Nearly every combi baler maker is now offering a film-on-film binding system which
allows users to quickly swap between net and plastic. Here is our round up of how each make goes about its bale binding business.
It’s nearly 80 years since Allis-Chalmers produced the first round baler, and in that time the tying of the bale has evolved from twine to net and more recently to the use of stretch film. When combined with a wrapper, covering the barrel of the bale in this way means that the same material is used for wrapping and sealing and fewer layers of wrap are required.
With no film and net to tease away from the bale, ease of unwrapping is another benefit – especially in wet or frosty conditions, while there is also just one material to recycle.
Adoption of ‘film on film’ wrapping is also said to increase forage quality. The film applied to the barrel of the bale can be stretched between 15-35% according to the film manufacturers’ recommendations, which is a higher ratio than can be achieved with net wrap which would be a maximum of 8%, Mc Hale points out. “These additional layers of film on the barrel of the bale provide higher quality fodder as the film can be stretched more than net and generates more pressure. This in turn, expels more air, resulting in better feed quality as the tightly bound bale contains less air which enhances the preservation of the crop.”
Other benefits cited by machinery manufacturers include a tighter bale with improved shape and reduced spoilage from the enhanced seal.
Material costs will be higher as not only is the film itself more expensive but less bales can be wrapped per roll than net; however, the advantages are considered to outweigh this.
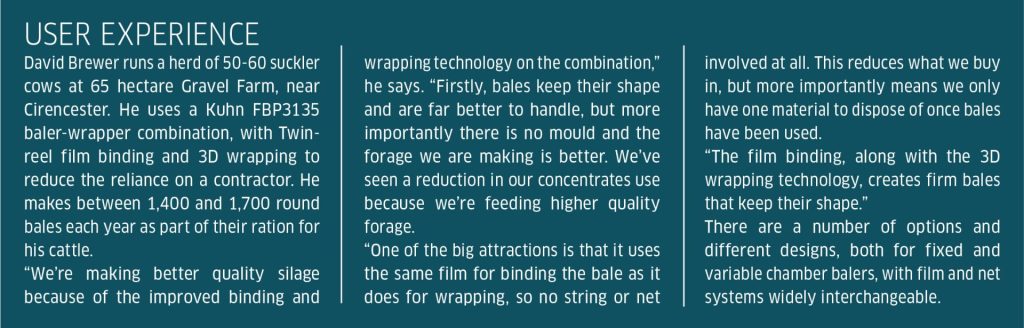
CLAAS
Claas offers the fixed chamber Rollant 630RC Uniwrap with a Net Replacement Film (NRF) system. The 630RC Uniwrap applies either Claas Coatex 1400-2000-17W (1.39m Wide, 17 µm Thick) or 1280-2200-17W (1.28m wide, 17 µm thick). Application is done via the standard net wrapping system.
Machines with the option of NRF are fitted with a roller storage chute that can store spare NRF but can also assist with lifting the roll. NRF machines will have capacity for carrying up to four rolls of NRF along with 12 rolls of wrap for long operating days.
When fitting NRF, the film runs over a transport roller and between two hydraulically controlled bunching rollers before being fed into the bale chamber.
The bunching rollers create a bunch of NRF that can easily be fed into the bale chamber when required. The length of bunched material can be adjusted according to conditions for the start and end of the tying process. The bunched material is fed into the chamber with minimal resistance for a set time depending on settings and when this has elapsed the bunching rollers open and then pre stretching begins.
Pre-stretch can be adjusted from the terminal in 15 increments depending on the film used and the operating conditions. Pre stretching is now carried out by means of a hydraulic braking system designed to give more accurate stretch with more adjustability. NRF can be applied between 2-8 layers in increments of 0.1. Once the bale is nearing tying completion the bunching rollers close and the cutting process commences.
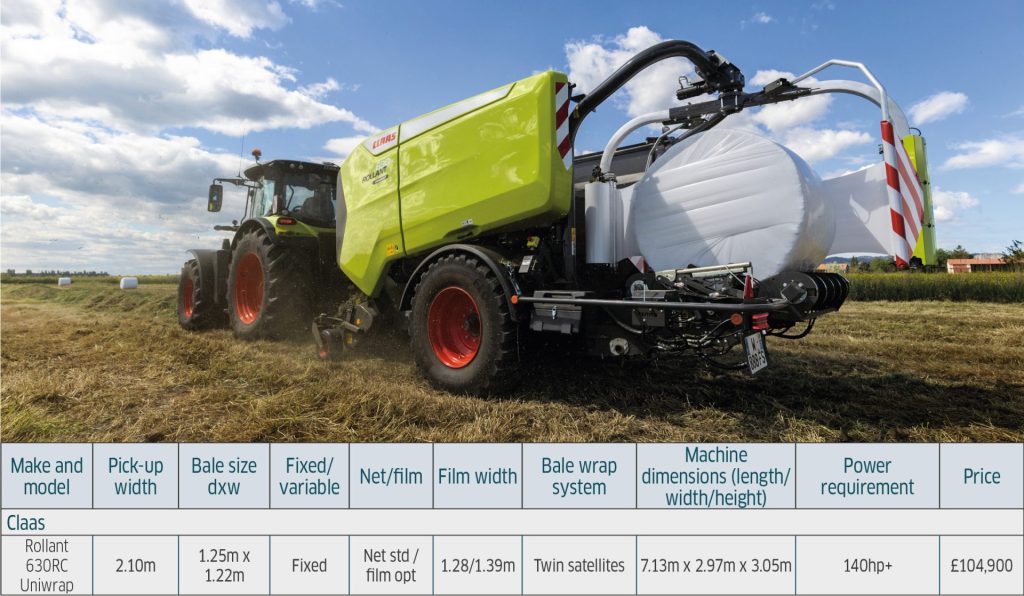
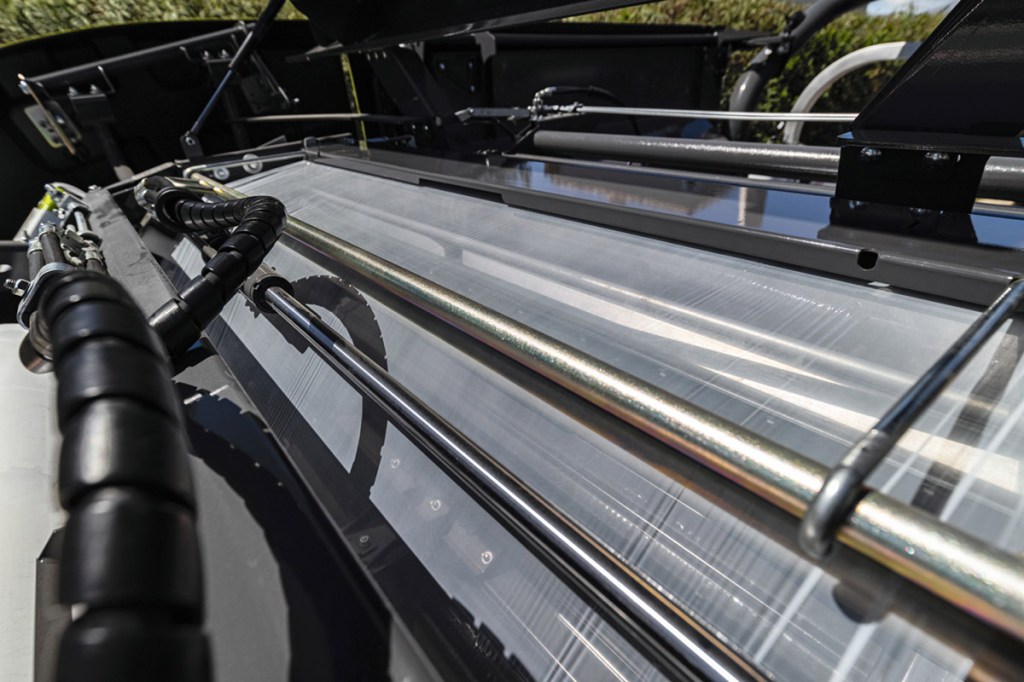
CASE IH
The RB545 Silage Pack offers the ability to pre-wrap bales with plastic film in the bale chamber. If not required, film rolls can be exchanged within minutes for net rolls. Access to the film and net dispenser is easily achieved from the side of the baler at ground level.
Improved crop feeding and a new roller design means more air is squeezed from every layer of material that goes into making up the bale.
When coupled with the new, improved chamber rollers, this means air is excluded immediately from the package, and there’s no risk of bale surface contamination from touching the soil, points out Case IH.
Available as an option, a quarter turn feature allows bales to be deposited on one end, helping to ensure safety on slopes where bales might otherwise roll, and allowing easy pick-up by squeeze-type handlers. An improved system uses a wheel/tyre to gently turn bales on their ends.
Control is via the AFS Performance monitor.
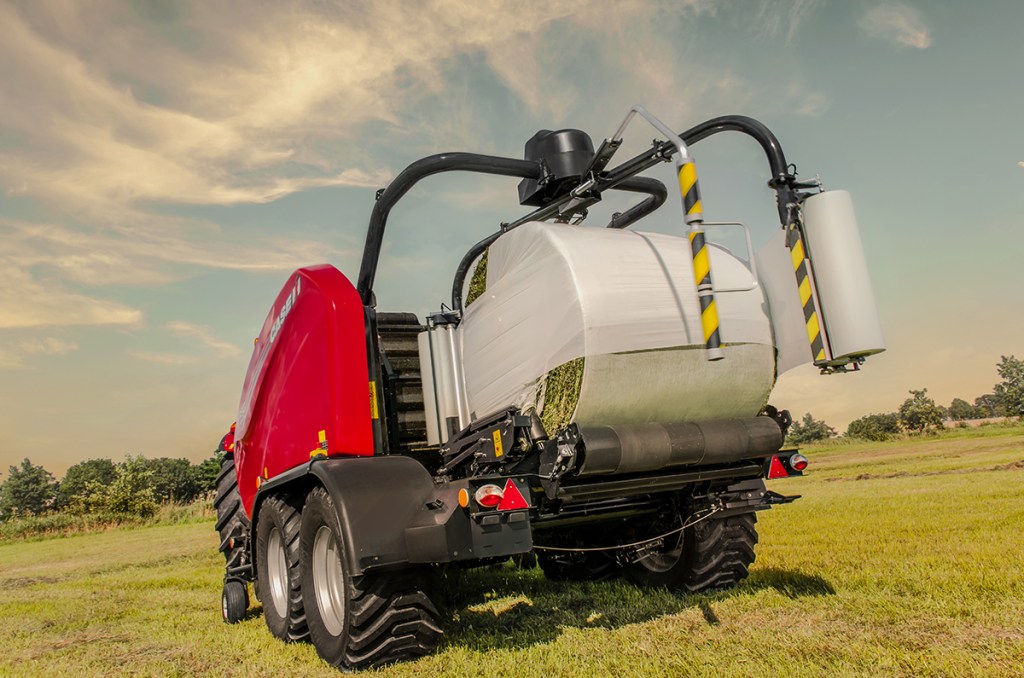

GOWEIL
Göweil’s G1 F-125 fixed chamber combi baler can be specified with a combined net and film binding unit, but also offers the option of a clever dual binding unit. This uses two rolls of net or film simultaneously for quicker binding or can be loaded with one roll of film and one of net. The isobus terminal is used to select the binding unit for net or film, making for a quick swap from silage to hay for example without having to physically change the rolls over.
This model is a high specification combi baler with load sensing hydraulic control, 30 blade chopping unit, enclosed wrapping film unit for 14 rolls and uprated drive system. Isobus control is standard.
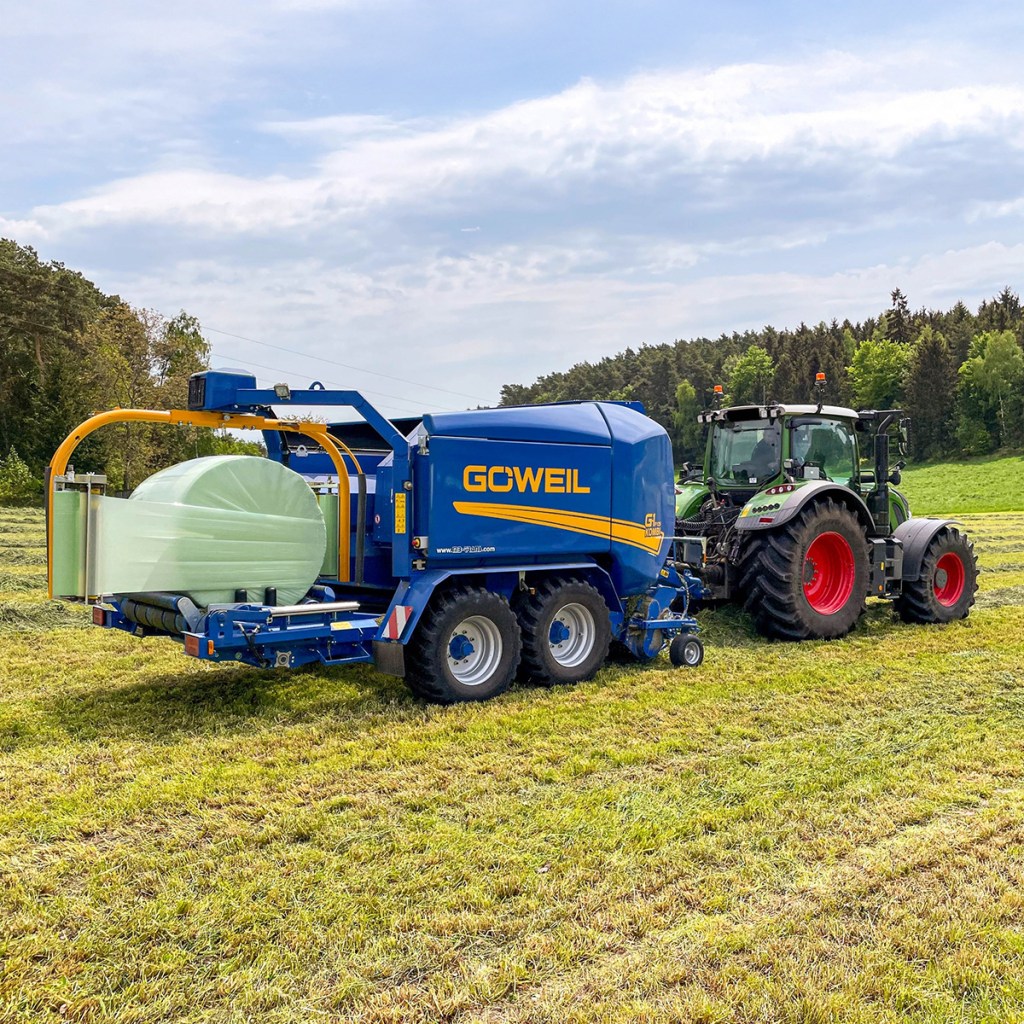
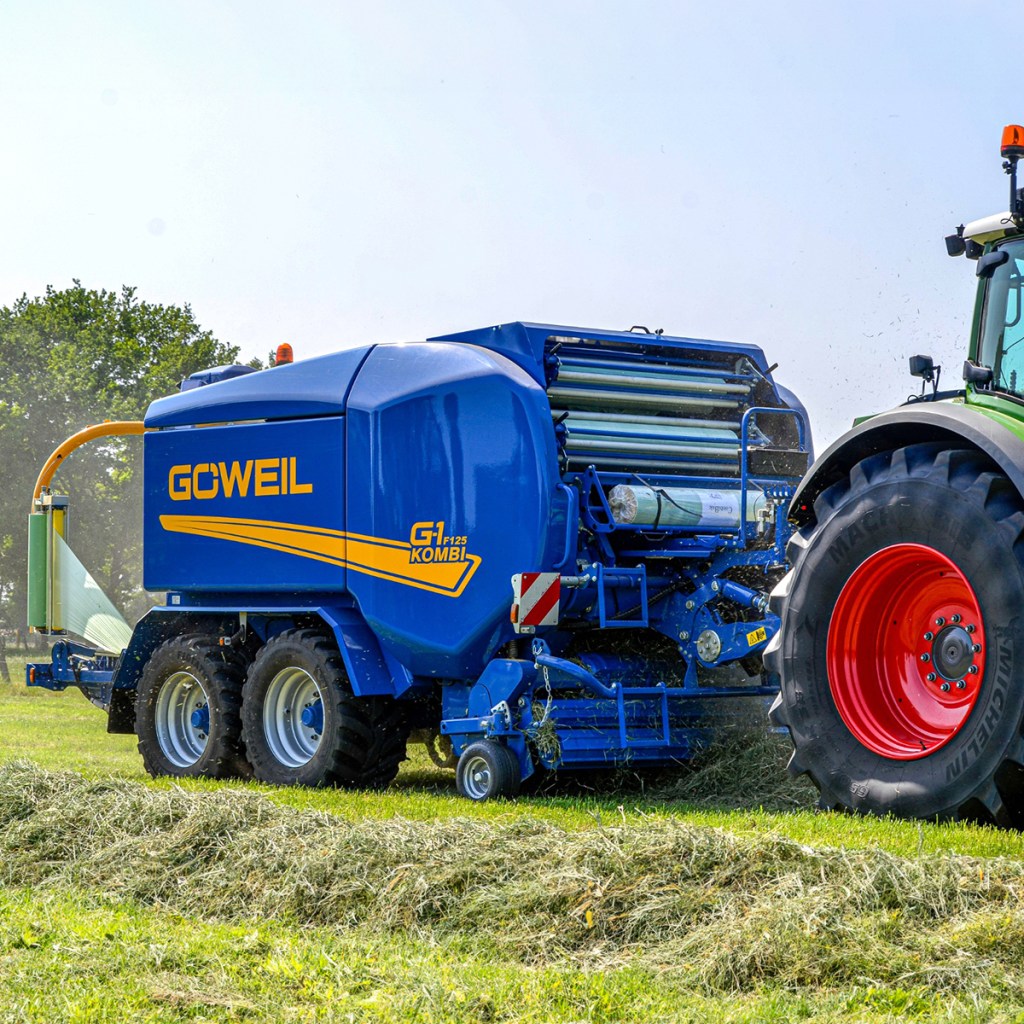
FENDT
Fendt recently added a film binding option on its Rotana 160V Combi variable chamber baler-wrapper combination, alongside the Rotana 130F Combi fixed chamber version. In addition, there is now a quick-change system for film and net rolls as well as a new tailgate function.
Two gathering arms and a shaft binding system specially developed for the variable presses guide the binding material precisely and safely into the baler chamber. An electro-magnetic brake controls the pre-stretching of the net or film optimally according to the binder and its roll diameter. This optimises the stretch effect of the film and its adhesiveness, thus maintaining the density and quality of the bale.
The film binding system specially developed for variable chamber balers can save up to 3.0m of film per bale, as the shaft binding allows the film to be inserted wider and thus requires much less bundling, says Fendt.
A quick-change system for film and net rolls is available for the Rotana Combi balers. The roll magazine offers three storage spaces for rolls that are loaded ergonomically. Machines with the Eco Load System have a simple loading chute for manual loading.
With Comfort Load, the driver places the roll in a padded carriage, lifts it and guides it up to the quick-change system, allowing the machine to be loaded directly from the ground. An intelligent lever system makes it possible to switch between the three ready-to-tie rollers in a few simple steps. In addition, the easy operation and padded contact surfaces prevent damage to the net or film.
Other updates to the Fendt Rotana include optimising the tailgate closing process, said to offer outputs of up 30 more bales per day.
An automated dry mass control system fitted to variable chamber Rotana round balers allows the operator to select how much dry matter a bale should contain before the baling process. Two synchronously operating sensors in the bale chamber record the moisture and mass of the bales and from this, the software calculates the dry matter content during the baling process. The round baler controls the bale diameter according to the entered target dry matter, offering greater control of rations.
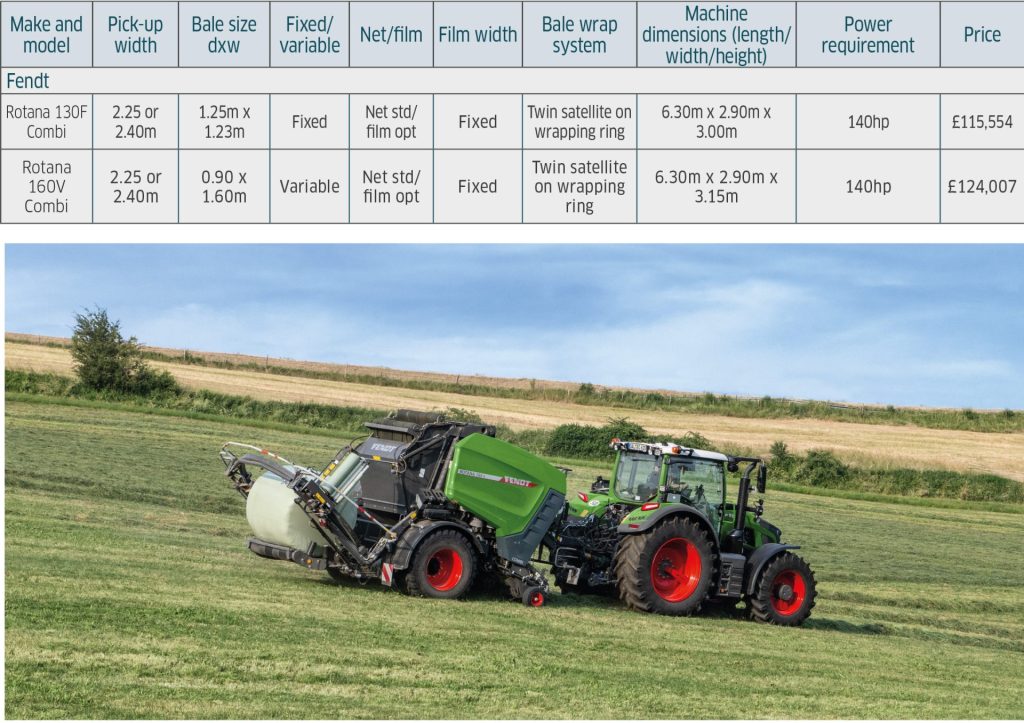
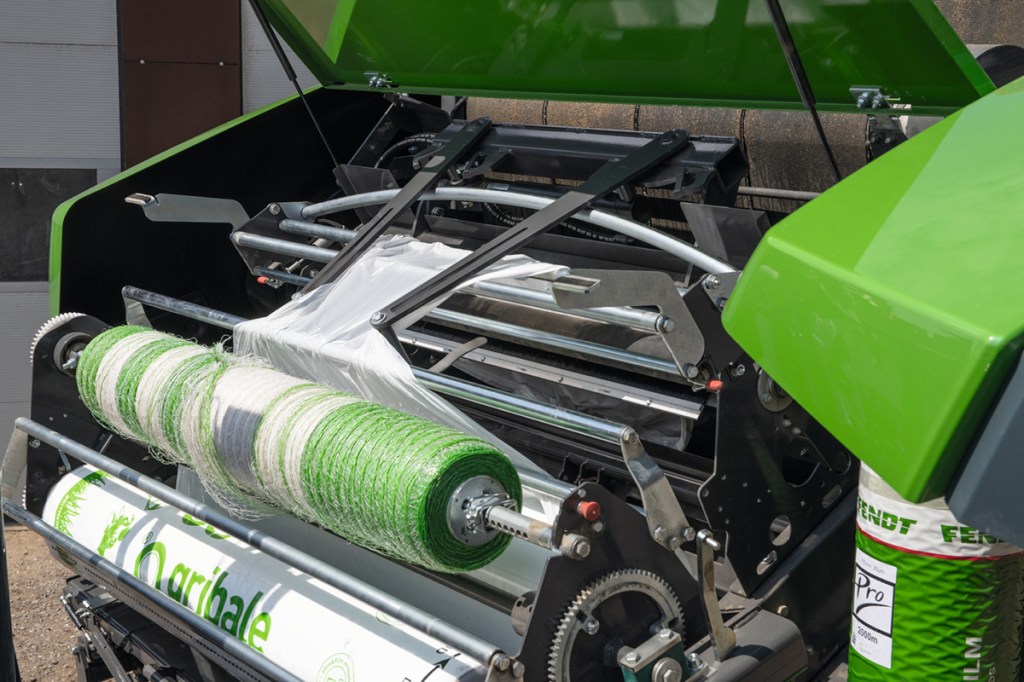
KUHN
Kuhn has four round baler combination wrapper models that offer Twin-Reel film binding to maximise forage quality and ensure preservation at the time of baling.
The smallest version is the I-Bio+, suited to remote farms and fields for users requiring wrapping immediately after baling. It features the same 18 Powertrack rollers as the larger FBP3135 for consistent bale density. Above these two models are the variable chamber belt balers – the VBP3200 and VBP7100 series.
On the I-Bio+ the baling and wrapping processes are completed without the need to transfer bales, so the machine’s overall dimensions are similar to a standard round baler. The upper part of the chamber raises to allow the six rollers in the bottom half of the chamber to act as the wrapping table for the two integrated pre-stretchers to rotate on a ring around the bale. It takes 18 seconds to wrap the bale with six layers of film.
The pre-stretcher pivots over the wrapping ring to allow operators to change rolls easily.
The optional Twin-Reel film binding system is available on all models and uses the same size film rolls as the wrapping system, instead of a wider mantle film as is common on other machines. By using two 750mm stretch film rolls, a higher pre-stretch is possible and can reduce binding costs by 37%, says Kuhn. This system also reduces plastic usage by up to 30% through the pre-stretching prior to application and extends film change intervals. Each roll weighs just 27kg, compared to the wider rolls, which can weigh between 40-90kg.
For VBP and FBP models, Kuhn’s 3D wrapping applies more film to the shoulders of the bale to protect the most vulnerable areas. As the film is distributed efficiently across the entire bale surface, this helps bales maintain shape during long periods of storage as more air is excluded thanks to the cylindrical wrap.
Kuhn’s Intelliwrap feature allows operators to adjust the number of wrap layers on individual bales depending on the humidity of crop and desired storage time. This can be any number of layers, including odd numbers, and ensures operators only use the film required for each bale. It is available on all models.
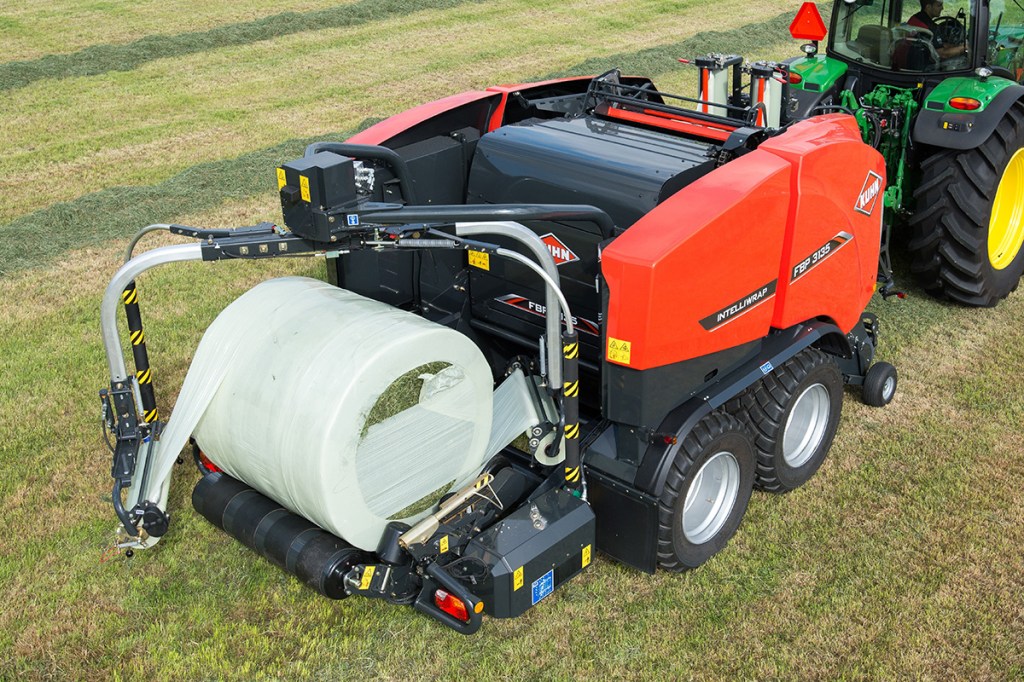
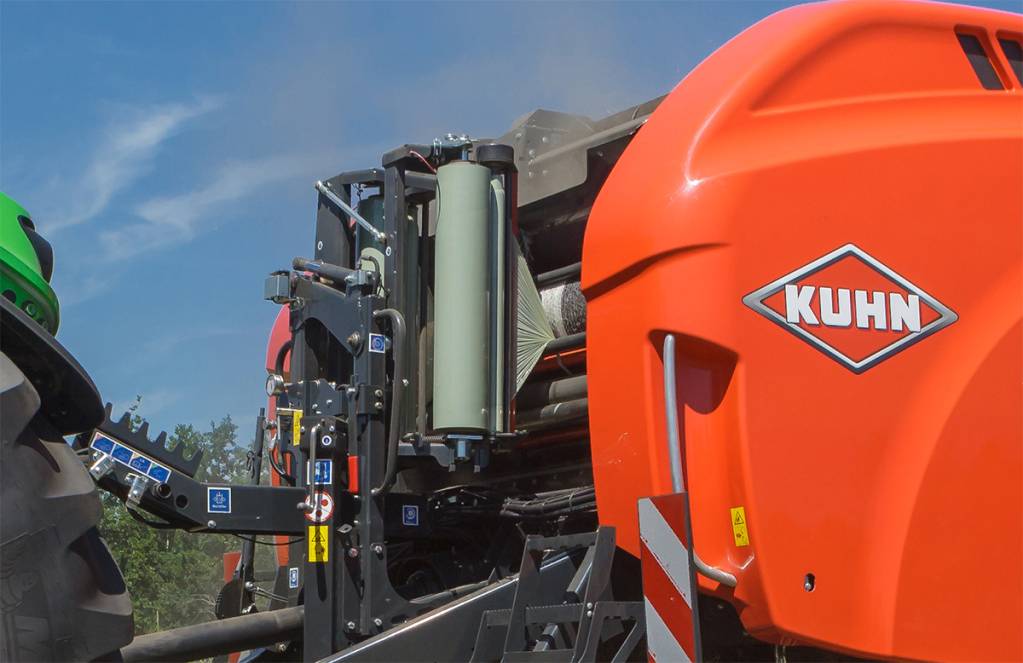

KRONE
Krone offers a compromise between fixed and variable chamber balers in the form of the Comprima CF 155 XC Plus ‘semi-variable’ chamber baler which can adjust bale sizes from 1.25 to 1.50m in diameter, using heavy-duty rubber fabric belts reinforced with steel slats to compress the material.
Also available with film wrapping capability is the Comprima V 150 XC Plus, which allows operators to produce bales ranging from 1m to 1.50m in diameter. The machine’s bale chamber design is built on three core components: the tensioning arm, suspension strut, and tensioning kinematics. As the top tensioning arm moves downward, additional space is created within the chamber, allowing for increased material intake. Another feature includes the ability to adjust the density of the bale from 80cm depending on what you are baling in order to get the most from each bale.
Net wrap is standard on both models with film wrap an option. The shared net/film wrap unit is at the front of the baler and 1.28m wide film wrap is loaded onto a swivelling locating shaft and the moved towards the tying unit. The storage compartment above the shaft stores up to two spare rolls of wrapping material.
The integrated bale wrapper is a twin arm design and uses a specially designed lever—activated only when the gauge roller detects a sufficiently heavy bale— to transfer the bale onto the wrapping table.
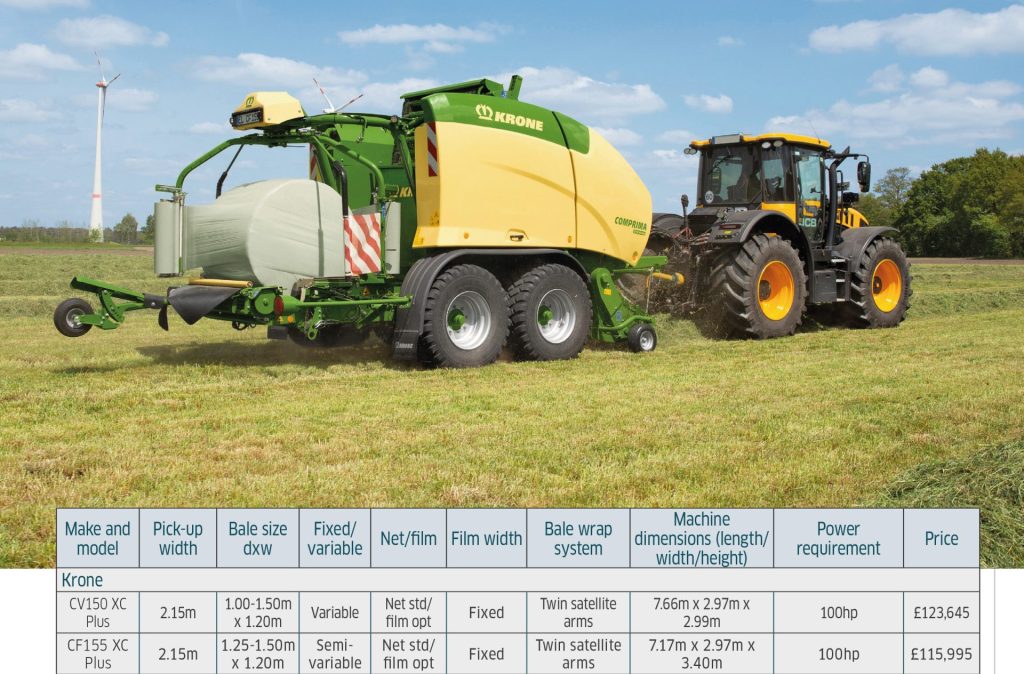
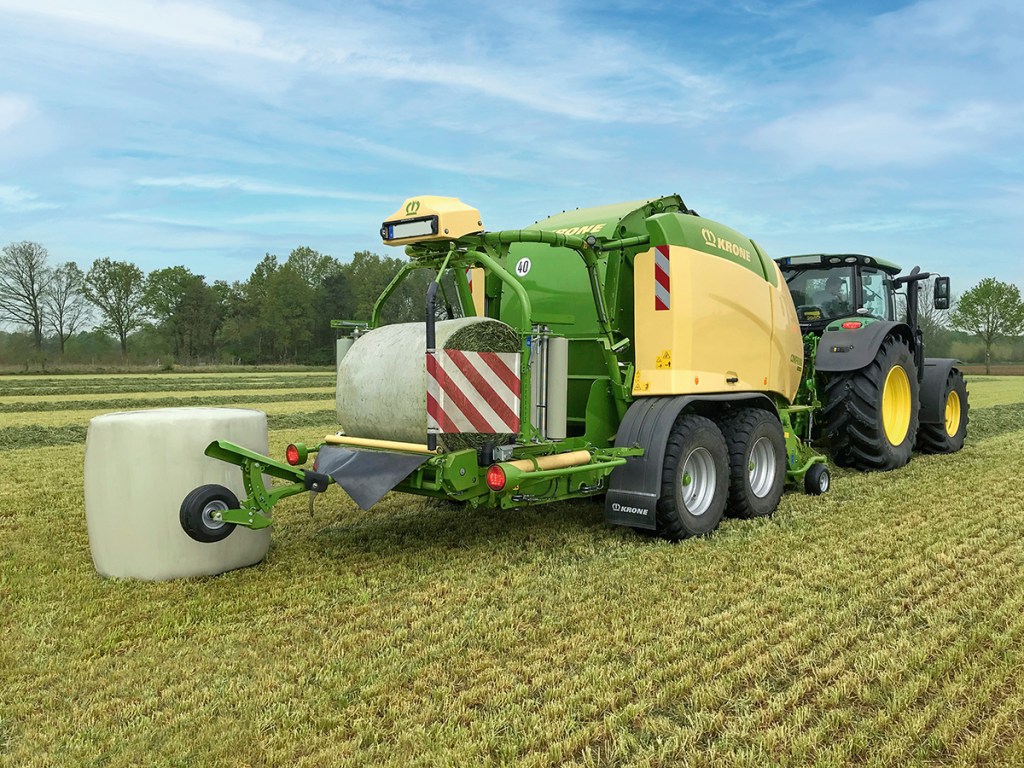
JOHN DEERE
The C461R premium wrapping baler incorporates a heavy-duty drive system rated at up to 210hp with 1,000rpm pto.
The 18-roller bale chamber has a 121cm width, and a transport table system allows one bale to be held while the next bale is being formed before ejecting both at the same time.
Operators can choose from two-metre or optional 2.2m pick-ups, feeding a high capacity MaxiCut HC rotor with 13 or 25 knives. The baler also incorporates a full width parallel drop-floor system operated from the tractor cab, which enables blockages to be removed instantly. The machine is available with a single axle as standard or with an optional tandem axle chassis for improved stability.
The film binding system, available as a factory option or retrofitted, uses ultrasonic sensors, camera and a roll clutch, for increased reliability to reduce downtime. The film wrapping module uses many of the net wrap components, said to make swaps between the two straightforward.
John Deere offers its own XtraCover 1.38m wide fully recyclable film for use with the system; two film rolls are stored as standard with an extra as an option.
Monitoring is via John Deere’s Gen 5 display as standard.
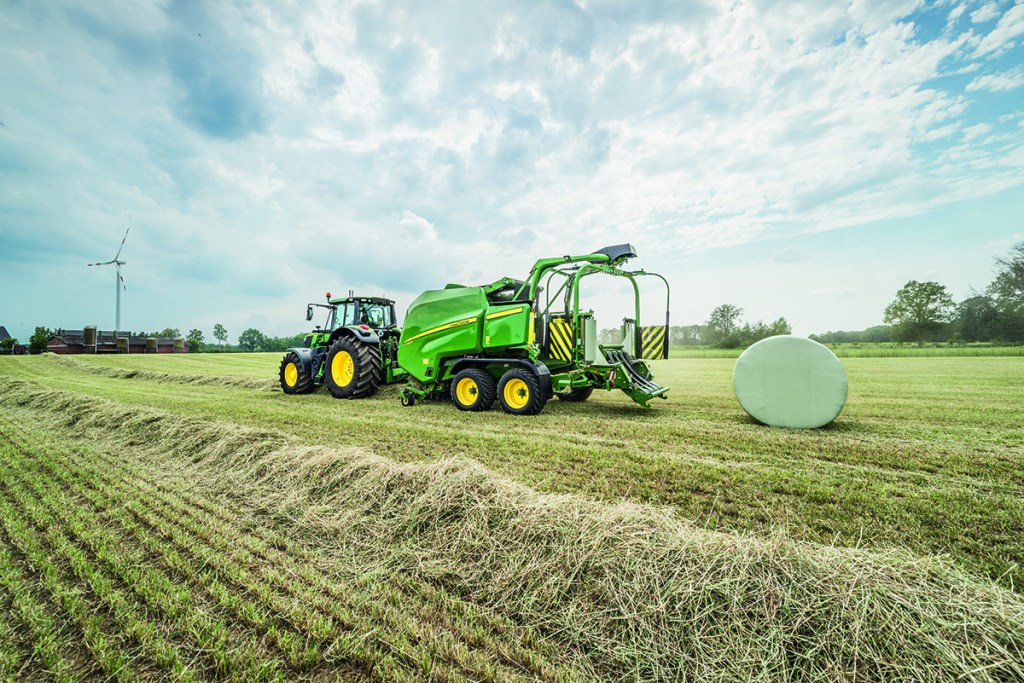

VICON
Taking the non-stop round baling and wrapping process a stage further, Vicon has introduced Premium specification for its fixed chamber, non-stop baler-wrapper combination, the FastBale.
FastBale uses a pre-chamber which produces two-thirds of the bale. As it reaches its preset density, crop then flows into the main bale chamber, along with the pre-formed bale, where it can be taken to its maximum size of 1.25m. When the bale has been made, the crop flow switches back to the pre-chamber, allowing baling to continue while the completed bale is automatically wrapped.
Film-on-film binding is available as an option, Vicon pointing out that the continuous baling process of FastBale saves time when using net replacement film as it can continue baling while the ‘tail’ is being formed at the beginning and end of the cycle and during the additional wraps needed compared to net.
Switching from net to film requires no mechanical adjustment – the tolls are simply swapped over and the appropriate stretch ratio selected on the control terminal. Two spare rolls can be carried on the baler.
The FastBale is also available from Kubota dealers as the FB1000.
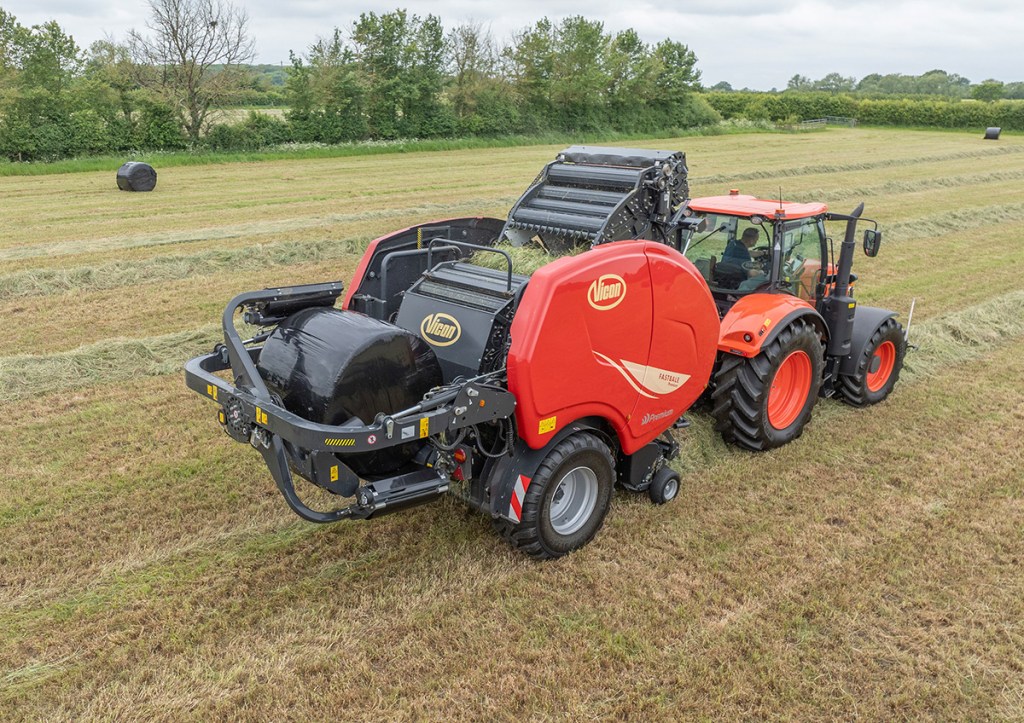
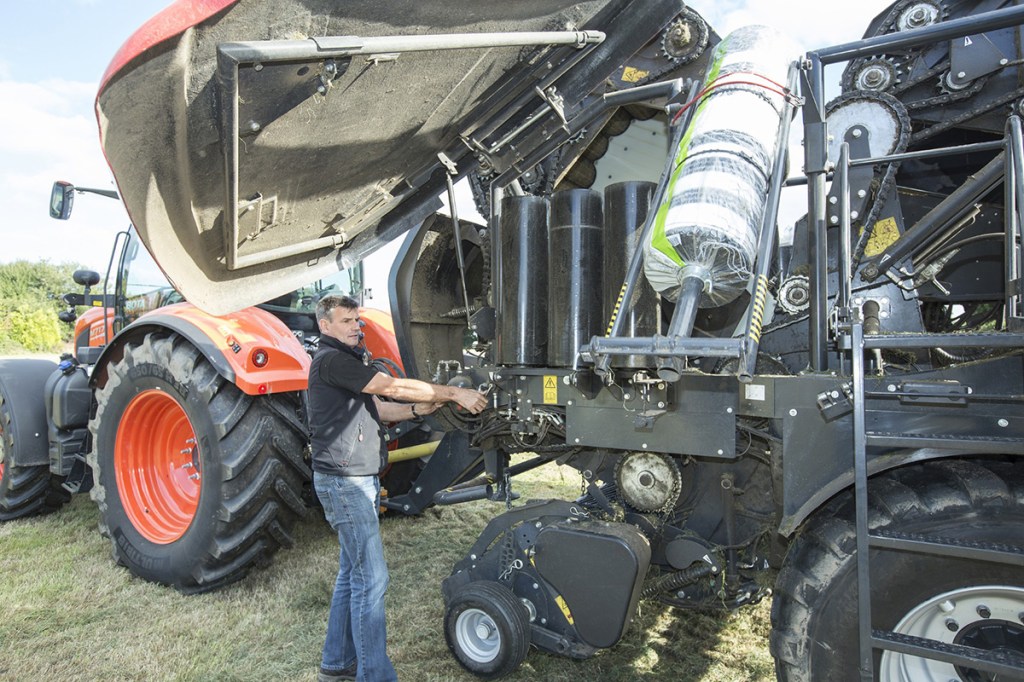

MCHALE
Film wrapping in the chamber was first introduced on the McHale Fusion 3 Plus integrated baler wrapper in 2013 before progressing on to the latest model the Fusion 4 Plus. In more recent years, McHale launched the new Fusion Vario Plus, a variable chamber baler wrapper which is now capable of applying film or net to the barrel of the bale in the chamber.
The Fusion 4 Plus is a fixed chamber baler which produces a 1.23m x 1.25m bale and can apply NRF or net to the barrel of the bale in the chamber using the Infinite Stretch hydraulic binding system. This patented application system adjusts the braking force on the roll of plastic in-line with working conditions. This allows for a continuously variable stretch, which can automatically adjust to changes in conditions, without the operator having to adjust any settings.
The variable chamber Fusion Vario Plus produces different size bales depending on the crop type. The width of the bale chamber is 1.23m and uses a heavy-duty, three-ply single belt the machine to bind a high-density bale using film or net.
This baler is fitted with a new binding unit called the Direct Beak Binding system which maintains a permanent grip on the net or film. It features a ‘beak’ which pivots upwards and away from the chamber to prevent any issues with crop accumulation during the baling process.
During the binding process, it pivots downwards to actively place the net/film inside the chamber before it spreads full width for uniform coverage across the bale for consistent and accurate binding.
On both designs, net or film tension can be adjusted depending on the operator’s requirements through the console. To obtain the desired stretch, a large net/film brake has been fitted to both machines, which provides 25% more stretch. This is especially effective when operating in cold weather with film that requires a higher stretch percentage, says the company.
Both Fusions feature the new Profi-Flo pick-up which has been designed to increase crop intake through more efficient crop flow.
The integrated baler wrappers use a patented transfer system. When the bale is bound in the bale chamber, the bale chamber splits horizontally. As the top section of the bale chamber moves up, the lower section of the bale chamber simultaneously moves up and out, transferring the bale onto the wrapping platform. This process has been increased in speed in order to match the throughput of the Profi-Flo pick-up.
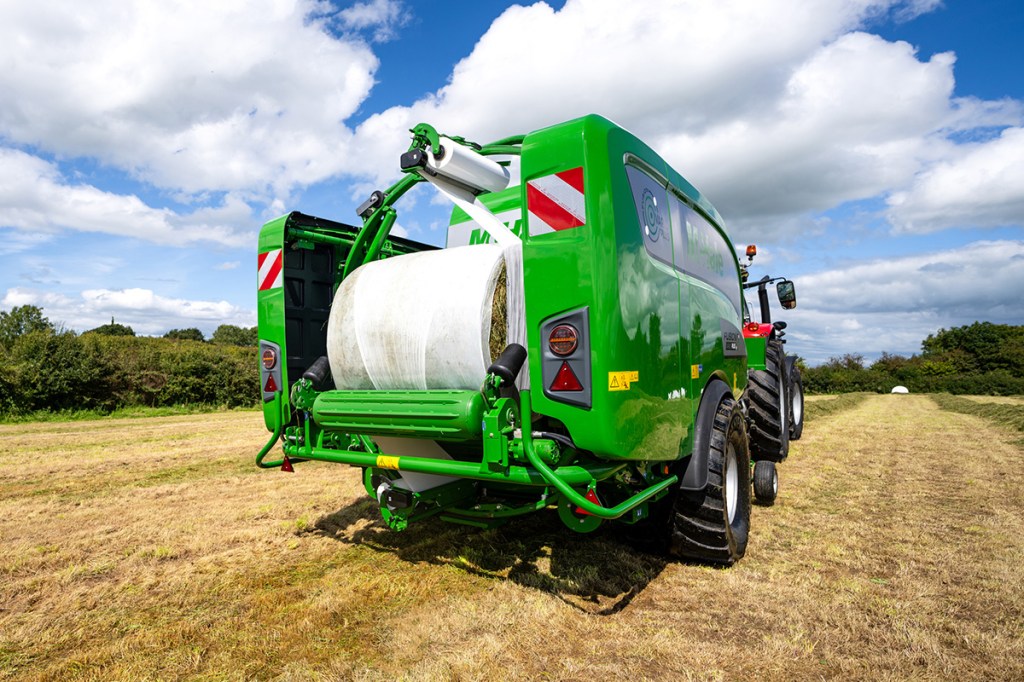
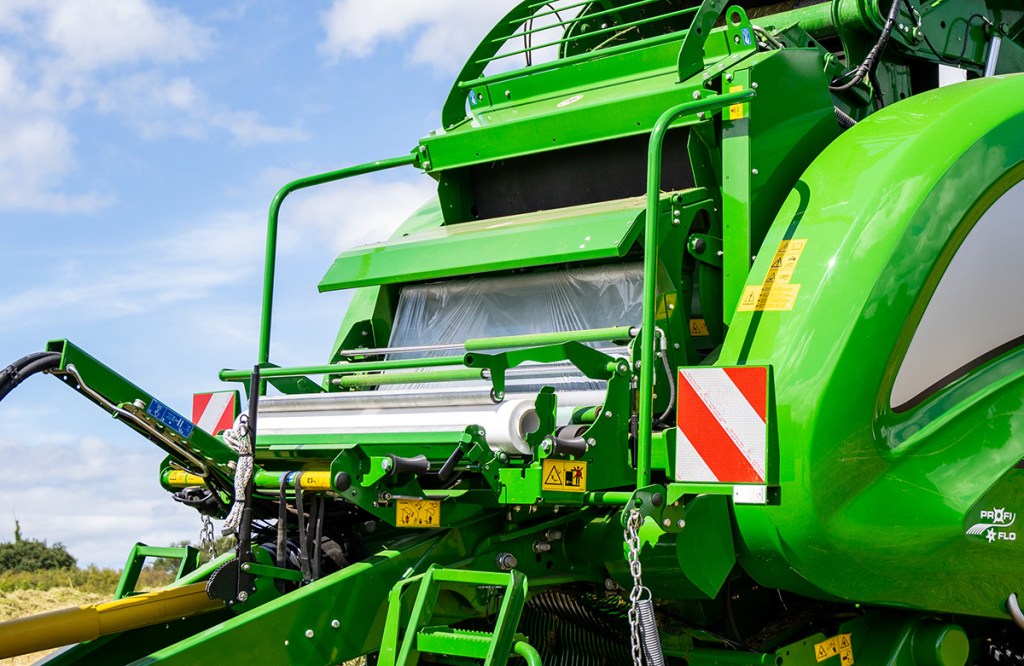
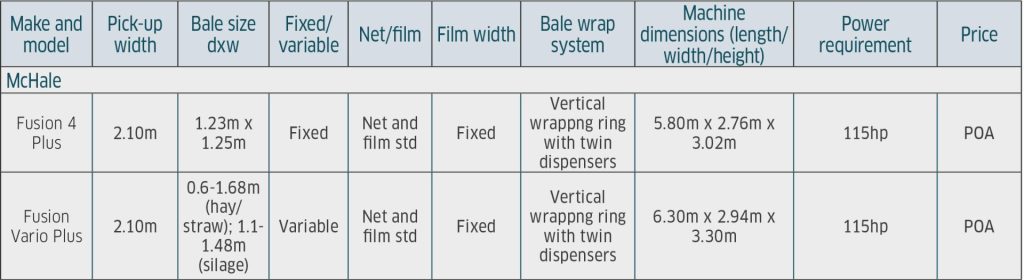
NEW HOLLAND
The Roll Baler 125 combi from New Holland has the option to wrap with net or film. Each cold-formed roller in the bale chamber features heavy duty sleeve bearings and automatic lubrication for maximum durability and is produced from 3.5mm thick steel with a seam-free surface to protect net wrap or film.
A design said to be unique to CNH, the latest film wrap on Combi models has positive hydraulic feed. This can be set to pre-stretch the film and combines with the bundle arm system for a tight, secure and reliable film wrapping process.
Accessed via fold-up steps, a front platform makes replacing rolls of net or plastic film easier.
Gap closure plates prevent plastic wrap catching in the chamber rollers, a hinged knife preventing any film catching the feed rotor. Operators can switch to net wrap if required, with Roll Baler Combi models now able to accommodate 1,400mm rolls for increased versatility.
This model uses the in-line wrap system of predecessor models including the possibility for the operator to choose between 500mm or 750mm film.
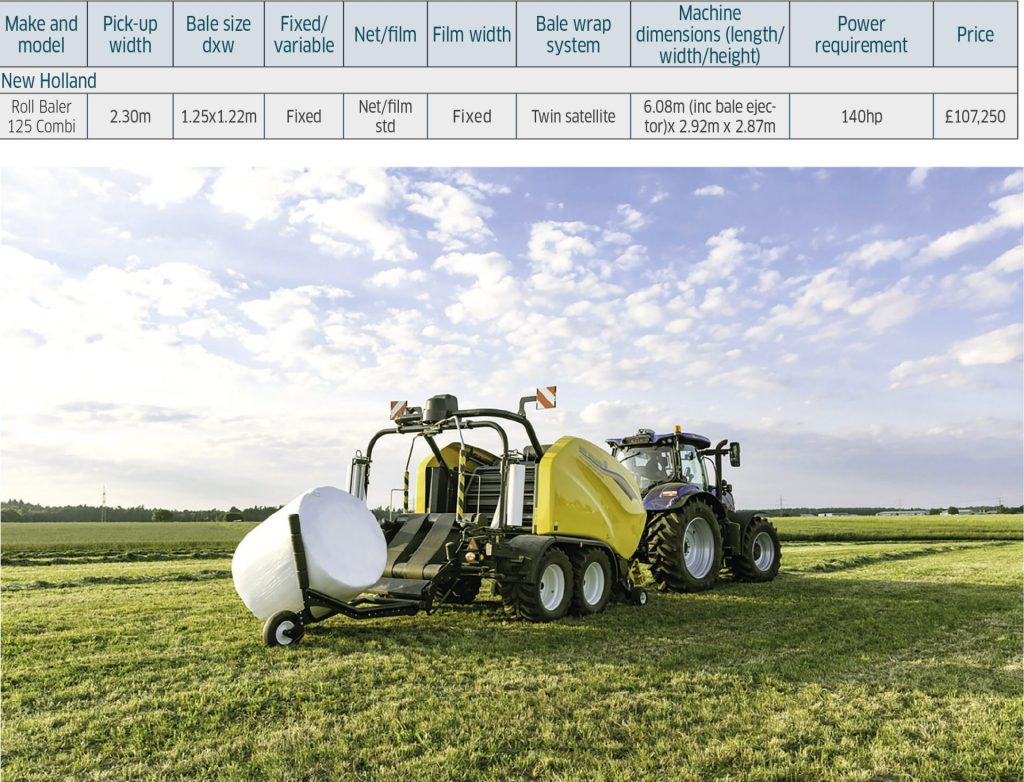
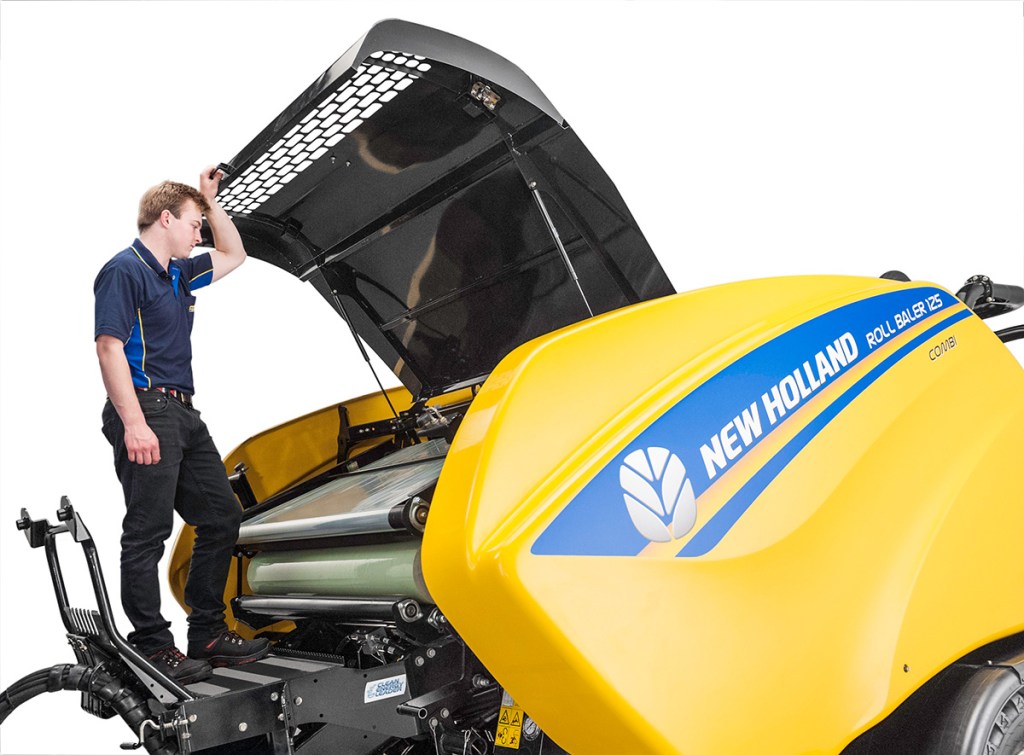
Jane Carley
For more up-to-date farming news click here and subscribe now to profi and save.