TECHNICAL: Wheel motors are becoming more popular, especially on larger trailers and tankers … or on more specialist machines such as potato harvesters, where they can lend a helping hand in wet conditions or on hillsides. This is how they work.
With more axles and bigger loads, a powered axle could provide some extra traction when in the field. Driven axles are not a new concept; indeed, they have been in use since engineers started looking at ways of boosting traction together with four-wheel drive using a ground speed pto or other means to match the speed of the tractor. Even when you look at today’s new generation of electric-powered axles you need a suitable power source. Nevertheless, it is obvious that driven axles are a useful thing to have on trailers or trailed kit such as heavy slurry tankers, trailers or
harvesters where a lot of the weight rests on the axles. The tractor needn’t be as big if the axle that carries the main load of the trailer is driven.
One manufacturer of such axle drive systems is Black Bruin, which says that a drive axle can produce about 30-50% of the traction that would otherwise be supplied by the tractor. The reason for this is the bulldozing effect. If the wheels of the trailer sink into the soil, a bow wave forms in front of the tyre that it has to constantly overcome; otherwise it will stall … and, well, you will no doubt know the outcome. Overcoming this bow wave is akin to effectively climbing a hill; consequently, the smaller the ‘bow wave’, the easier the load is to pull.
Large wheels, a low tyre pressure and a large contact patch help minimise this effect. If you add driven wheels, then this too will help the wheel run more on the ‘wave’ rather than behind it, thereby reducing the draft load on the tractor. Other advantages of wheel drives are, for example, the fact that the combination is stretched when reversing or controlled braking on slopes; hence there’s improved slope stability. It can also help to extend the harvest window for the likes of root crops in a wet autumn.
Hydraulic solution saves space
Although expensive, hydraulic wheel drives are becoming much easier to fit into existing designs. Which is one of the main reasons why several tanker makers were displaying such systems at Agritechnica. Axle suppliers such as BPW even have axles with integral drives and brakes.
This is where the Finnish hydraulics specialist Black Bruin comes to the stage. It started installing wheel motors that were driven by radial pumps on logging trailers, and today it has further expanded into the agricultural market, which has a growing demand for such traction boosting systems.
Together with the hydraulic control specialist Niehues, they can now offer complete set-ups that transmit up to 120kW to the axle drives. The drive unit is controlled through ISObus or the axles have extra sensors that sense and transmit the speed and sense of rotation to control the output of the oil motors. It’s all clever stuff.
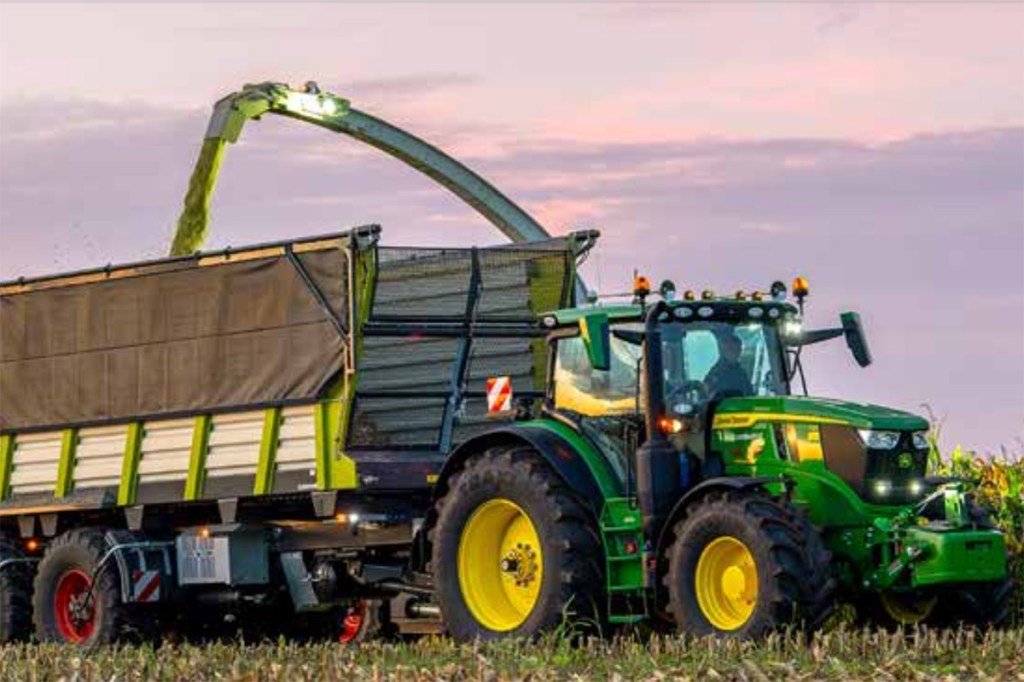
Radial motors
At the heart of the wheel drives are hydraulic radial motors with a rotating housing and hub. The motor is rotated as oil is supplied through a distributor valve. This feeds the oil to the pistons, which, in turn, press rollers against a cam ring. The cam ring is shaped like a wave. As the roller, which is fixed in its position, presses into the flexible and wavy ring, a torque or rotary movement is generated. As the piston is extended to maximum length, the power stroke ends. Like in an engine, the rotary motion opens a valve and allows the oil to escape, or the roller follows the ring profile and pushes the oil from the piston back into the system before a new work cycle begins.
Not from stationary wheels
Several pistons combine to generate the output that is needed. An important detail here is that the wheel should already be turning to ensure that maximum torque is developed and disproportionate forces are avoided. This means, on a stationary wheel, the motor develops only about 80% of the power it can develop on an already moving wheel.
Theoretically, oil would continue flowing into the motor when no drive power is required. This, however, would have a negative effect on the idling behaviour of the trailer, increase wear and run the oil hot. Therefore, Black Bruin also markets a mechanical freewheel set-up that opens a valve to depressurise the system. Here, mechanical springs fix the pistons and rollers in their retracted positions. This allows the wavy cam ring to rotate freely – even at speeds of up to 60km/hr or more. In the best case, drive axles have their own onboard hydraulic system on the trailer — which applies more to harvesters, forwarders and slurry tankers. The advantage of a closed system is the oil is only used for this specific purpose; it doesn’t mix with the tractor’s oil and the system has sufficient cooling capacity to prevent the oil from overheating.
In an open system, where the oil is supplied by the load-sensing system of the tractor, for example, there is a risk of insufficient oil cooling. The wheel motors are also designed for high outputs in the pressure range from 350-450 bar. Tractors usually can’t keep up with this demand, especially as radial motors can swallow more litres than the tractor can provide. In addition, high-pressure and return filters are required on the trailer or tractor to prevent dirt ingress — a system killer — into the drive system.
Logically, however, the drive must not be switched on or off at pace, so speed sensors and the control unit monitor the system. For maximum torque even at higher speeds, some systems are equipped with an additional gear reduction. Even larger diameter tyres such as those on slurry tankers can be driven with such systems.
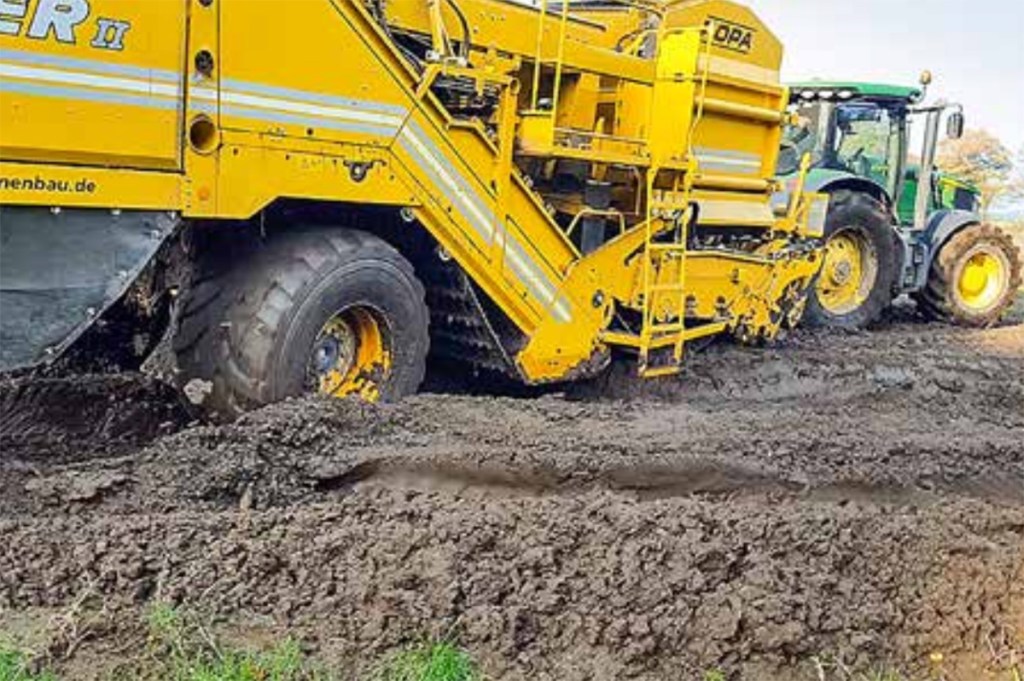
Potato harvesters, in particular, benefit from some extra propulsion in a wet autumn harvest.
Summary
Four-wheel drive power has been standard on tractors for the past couple of decades to minimise wheel slip for maximum traction. In fact, two-wheel drive is now almost an oddity on most farms.
Depending on the system, up to 120kW can be transmitted hydraulically to the wheels of the trailer. This, however, requires a powerful hydraulic system — ideally a closed system. Despite their benefits, wheel motors are not widely used, as they are expensive to buy and keep. And a drive axle isn’t necessarily a substitute for a heavy tractor, either, because only a heavy tractor can provide the stability it takes for hauling a heavy trailer or tanker on public roads.
For more up-to-date farming news click here and subscribe now to profi and save.