Peecon surprised visitors to last year’s EuroTier, where it had a new type of self-propelled feeder on show. A conventional tractor had been kitted out with a self-loading boom for the diet feeder behind. Our colleagues at Dutch machinery magazine Trekker were able to see the prototype in action.
KEEPING IT BRIEF
- Peecon has developed a milling head and self-loading boom to turn a tractor into a self-propelled feeder.
- Future versions will not require loader brackets on the tractor.
- The milling head is driven hydraulically by a pto power pump at the rear.
- The Peecon Pacman Gen2 was a self-propelled feeder based on a forklift. We looked at it in profi 10/2016.
It was, and still is, a genuine eye catcher: Peecon once again wowed showgoers with some out-of-the-box thinking. This time, it was a novel forage milling head that transforms a regular tractor and diet feeder into a self-propelled outfit. Although it looks big, the milling head doesn’t stick out any farther than a standard front loader with a shear grab.
The Biga Rapide XL-V, as it is called, is still in the early stages of development. Indeed, at the time of the exhibition, it hadn’t even worked ten hours. Nonetheless, the concept was already working very well. And the reasoning behind the project: Peecon says that smaller farms are reluctant to invest more than €200,000 in a self-propelled diet feeder. Which is something the Dutch firm should know first hand, as it also makes self-propelled feeders.
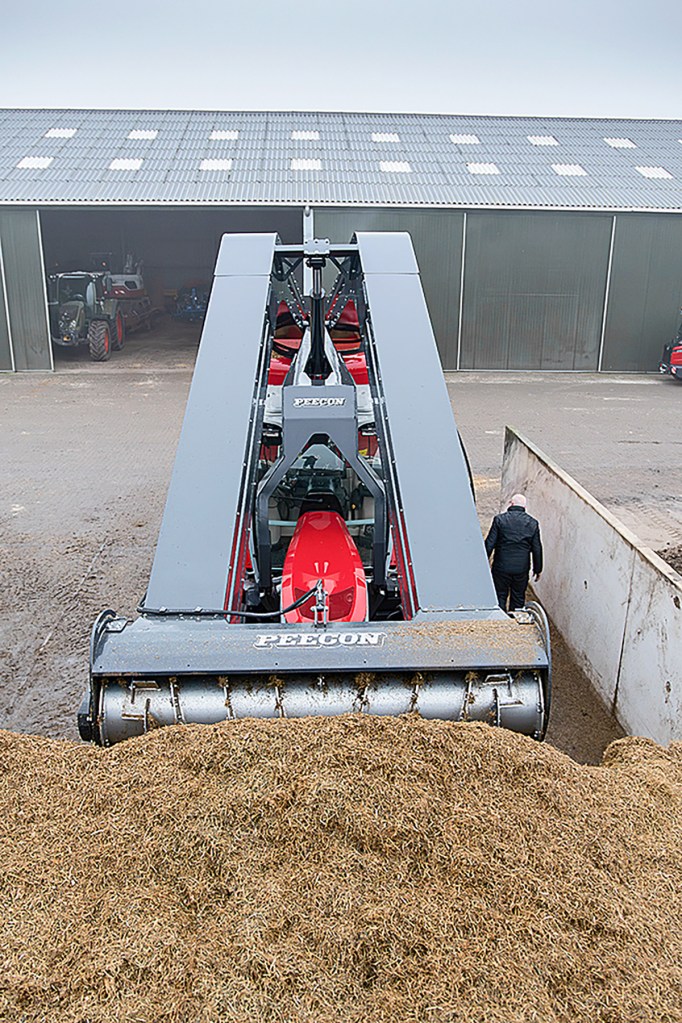
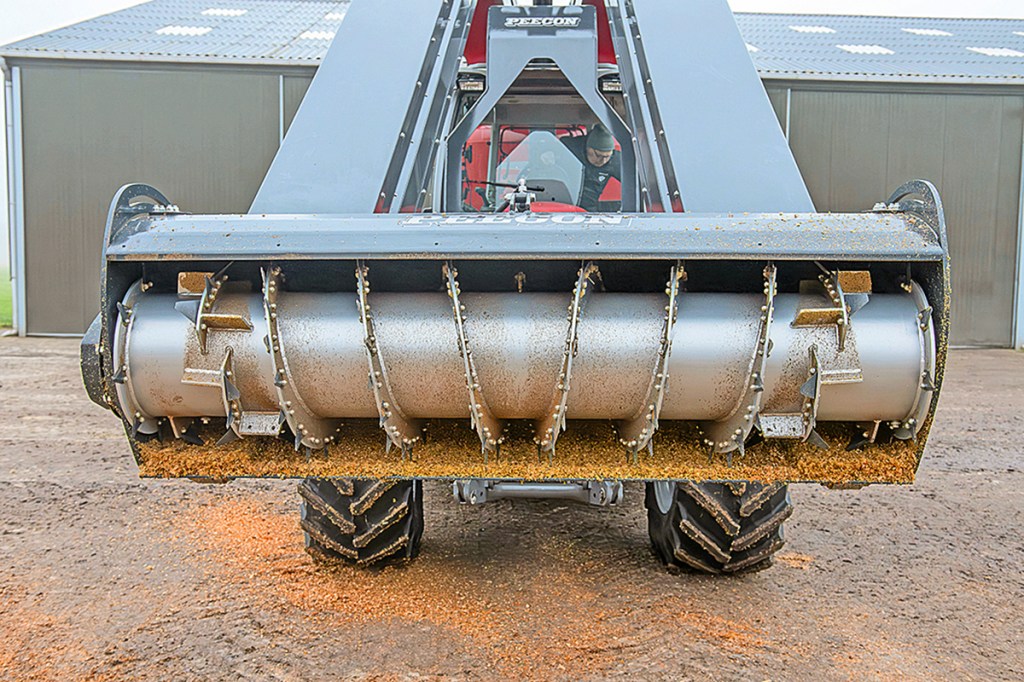
Two feed passage arms
The 60cm diameter, 2.40m wide milling head for removing silage from the clamp face is Peecon’s design. This is different to on its self-propelled Rapide mixer, which actually uses a rotor supplied by Storti. The reason for the change is simple: for this machine, the flights on the rotor need to direct the material to the left and right so it can be taken away by the conveyor belts running up the sides. With this approach, there is no requirement for an auger behind the rotor, as on the Storti-sourced unit, helping to save weight and cost.
The feed is thrown onto two belts, which are concealed inside the solid-looking boom structure positioned over the tractor cab. Each of the seamless belts is 40cm wide and 14m long, bridging the 7.0m distance to the mixing tub. Peecon says that the belts are self-centring, whereas the belt tension is set manually by adjusting a bolt. Working at 5.0m/sec, it takes 1.5 seconds for material to travel from the rotor to the tub, Peecon pointing out that this high speed should prevent any blockages.
As the belts are powered by the tractor’s hydraulics, the speed can be adjusted by altering the oil flow.
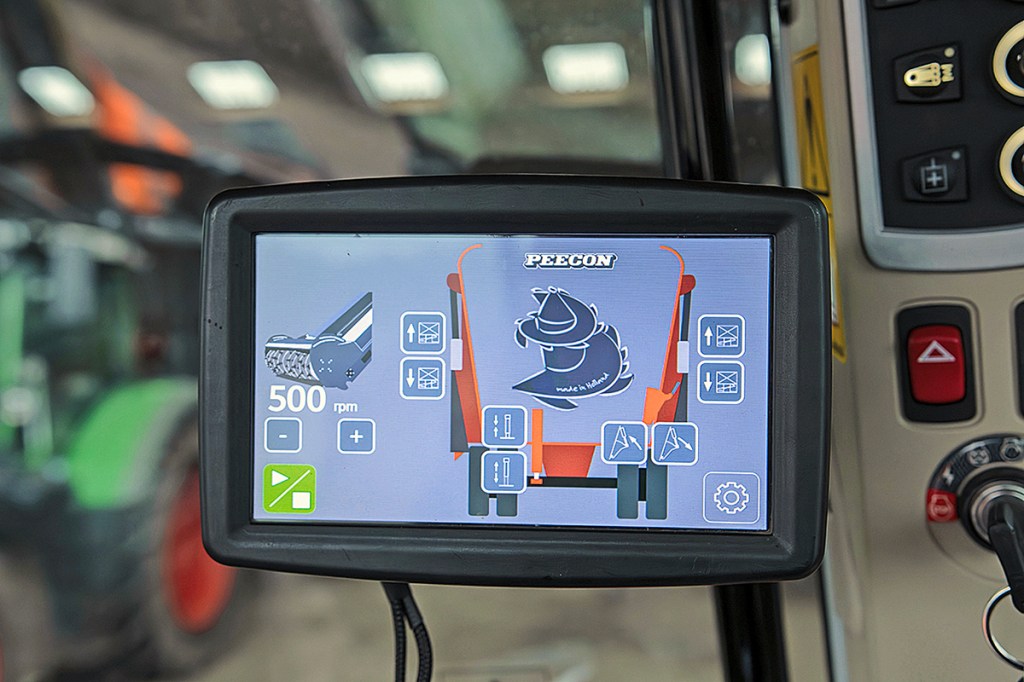
Both the belt and the rotor are monitored by sensors that measure hydraulic pressure and belt speed to show what’s happening and pre-empt a potential slow-down and feed blockage.
The single-acting lifting cylinder for raising and lowering the boom is also supplied by the tractor hydraulics. Because the boom pivot is located so far back, the chomp on a clamp face is almost vertical — even at the boom’s maximum removal height of a lofty 5.80m.
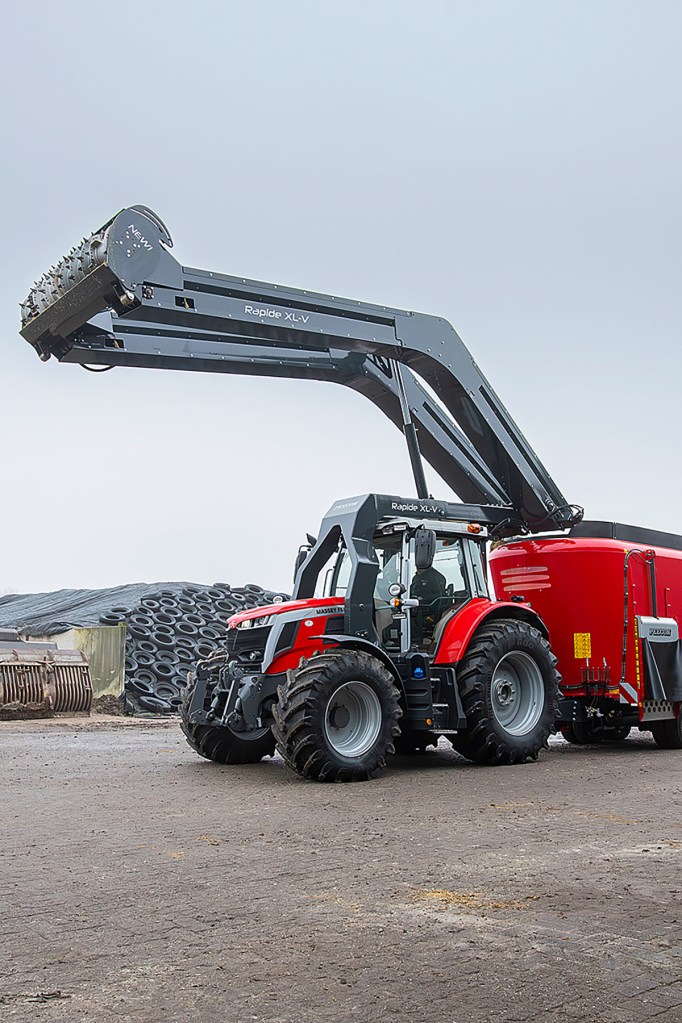
The outfit must be positioned in a straight line in front of the pit face; if not, it won’t feed the silage into the tub. Peecon would like to refine the system so it can still load when in a turning position. As for steering angles, the boom increases the tractor’s turning circle to the same extent as a front loader.
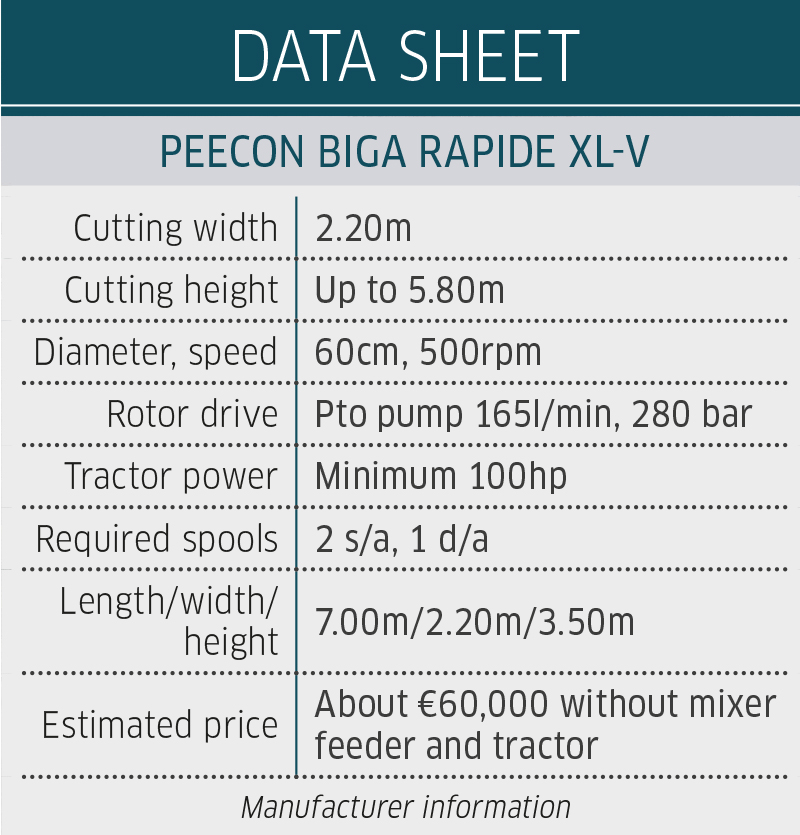
Structural changes
Peecon estimates the current weight of the loading system is around 2.5 tonnes. In future, the company plans to save weight by using less but harder material. It also wants to eliminate the front loader brackets to improve the less-than-perfect visibility and also simplify taking the unit on and off. The firm’s goal is to ‘undress’ the tractor within 15 minutes, though it didn’t want to reveal to us what the future design might look like without the brackets.
100hp rotor input
The rotor is supplied with oil by a high-pressure pump, which is located at the rear on an intermediate gearbox on the pto drive shaft to the mixer; here the 1,000rpm speed is increased to 3,000rpm for the pump. The pump can then deliver 165l/min at 280 bar pressure. This means the rotor is still part of the mixer wagon. In future, the design team wants to integrate the pump into a frame that supports the rotor behind the tractor cab. The rotor currently has a power requirement of 100hp, but this is definitely at the lower limit, especially since the mixer has to be operated at the same time.
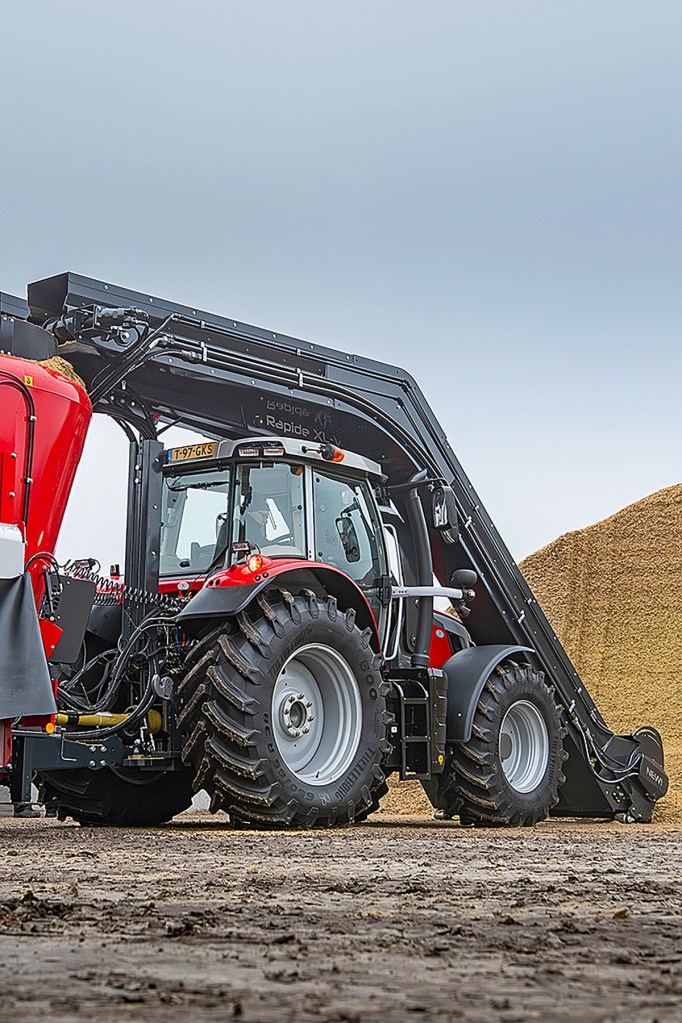
Final version at Agritechnica
For now, it can only estimate the costs of the unique self-loading system. The larger XL-V version is expected to list at about €50,000 to €60,000, and a smaller version could be about €35,000 to €40,000. One way or another, the concept is certainly different. And you still need to include the price of the tractor and diet feeder. Yet this unit could be used with any type of tractor or diet feeder, something that is not possible with a dedicated self-propelled. It will be interesting to see what the reaction is from farmers. Will they be willing to stump up the cash for such a machine?
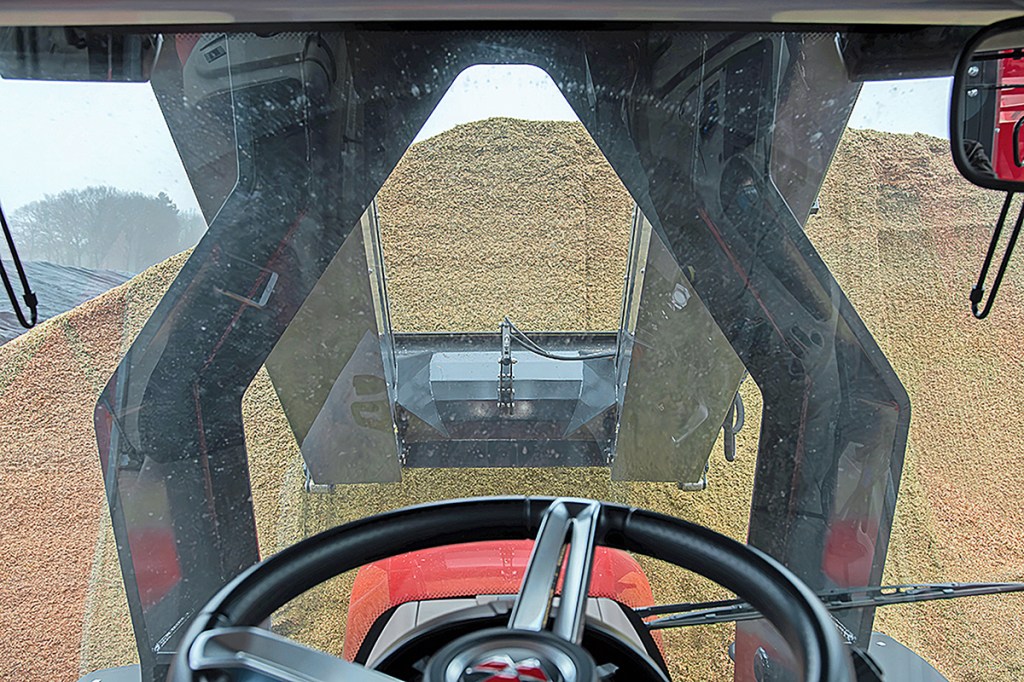
Summary
The Peecon Rapide XL-V milling head and boom design transforms a standard tractor into a self-propelled feeder. Admittedly, there are big compromises on visibility and manoeuvrability, but the idea is very new and it’s up to farmers to decide whether such a ‘retrofit’ silage removal system will revolutionise the market for trailed diet feeders. We are excited and will keep you informed on how the project develops over the next five years.
Jacco van Erkelens
For more up-to-date farming news click here and subscribe now to profi and save.