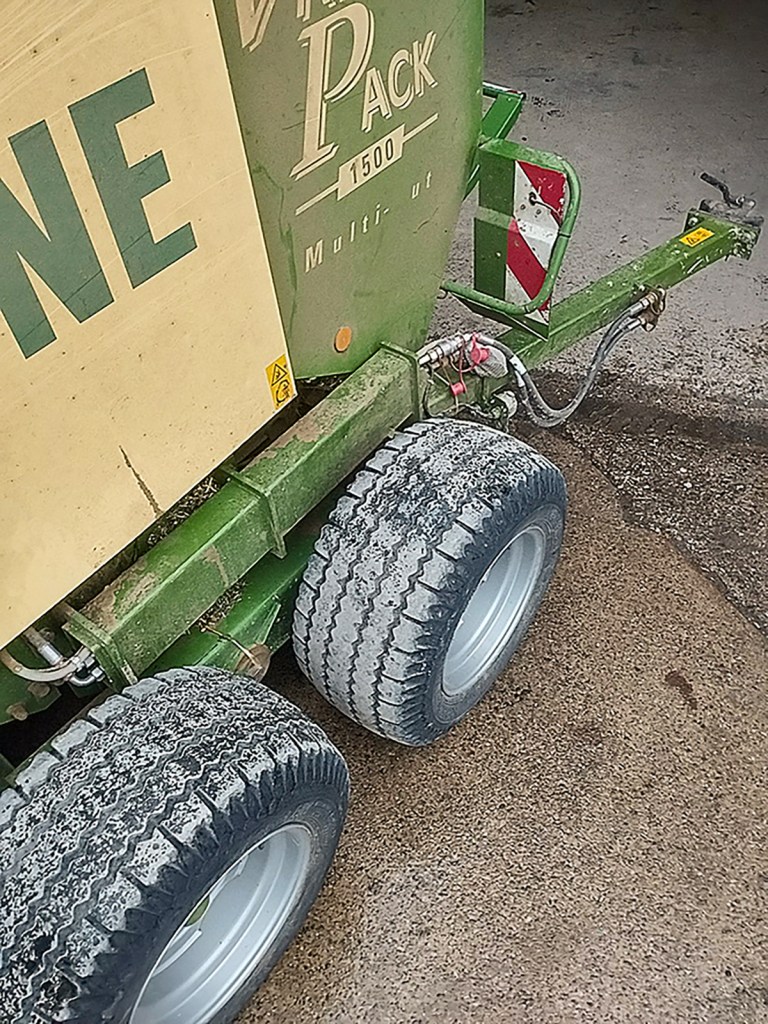
Markus and Christian Lues
For more up-to-date farming news click here and subscribe now to profi and save.