G Rae Contracting set about expanding their winter work in 2023, by building a mobile slurry separator. The operation has since taken on a life of its own.
KEEPING IT BRIEF
- Since 2023, the slurry separator has worked around 1,500 hours.
- The separator system is powered by an on-board generator.
- Outputs of 90-110m3/hr in thick beef stock slurry.
Twenty years ago, in the pre-emission’s days, slurry was just one of those jobs you had to get done, the product was seen as something of an inconvenience. Changes to legislation combined with higher fertiliser prices has brought a new attitude to slurry and its value, as well as storage concerns for older farm set ups.
Lockerbie-based G Rae Contracting run a full service agricultural contracting business with combines, forage harvesters, muck and slurry handling, as well as all of the jobs in-between. The west of Scotland is a fertile area, but it’s exposed to weather and has a cool climate. Andy Rae wanted to add something to the business that would complement what they already offered, and fill some of their quieter times.
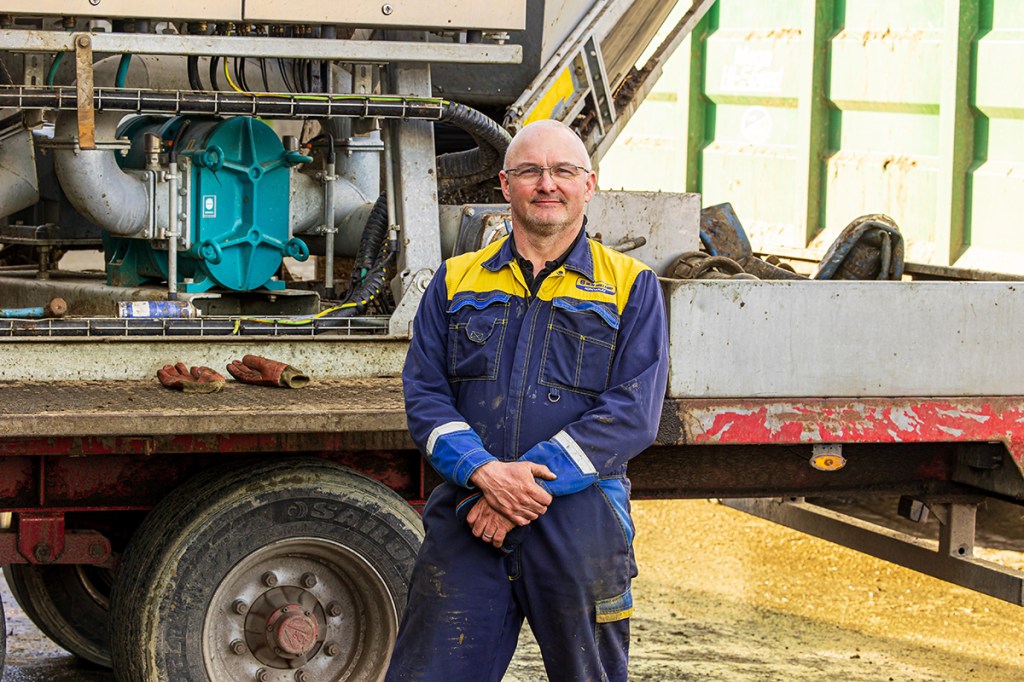
“I’d been watching what the farmers and contractors in continental Europe were doing, for about ten years, there definitely seemed to be an appetite for mobile slurry separation,” he says, having seen a few systems, but nothing quite ticked all of the boxes. “I started looking at what was available, a sensible amount of output was the main deciding factor.”
Already kitted out with three umbilical systems, four slurry tanks with dribble bar applicators and two 18,000-litre ferry tanks alongside Bunning rear discharge spreaders. Separating seemed like a service that would fit in seasonally and work with the kit they had, but such a service had been unproven in the UK at that point.

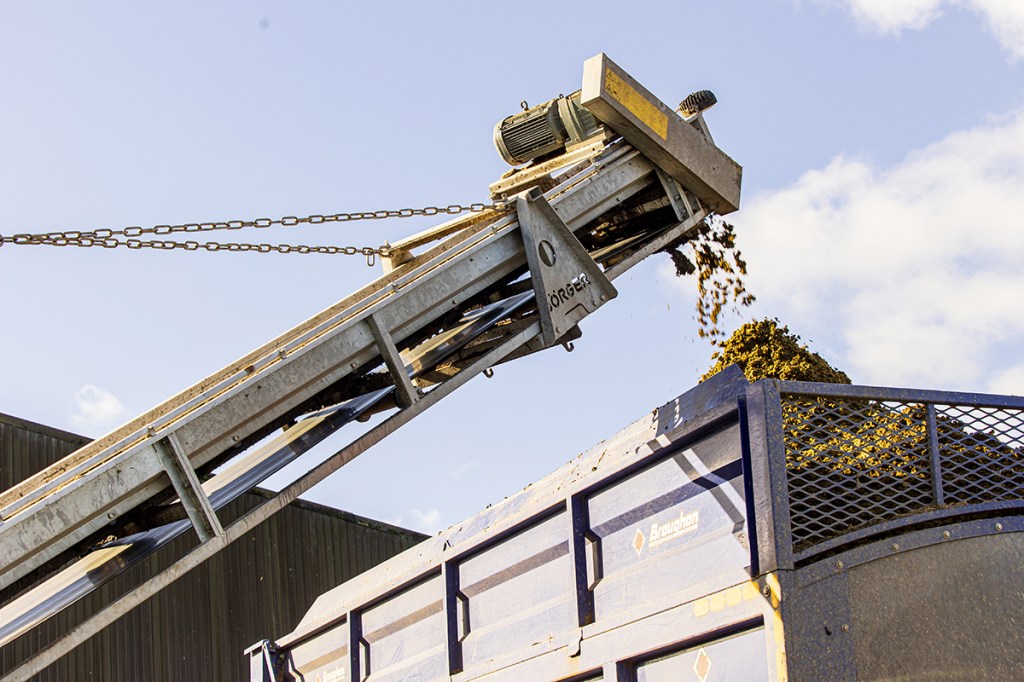
Andy chose the Börger separator for its output which is spec’d at 150m3/hr, they make smaller units, but the RC150 is the largest without going to a two barrel machine. It wasn’t conceived as a mobile separator but is offered by Börger as part of a complete unit if you want an off the peg solution.
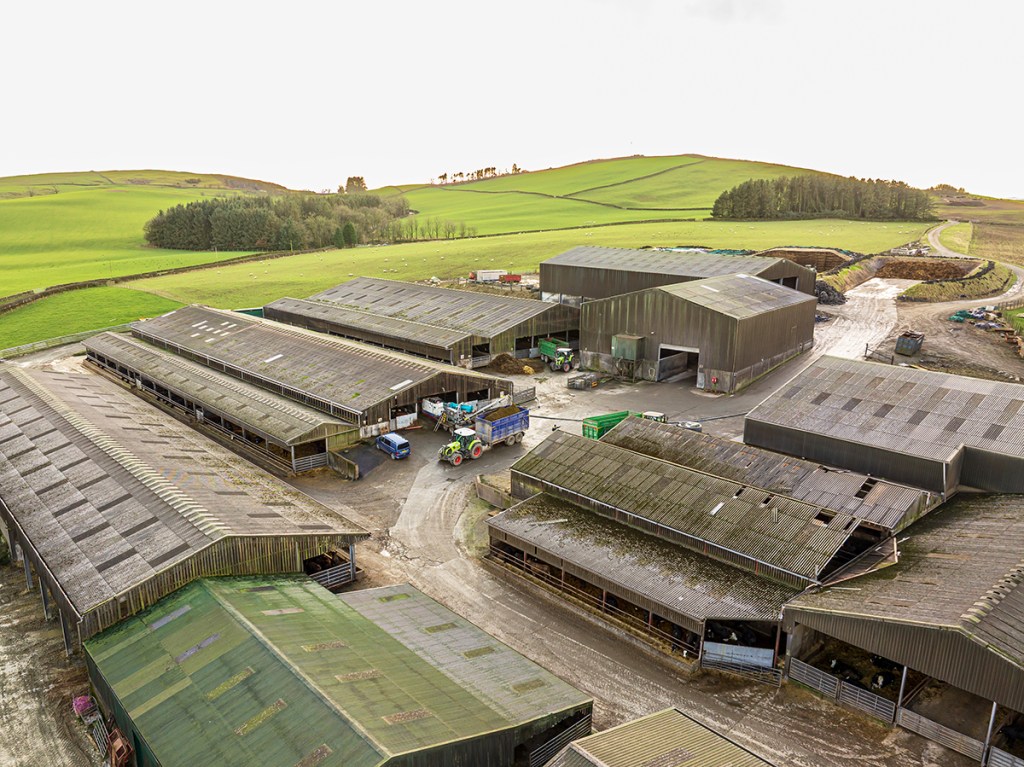
The package offered by Börger wasn’t the most economical solution, when looking at price breakdown, particularly to someone like Andy who had looked at the main components and has the ability to do some fabrication. Although the separator comes as a self-contained unit, in that it has the pumps, macerator separator and elevator. But requires a three phase electricity supply, which many farms don’t have, problem one, problem two, making it mobile.
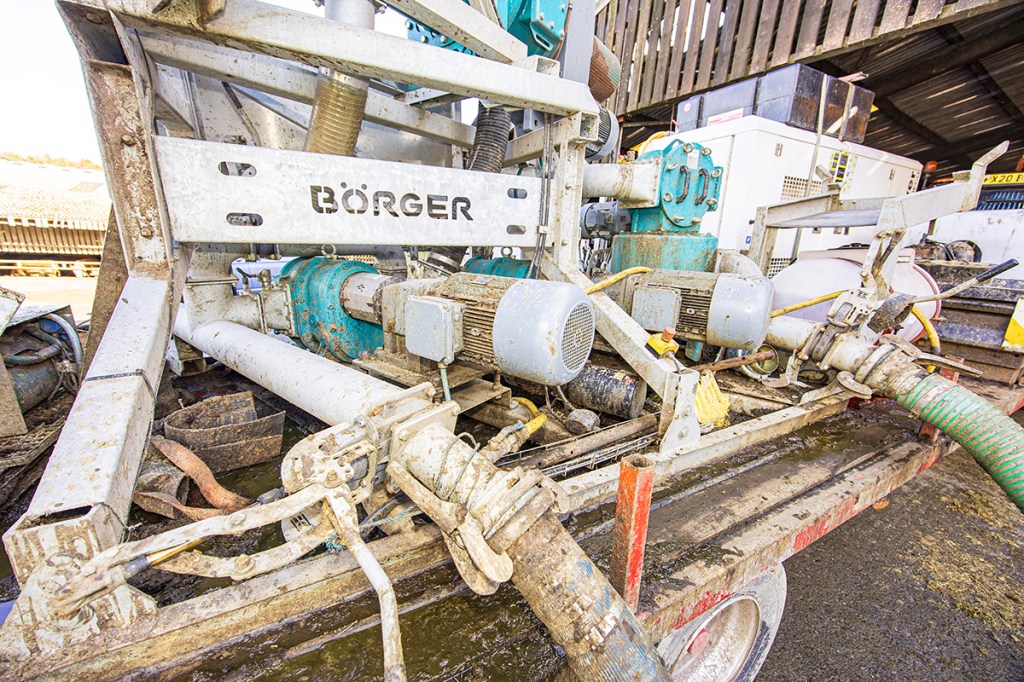
Like many contractors the G Rae team aren’t afraid of pulling out the welder and making something fit, after the separator was ordered, a 110Kva generator was sought out, and a trailer to put everything onto.
“We bought an eight metre Portequip bale trailer, which wasn’t a top spec trailer, and a self-contained Evopower generator pack, which we then set about grafting together,” recalls the contractor.
The separator arrived in October 2023, and the system was running by November that year, and was the first mobile Börger RC150 in the UK.
In Operation
As can be seen the setup is quite long, the generator is too long to mount across the bed, this does however leave space for the compressor, which is the only piece of the puzzle that wasn’t new.
There are inlets and outlets on either side, these were standard, Andy is able to switch to either side for filling without having to move the trailer. He has used Bauer couplings simply because there were plenty on hand having switched their umbilical systems to Storz. Suction hoses aren’t very pliable so some varying lengths have been made up for ease of handling.
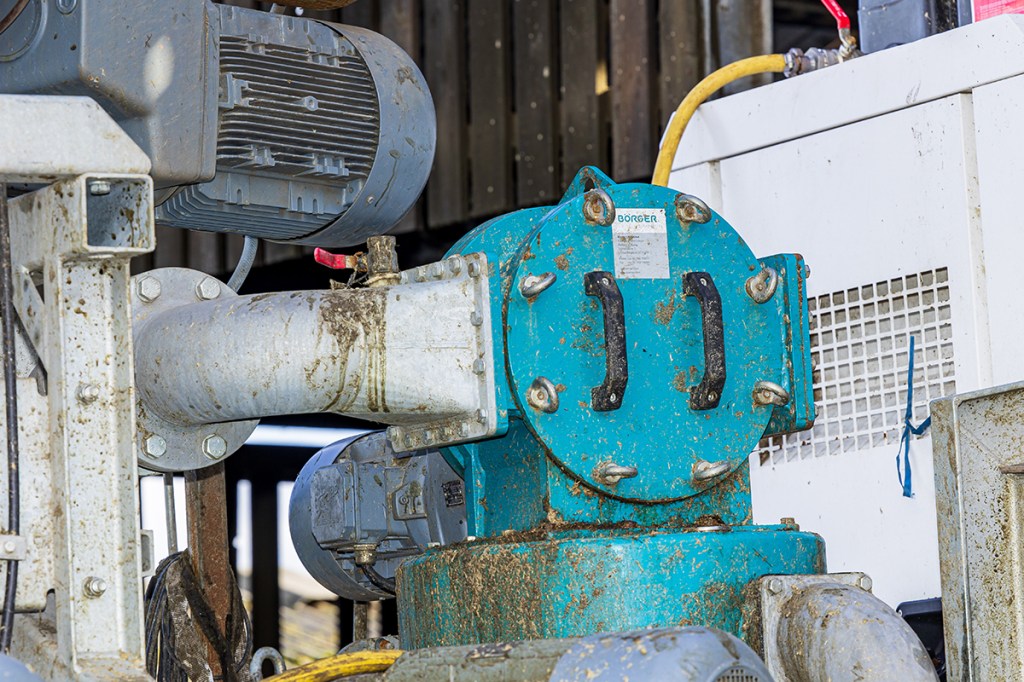
The Börger element consists of four main components, a macerator which they call a Rotorrake 6000, this is mounted on-top a 150-litre stone trap, a robust looking unit with a chopping action akin to a forage wagon. With stationary knives and a rotor with counter knives in the profile of a keyhole. Andy says it will munch through pretty much anything you’ll find in slurry; except the plastic clogs used by hoof trimming companies, these can stop it, and possibly caused the one broken knife he’s had.
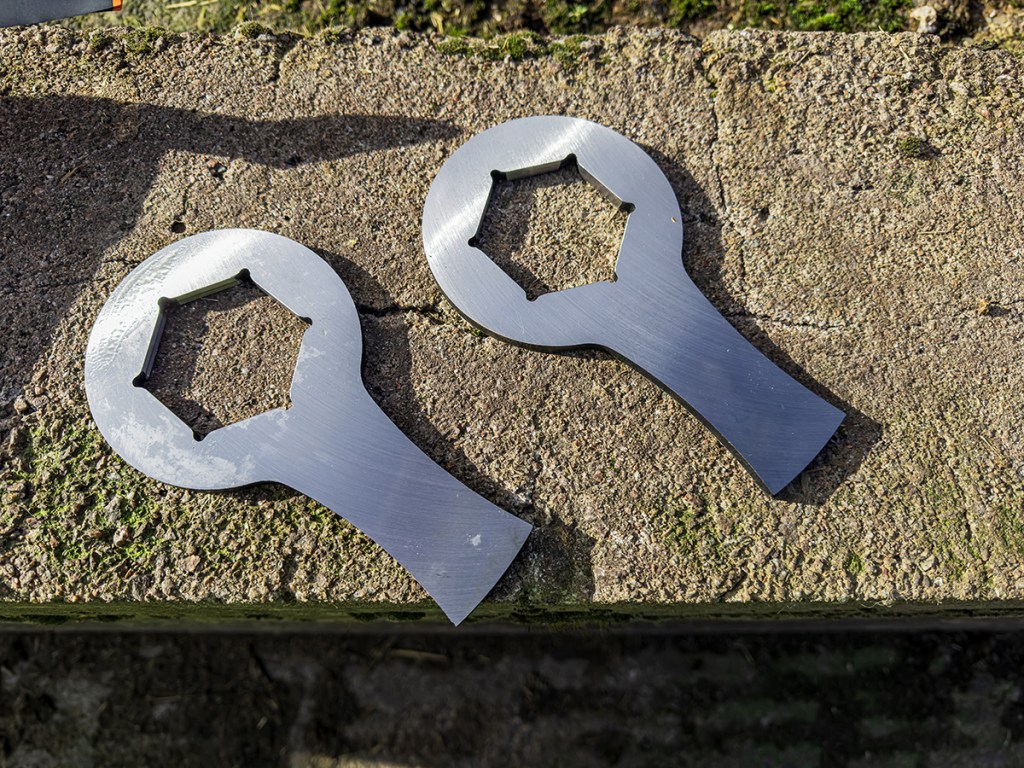
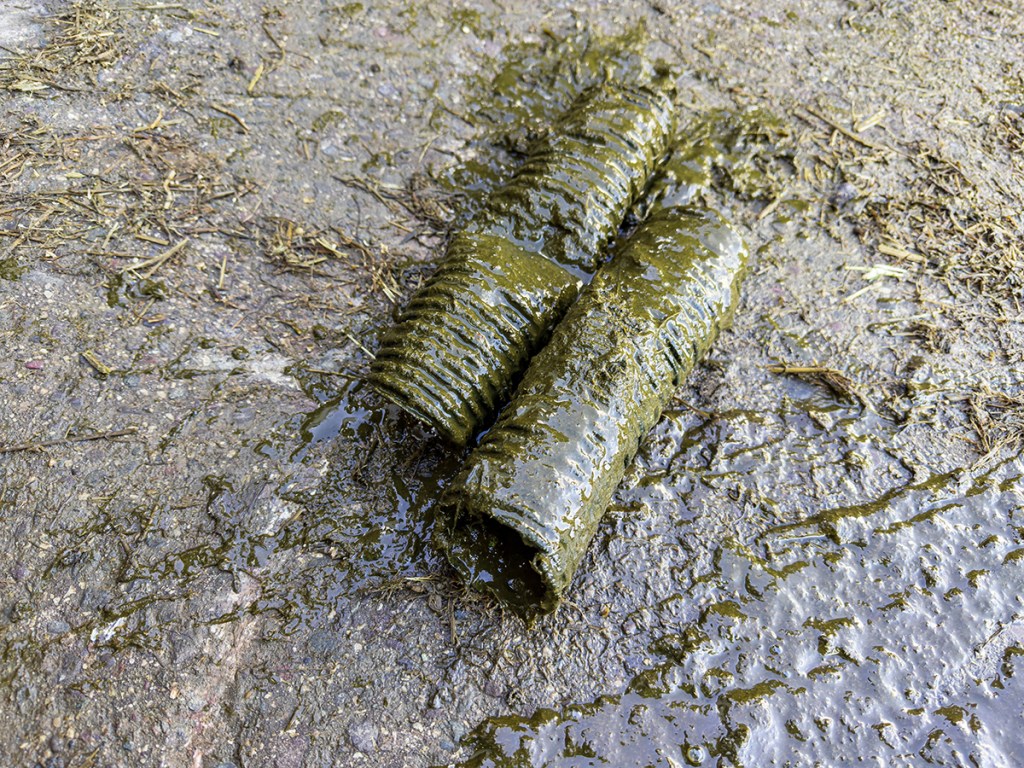
A feed pump is an FL518, a 150m3/hr lobe unit. This is a three lobe per rotor pump, positioned after the macerator, and pulls the slurry through the Rotorrake, so is exposed to more wear. Börger FL518 pumps feature replaceable casing liners as well as replaceable lobe tips, which should keep running costs sensible.
Richard Marcinkowski from the UK arm of Börger was present on our visit, he was able to run through the system’s operation after the macerator.
“The macerated slurry enters the main chamber of the separator where the auger conveys the solid material to the press channel area,” he explains. “The separated liquid flows through the wedge wire screen and is pumped away by the discharge pump to a lagoon/tank or similar for future use. The rotating auger has a groove on the flight which creates a regenerating seal as it collects the fibres from the slurry, this cleans the screen as it rotates. A counter bearing also stabilises the smooth running of the auger so there is no metal to metal contact in the Börger separator, which also reduces power consumption.”
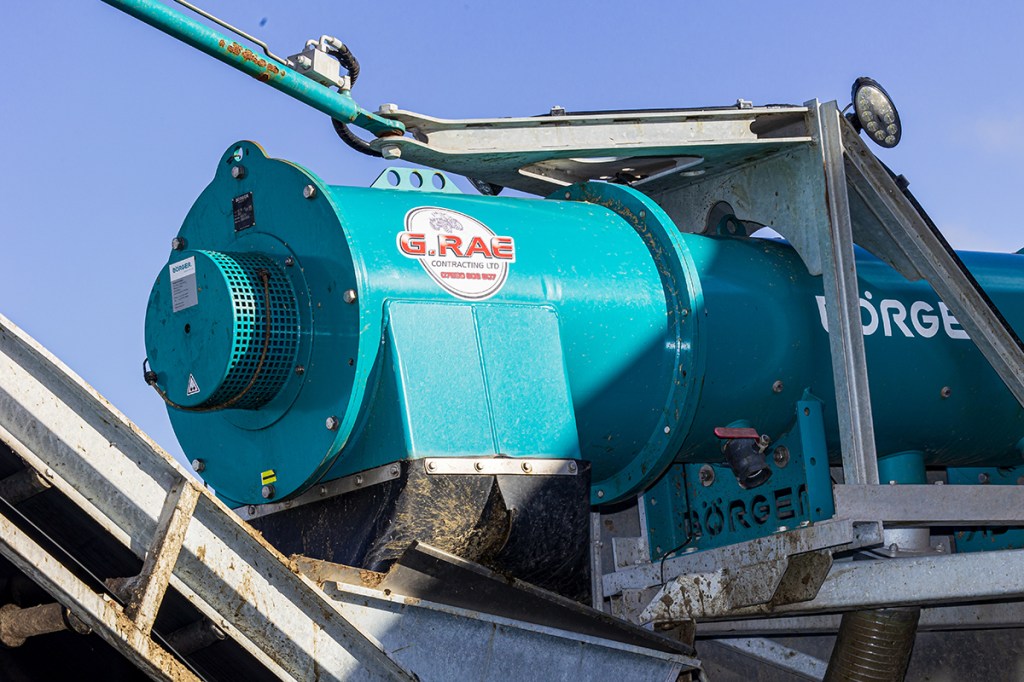
Feeling the squeeze
The separator runs at tens of revolutions per minute, you can see the Easy Shift pneumatic adjuster turning on the end, it works at a fairly stately pace. Andy opted for the air adjuster, this manages the gap at the high pressure screen end, a ring mounted on the auger tube can be adjusted via the touch interface to open or close the gap at the end of the high pressure screen. This is where the liquid is squeezed out, past this is the plug of solids that holds the material back which is what creates the ‘squeeze’. making a tighter plug for drier solids, or looser for wetter material. Without Easyshift, there are a set of bolts to adjust the squeeze gap, which are fine in a fixed environment, but can’t be adjusted on the fly like the air system.
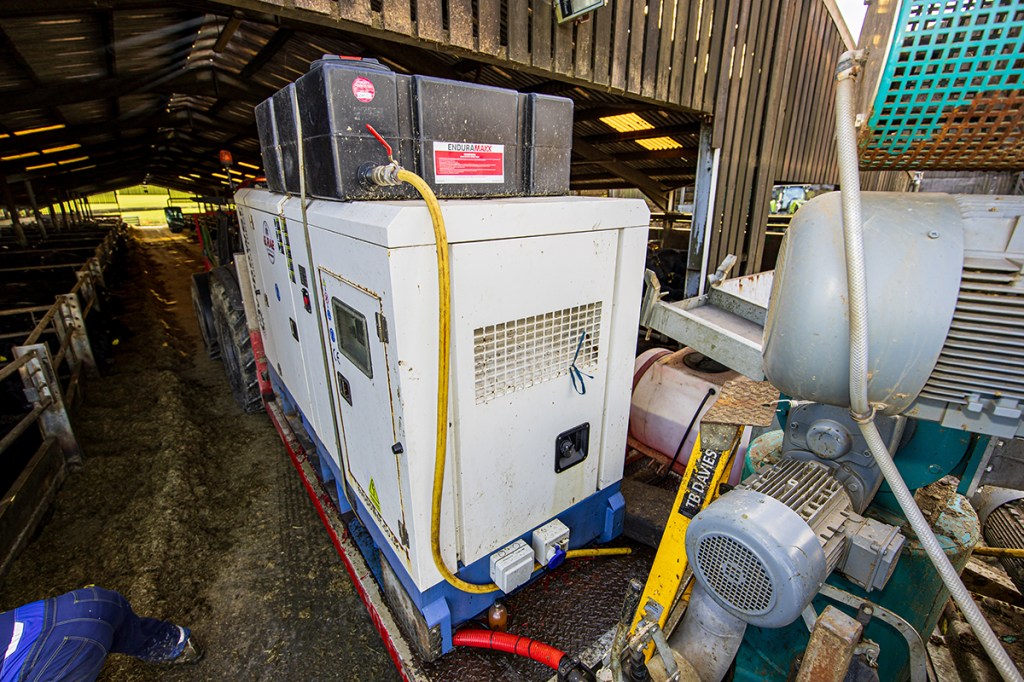
Andy fitted a water tank so if he needs to, he can purge the separator, either for mechanical or customer needs. As a future proofing idea, he thought that if a customer wishes to use the separated slurry as bedding, it would be beneficial to be able to wash out between jobs.

There is another FL518 pump taking the liquid element away, this typically runs between 0.5-4.0 bar which leads to one of the many questions we asked about the liquid being dispensed – no it can’t directly feed an umbilical system, the pressure and the flow are not sufficient to keep it going, even with a booster pump. The pump will, however, send liquid more than 850m. The store on this farm wasn’t that far away, but some new stores tend to be built well away from the buildings. The pipe running across the yard wasn’t as inconvenient as an umbilical pipe, with a maximum of four bar, it can be driven over, and as long as the vehicle doesn’t stop the separator will carry on, if the system senses more than a couple of seconds back pressure, it will stop automatically.
Solids are taken away by the elevator, which is high enough to reach into a silage trailer, or it can be stock piled.
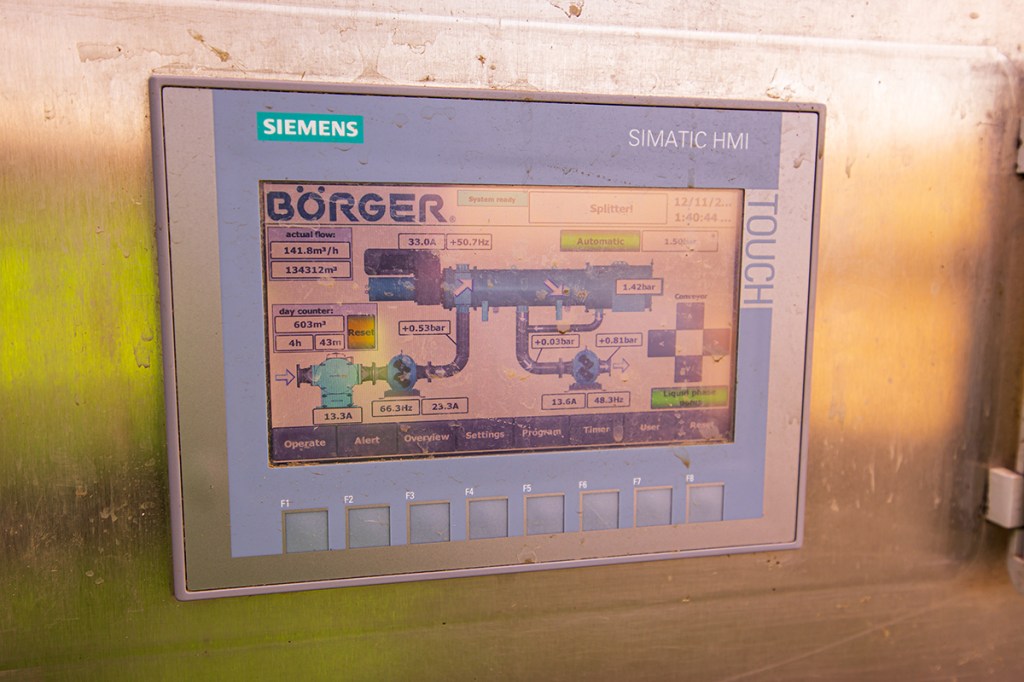
The system largely looks after itself, the Siemens touchscreen shows the status of all of the elements in the Börger system, showing motor current and line pressure in the different sections of the separator. The control panel coordinates the running of the feed pump, the separator and the discharge pump for optimal operating conditions.
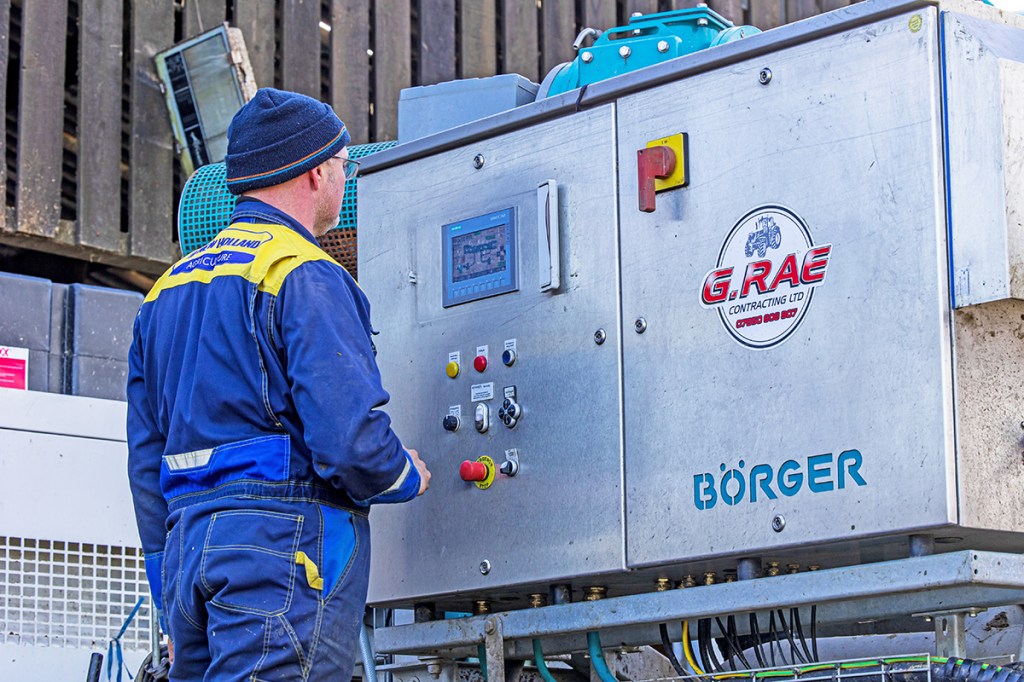
This is mirrored in a mobile app, connected via mobile network, the limiting factor being that only the discharge elevator can be adjusted via phone with an emergency stop. There is a computer based interface, which does give full control of the Börger element.
In terms of getting around and setting up, Andy uses a Valtra N174 with front linkage, using a small reeler for the lay flat pipes, the trailer is quite long but isn’t particularly heavy. Once on site, the tractor is turned off and the generator is fired up, it’s an electrical system, so there is a heavy duty earth lead, which can be clamped to a shed stanchion, or use a grounding rod hammered into the earth.
Early adopter
The farm we visited was one of G Rae’s first customers in 2023. It is a larger beef unit which produces 75 finished animals per week, so they produce a lot of slurry in their slatted houses. They have a mix of buildings, with some straw based bedding and the slatted floors where the separator was working. A multifaceted farming enterprise, with a business interest in a local anaerobic digester; the solids from the separator were making their way there by 15 tonne silage trailer load.
The farm exports the solids and some liquid for the AD plant, and in return they get digested solids. The finishing animals are on a mixed ration with plenty of grain, which still has gas to give after the cattle have digested it. The post AD solids are a high value product, with a good PH of 9.1 and more available nutrients than separated slurry solids from the sheds.
Beef and dairy
Not something that often crosses the mind, is the difference between dairy and beef slurry, which by Andy’s reckoning is about 10% fibre volume per cube. He reckons the slurry coming out of the beef shed can be close to 30% fibre, and he’s splitting that down, with the solids coming out at 22-24% DM. The building seen has an air bubbler system in the slurry tanks, which bubbles through the slurry to maintain a homogonous liquid.
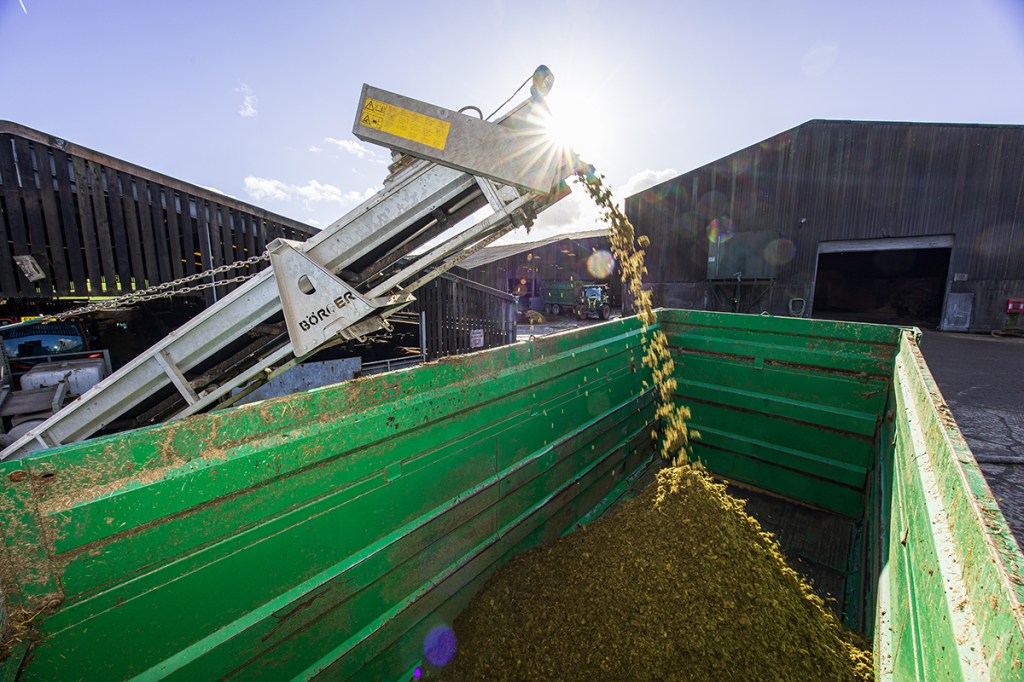
The separator was operating between 90-110m3/h which is fairly typical for beef slurry, in wetter material output is higher. The generator was operating at 40-50% load, which consumes 10l/hr of diesel. The system can squeeze the solid down to 38%DM, but this takes more power and noticeably reduces output, increasing fuel consumption to 12l/hr, not a huge jump, but throughput is more impacted.
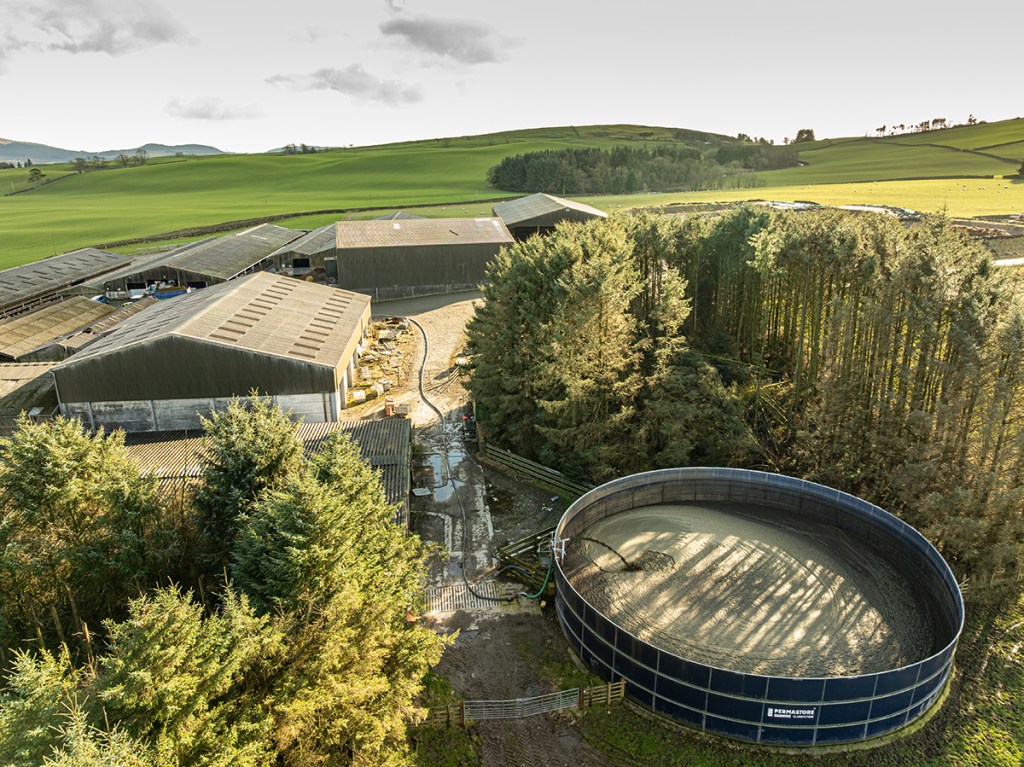
As well as the constant flow of liquid, being sent to the Permastore roughly ten tonnes per hour of solids was being produced. The trailers were taking the material directly to the AD plant while it was still fresh.
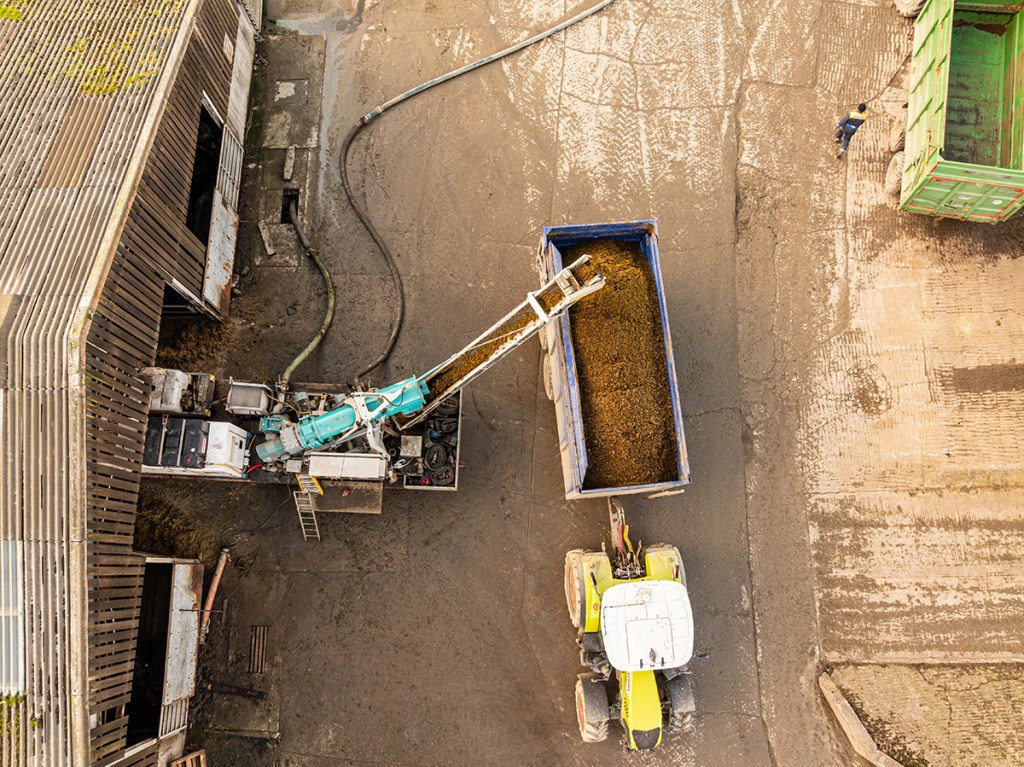
Spreading the benefits
As a contracting business that also carries out the field deployment end of slurry handling, G Rae have also seen benefits in the field, the separated solids are just about as uniform a product you could wish to spread with a rear discharge spreader. The business runs standard vertical rotor Bunning spreaders and are seeing great results in spread pattern and reduced stress on the machines.
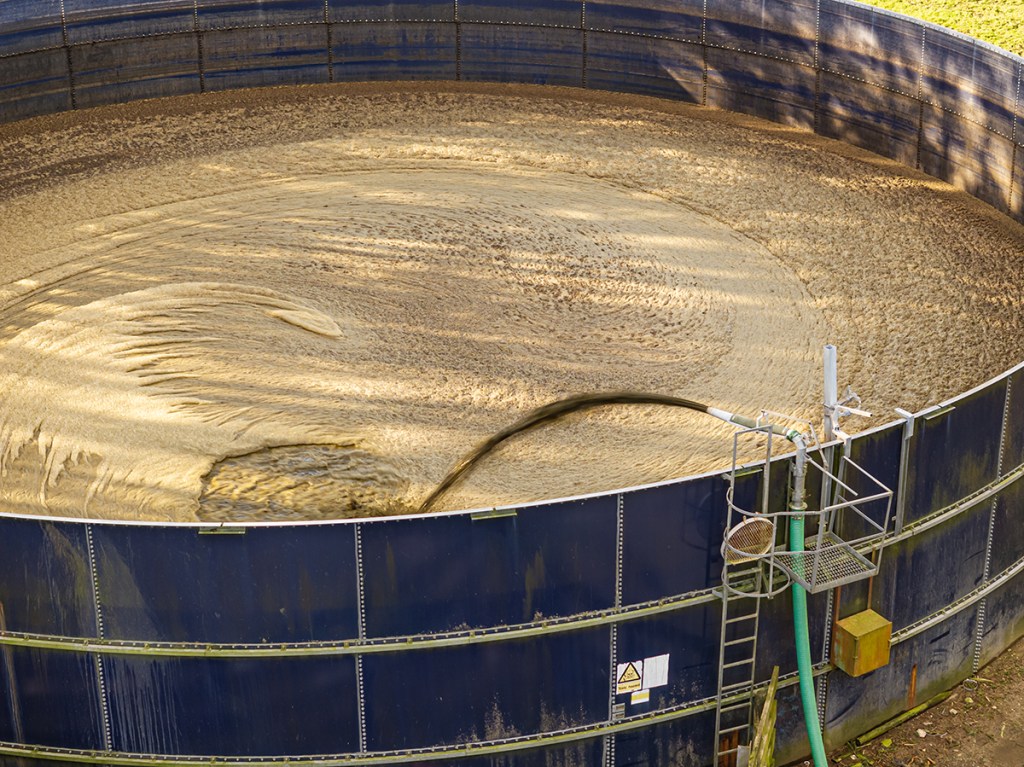
The liquid element is significantly easier to deal with, macerators can be slowed down and have little to no work to do, the material is easier to pump, and wear is reduced on the pumps as well as less power required to send it down the pipe.
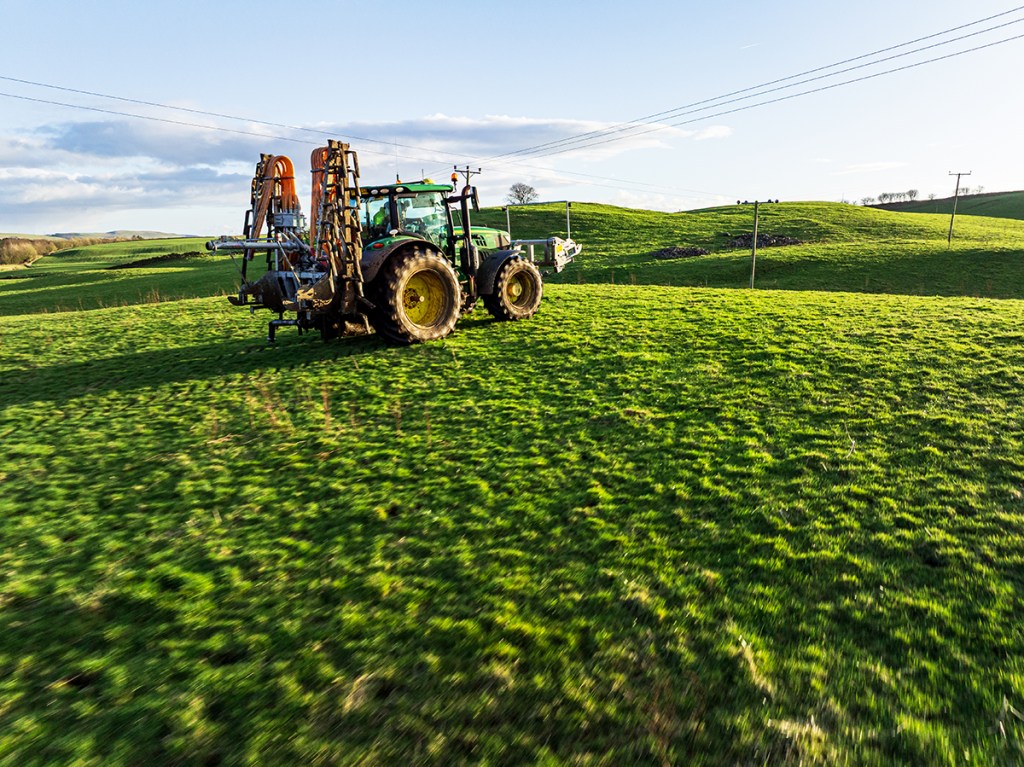
The most noticeable difference in average dairy or beef farm slurry is the amount of fibre residue coming down the pipe, and ultimately sitting in lines on the fields if the weather conditions aren’t suitably wet to wash it away. Ash content is becoming more noticed in grass silage, more from a perspective of slurry residue than soil, there are plenty of arguments around splash plate versus dribble bar. The certainty is that after this year, you won’t have a choice in the UK, separated slurry disappears in the pasture and in dry conditions is favourable to prilled nitrogen for optimal take up by the plants.
Expected life
How long is a piece of string springs to mind, Börger estimate in sand/grit free material, that the screw and screen should last 8,000 hours. These are the heart of the separator, but are fairly easy to change with some lifting equipment.
With extended biogas plant installations, they have a good idea of working lifespan, with many working 24/7. They have extensive knowledge with varying materials going through their equipment and how each affects the life of the components.
The estimate is that separating slurry from a sand system will shorten the life of the internals by approximately 30%. Even though there is no metal to metal contact, the self-replenishing seal will inherently cause accelerated wear if sand is involved.
Andy’s system is approaching 1,500 hours since November 2023, and says he’ll be happy if he gets 8,000 hours. So far he’s only had to replace one macerator counter knife due to breakage rather than wear. The feed pump has had two new sets of lobes and liners, as it handles unseparated slurry with the debris and fibre it contains.
Workload
From the concept Andy thought it would be a service that would run alongside what spreading is allowed through winter, but it’s grown into a five days per week roll for himself and another operator. In the spring and summer months it drops down to three days, which does require some juggling when grass harvest is in full swing.
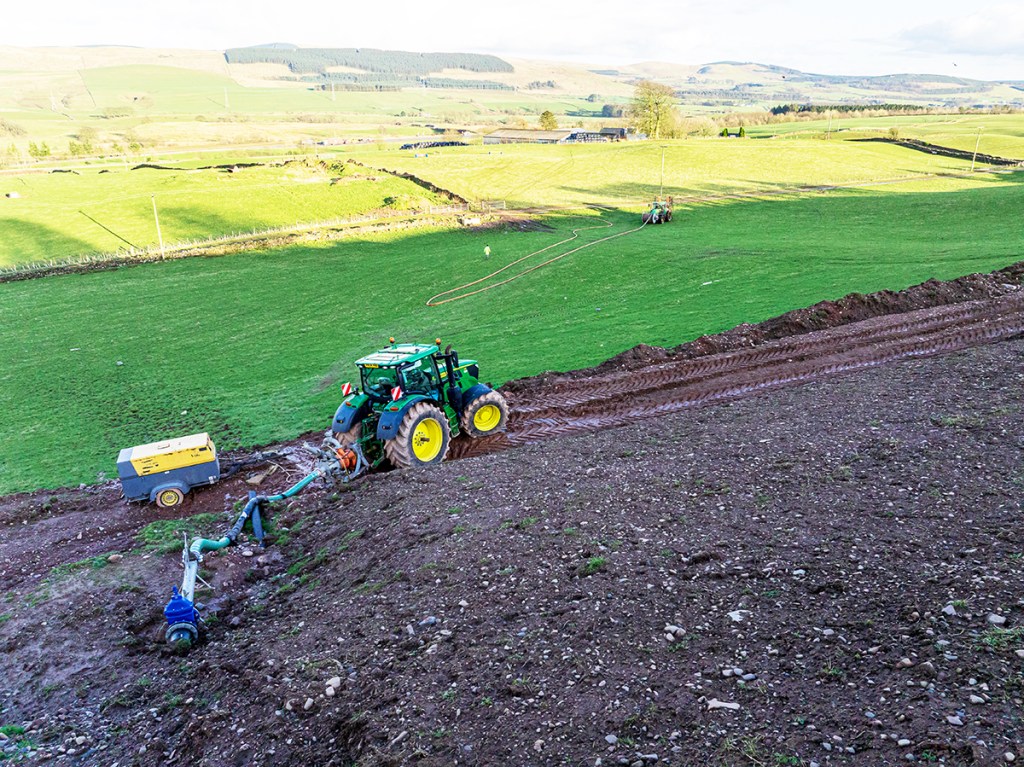
What started out as a leap of faith for G Rae Contracting, has turned into a full time job in the winter, that can usually be done on a concrete yard. The concern over farmers fitting their own systems has mostly been subdued, as the type of work being done is not suited to a stationary separator, it’s also a useful service to farmers who don’t need it all of the time.
The benefit of separated slurry in both increasing storage which can be between 20-25% and producing two products that are more useful than their base state is also being recognised by contractors and customers. Ease of spreading, better nutrient uptake and reduced ash content in grass silage are also key benefits.
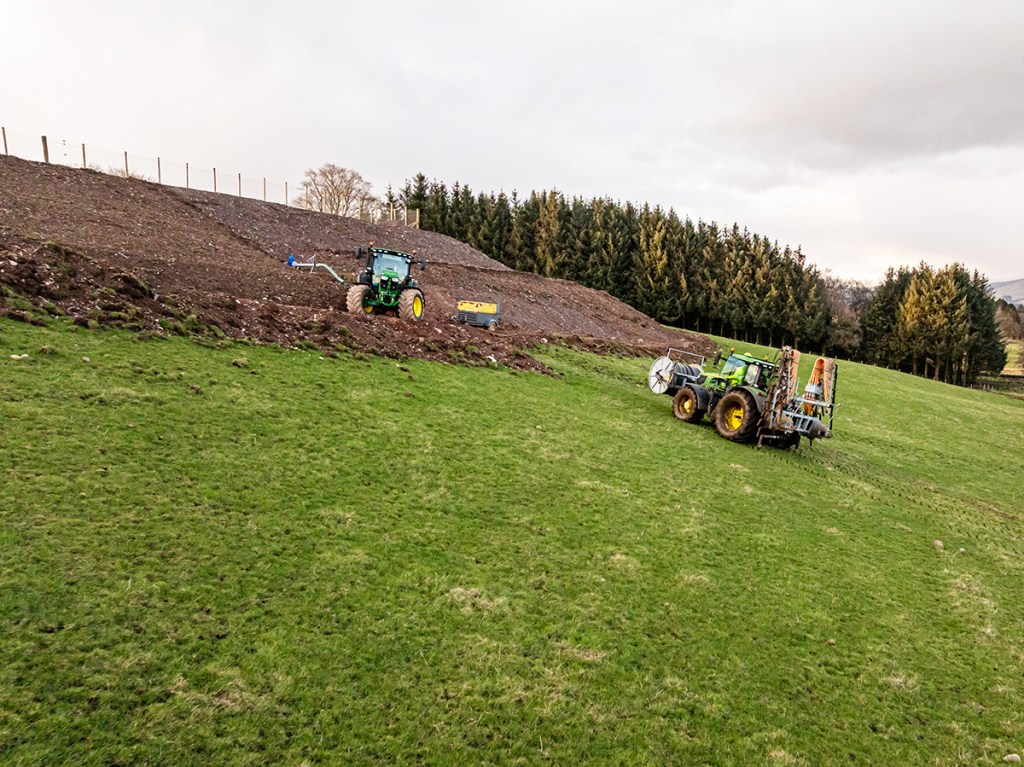
Ken Topham
For more up-to-date farming news click here and subscribe now to profi and save.