Photoheyler’s hoe even works between the plants in the row, using camera-controlled blades to slip in and out. And there’s an interesting approach to steering, too. We catch up with the recently founded manufacturer to delve into the detail.
KEEPING IT BRIEF
- The system employs AI as one means of recognising the plants.
- Photoheyler is able to cultivate in the row as well as between them.
- Image analysis is used to control the rotors within the rows.
Organic farmers are always looking for fully automated alternatives to manual weeding within crop rows. Stefan Heinrich and Thomas Stangl from Bavaria developed a solution based on Stefan’s doctorate. The concept was awarded a silver medal at Agritechnica in 2021.
Now the four-person start-up has almost 20 machines working in countries including the Netherlands, where Dutch magazine Trekker was able to accompany the Photoheyler as it was weeding a patchy stand of valerian spaced on 50cm rows in an undulating field. Despite these generally adverse conditions, the machine did an effective job.
Technical structure
Each hoeing unit is depth-controlled by a wheel-guided parallelogram. An additional parallelogram is fitted with a rotor mounted at a 30° angle and equipped with a total of four camera-controlled blades — this is what clears the weeds that are growing between the plants. Ultrasonic sensors and hydraulic cylinders control the depth of the rotors, while the penetration depth is set on the in-cab terminal.
The hydraulic cylinders allow the individual lifting/lowering of each unit, either manually or via section control. The springs on the parallelograms exert a light pressure on the hoeing tines.
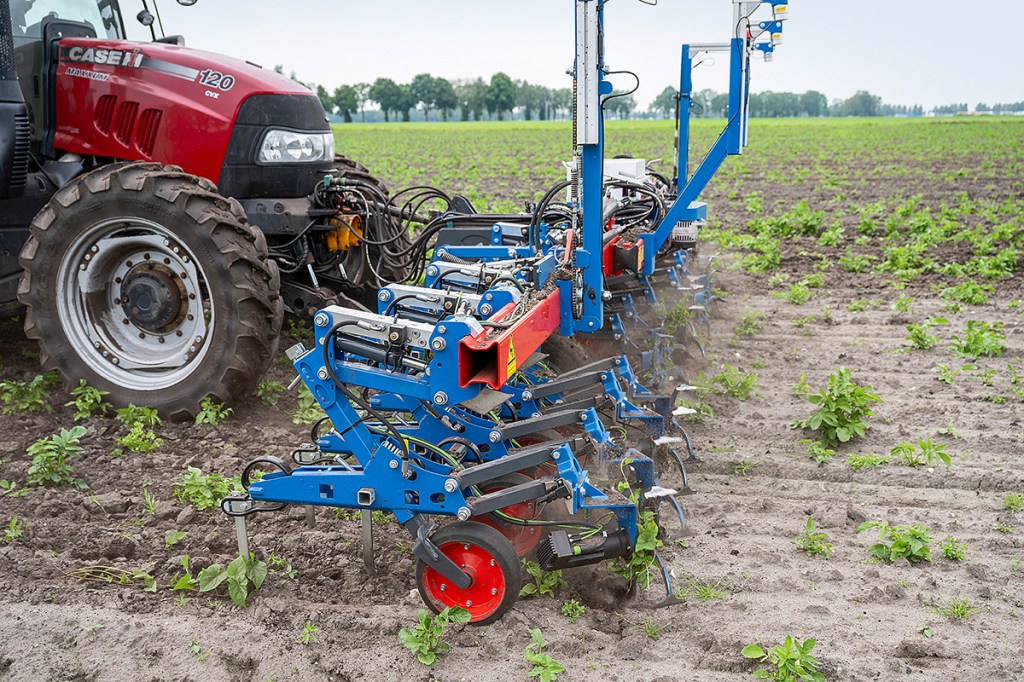
With the rotors in their raised-up position, it is also possible to use the machine as a conventional hoe. When raised, the ground clearance is 20cm, but this can be increased to 35cm when the tines are removed.
The system is suitable for row crops growing on a 45, 50 or 75cm row spacing and an inter-row plant spacing of at least 10cm. Various tine widths (7 to 22cm) are available from Photoheyler.
You can also set on the terminal whether you want the rotors to move one, two or three tines between the plants. When the system detects a double, the rotor stops briefly to protect the crop.
Training the weeder
Photoheyler has already stored numerous crops in the system; however, new plants can be added within a few hours. To do this, the user first drives the hoe over the crop and takes photos. With these images, the user or the development team can train the system with the new target plants with a click of a of mouse in a web portal.
The resulting data is later transferred to the control terminal using a USB memory stick. Access to software updates is also possible wirelessly via a mobile hotspot.
Better than the human eye
The earliest growth stage of a crop that can be detected by the system depends on the type of crop. Sugar beet plants, for example, can be detected as early as the two-leaf stages, and for onions the whip stage is sufficient, say the developers. A realistic forward speed in this growth stage is up to 2km/hr; later on, this speed can increase to up to 3.5km/hr. Image recognition can be performed with or without AI, although the latter is particularly helpful for overlapping leaves or when plant and root centres are actually out of centre.
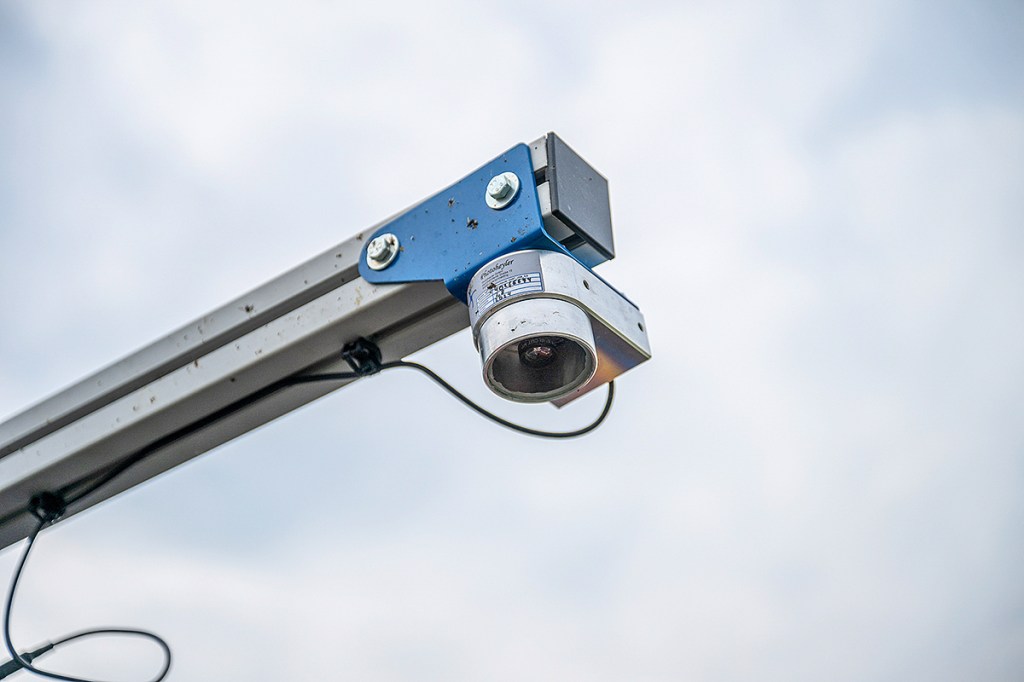
The developers built both the cameras and the data structure, and their solution requires no on-board job computers. Instead, all the camera and control signals are transmitted through a network and USB ports to the tablet computer, which also serves as an operating terminal. The mechanical parts of the machine are also manufactured inhouse by Photoheyler, whereas the main frame is sourced from Hatzenbichler.
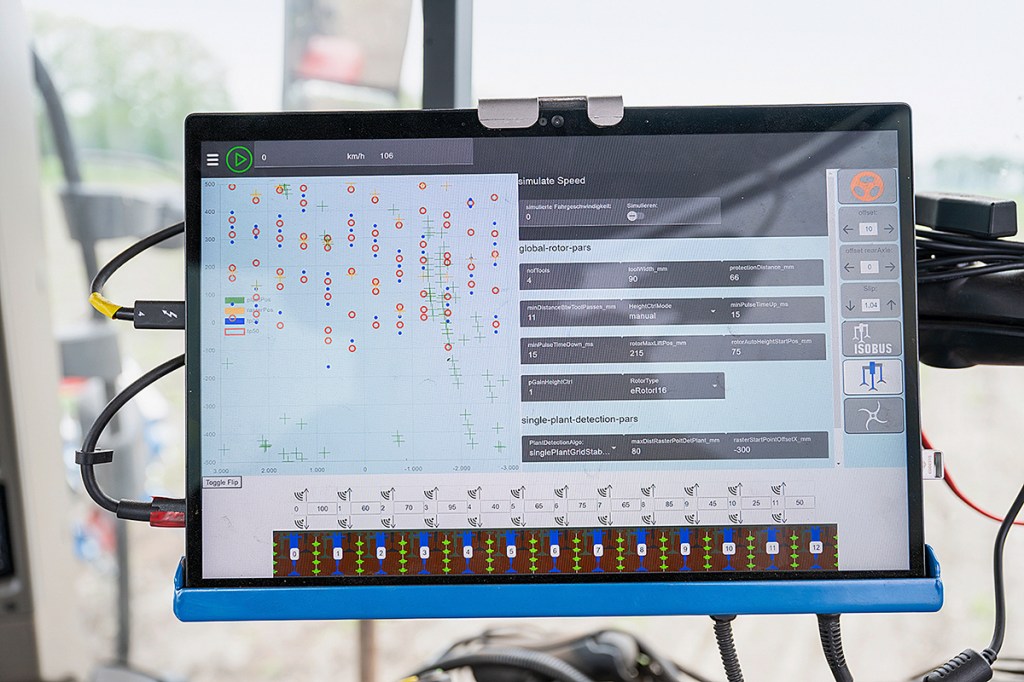
Steers the tractor
The cameras that look on to two to three rows are also used for auto guidance. The Photoheyler unit hydraulically steers the guidance wheels under the hoe frame and it also steers the tractor — a unique feature. This solution improves tracking on sloping terrain and reduces lateral drift — great for weeding in narrow row widths.
For tractors equipped with RTK steering, Photoheyler can usually access the steering system through the TIM-Steering ISObus function. Otherwise, the firm offers separate steering valves. When camera steering is enabled, the tractor will follow the weeder; when manual steering is enabled, the weeder will follow the tractor. An adjustable offset is possible when camera steering is enabled.
Differences in system
The manufacturer says its solution offers several key advantages over other in-row weeders. For example, due to the way the blades spin across the rows, this means there is very little soil throw in the direction of travel. Another is that the front-mounted design allows for a compact layout while the cameras provide a large field of view. The 6.0m wide, 1,650kg machine protrudes out 1.20m when measured from the middle of the lower links.
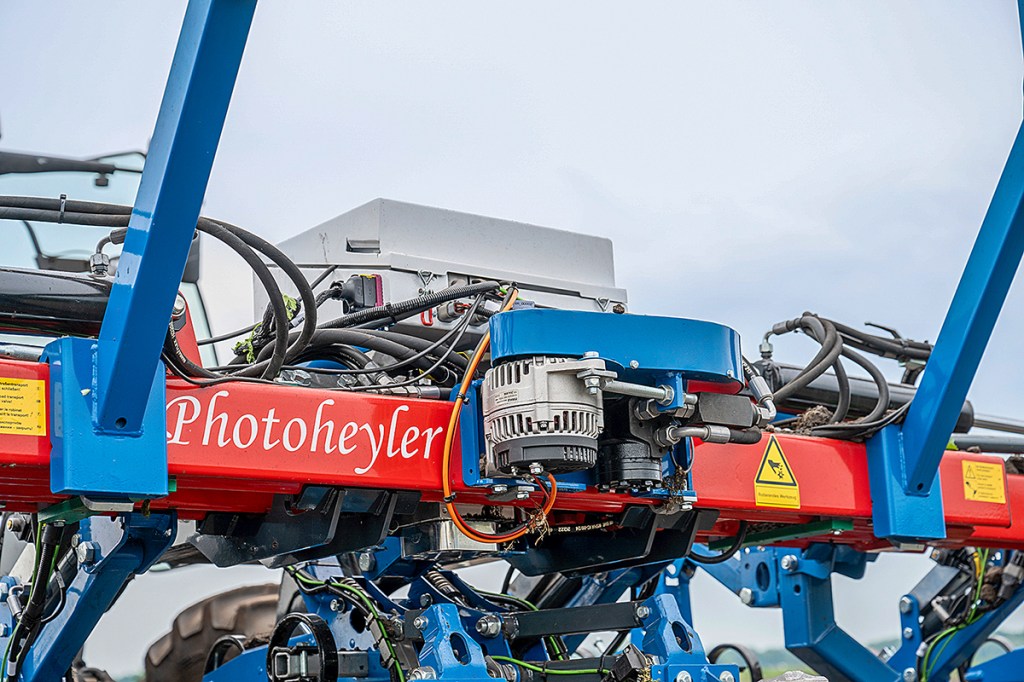
Other details
- The electric rotor drives are powered by a 48V alternator that is load-sensing controlled.
- Up to now, Photoheyler has mainly built 6.0m machines and one 9.0m version.
- In AI camera specification, the machine can also be kitted out with a camara-based solo steering system for the tractor and the side-shifting platform as well as a potato sorting system. Initial trials with a spot sprayer and laser weeder are also underway.
- The weeder is not AEF-certified, but the developers still refer to ISObus integration and Aux-N functionalities.
- The rotor motors deliver 100Nm.
- LED headlights are required at night.
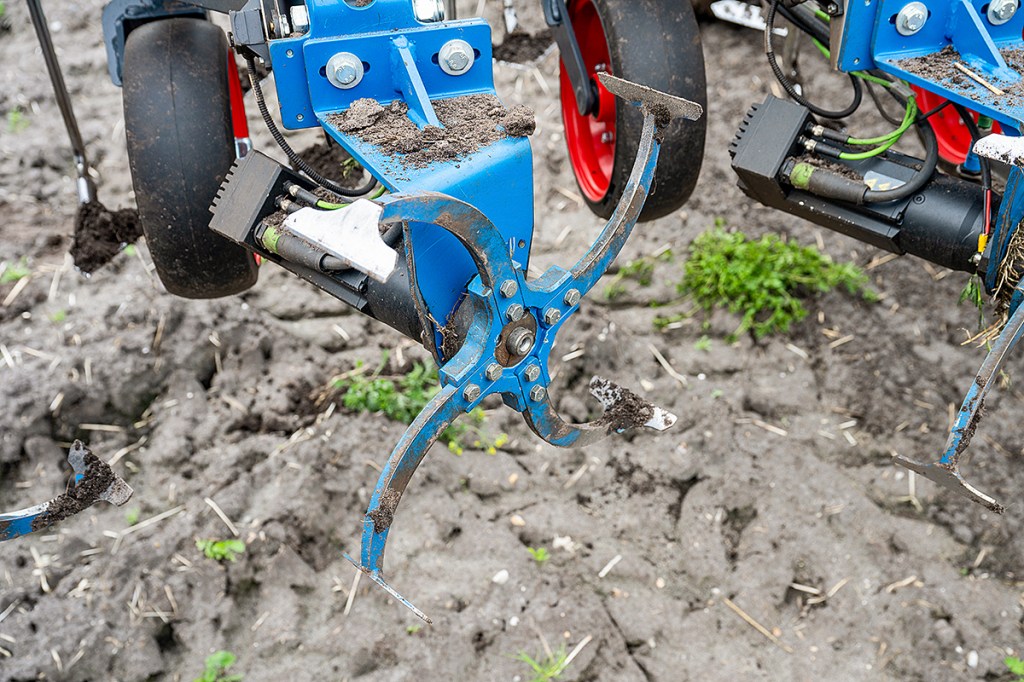
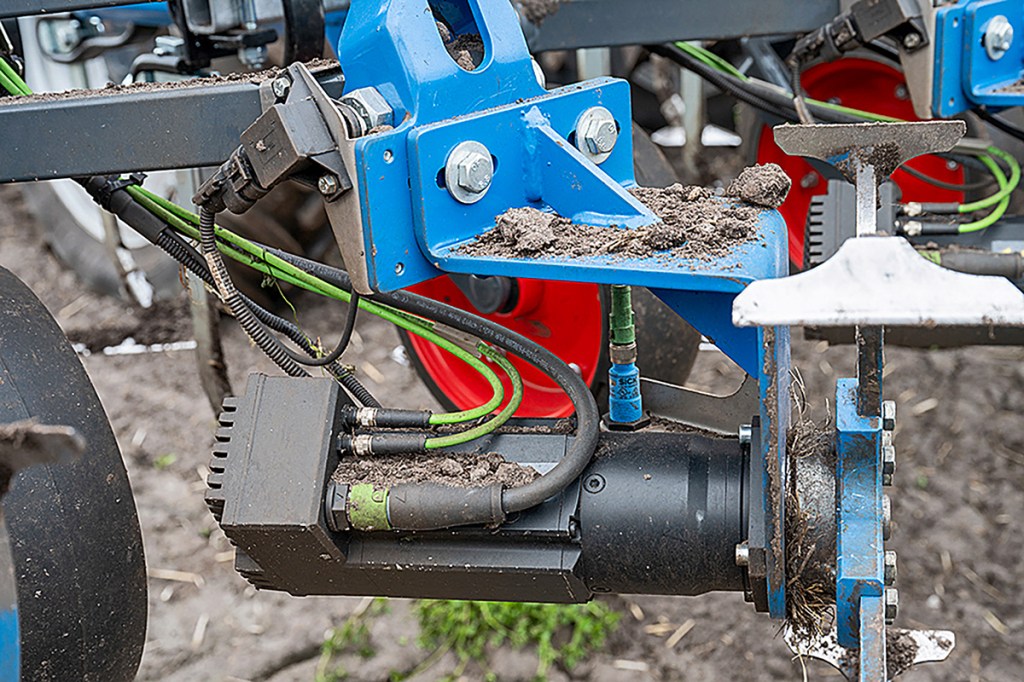
Summary
Our colleagues at Trekker used the optional AI-supported in-row and inter-row weeder from Bavarian manufacturer Photoheyler in a stand of valerian.
Unlike other in-row weeders, Photoheyler uses a horizontal rotor with knives. Powered by electric motors and camera-controlled, the knives move in between the plants. In valerian, the system was able to achieve good results despite a patchy stand. Typical ground speeds are between 2 and 3km/hr. The camera-based steering system is an interesting feature.
Martin Smits, Sönke Schulz
For more up-to-date farming news click here and subscribe now to profi and save.