A Beckett recently changed their spraying set up to the latest tech, and it has revolutionised their crop protection system, and improved application efficiency and efficacy to boot.
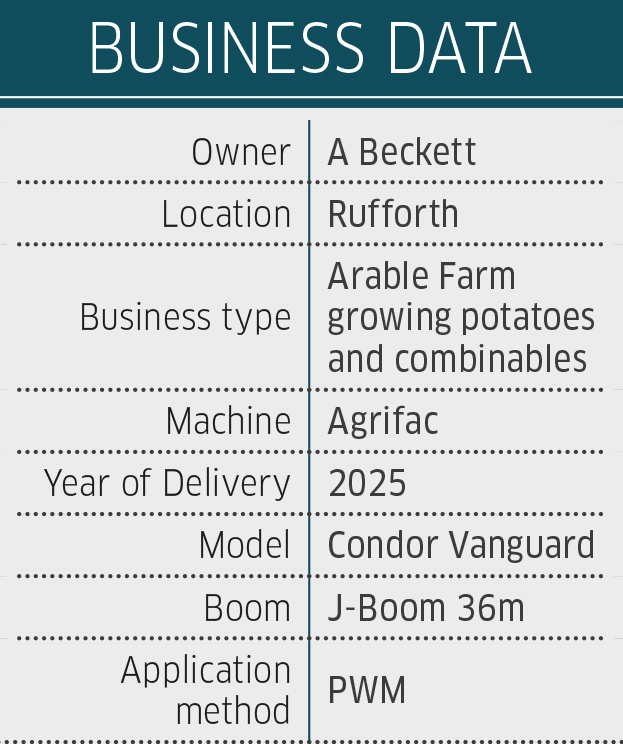
Based near Rufforth outside York, A Beckett grow 320 hectares of potatoes, and 400 hectares of combinable crops, Since Tony Beckett established the enterprise in the 1960’s he took care of spraying, as the hectares grew, his son Steve; now the head of the business took on some of the workload with a second sprayer.
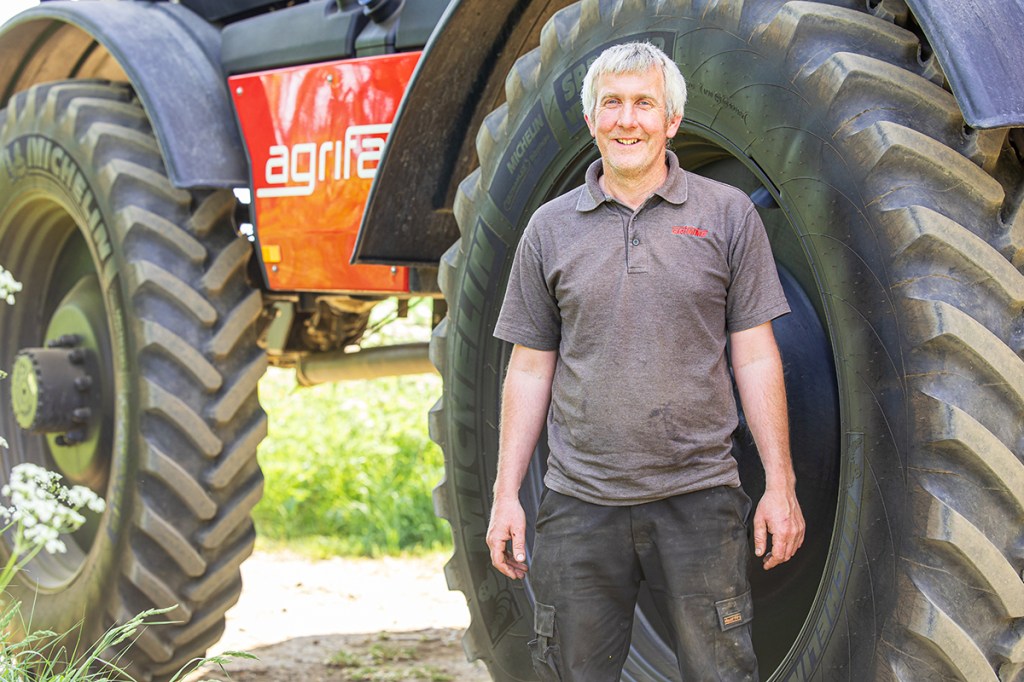
In the last twelve months Tony has stepped back for frontline operations, including the spraying work. This left quite the gap in crop protection capacity, which prompted Steve to look at what he could change to alleviate some of the bottleneck.
The enterprise has been running Agrifac sprayers for some time, indeed, the farm’s last three machines have come from the Dutch firm, and with the field performance where the business wanted and good backup there seemed no reason why not to have another. However, the local dealer had ceased trading, which might have thrown a spanner in the works, were it not for B W E Engineering extending their service south from Kelso in Scotland, as it happens they rent a building from Steve. From here, Callum Banks runs the Agrifac franchise which has filled the in Yorkshire and the rest of the North of England.
So, with dealer support bolstered, Steve ordered the Vanguard and took delivery in spring this year. The machine was a pre-series, number two off the line, while number three working in the east of England, and has been for about 18 months.
A gift horse
The Vanguard has a larger tank than the previous machine, up by a thousand litres to 6,000l. Which helps with output, working now as a one-man spraying outfit returning to base for re-fills, Steve can get more done with each load. This was originally used by Agrifac at factory for testing any issues from the field under controlled conditions, and as such it’s got quite a busy boom. It’s equipped with HightechAirPlus, StrictSprayPlus, StrictHeightPlus, and FastFoldPlus which is a lot of Plus’.
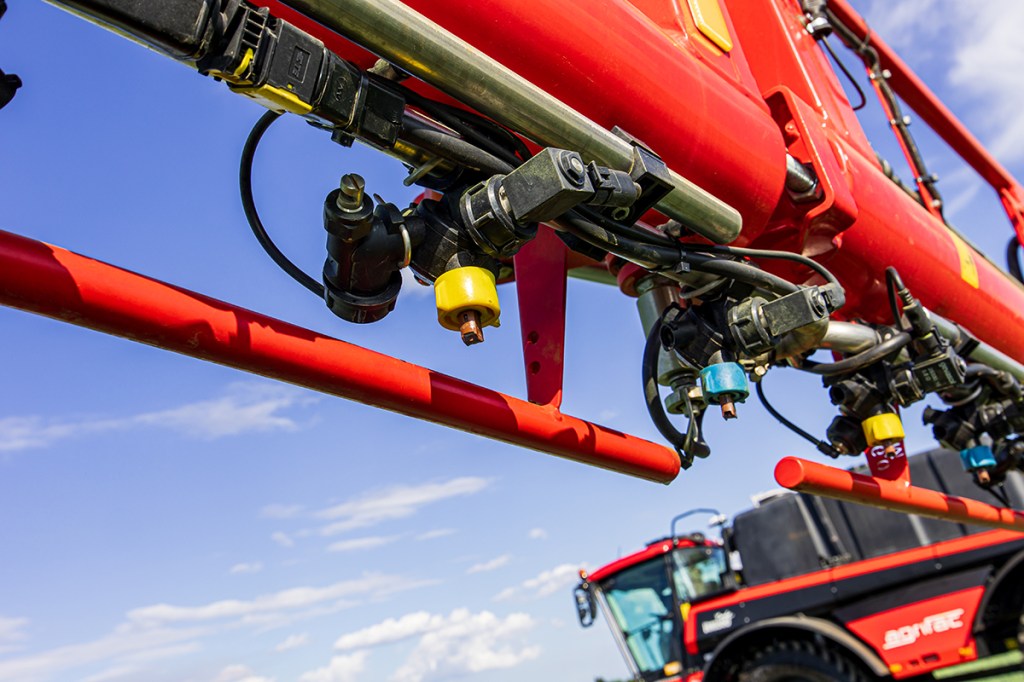
The nozzles are on 25cm spacings, which was the one thing that Steve Beckett categorically wanted following a conversation with a neighbour who is one of those people that will look at every detail of a machine before ordering. His words of wisdom were that without doubt the closer spacing returned better application.
The machine is equipped with HighTechAirPlus, which is the air induction body that mixes compressed air with the water to give a wide adjustability in droplet coarseness. These are spaced at 50cm, Steve obviously sensed our impending question and his reply; “I haven’t used it yet, I wanted to learn the StrictSprayPlus system first.”
StrictSprayPlus
Agrifac has its own in-house pulse width modulation system. In brief PWM is like diesel common rail injection, the lines hold pressure and a solenoid at each nozzle opens and closes allowing varying quantities of product through the nozzle. Because PWM pulses, the nozzles need to be larger than a constant flow system, Steve routinely uses an 04 nozzle.
What sets the Agrifac system apart is the frequency of the pulses, many run at 50hz, whereas the Vanguard runs at 100hz, this said to greatly increases the versatility of the system and what can be delivered with one nozzle.
Like charging our phone there is an ‘ideal’ range to operate, not too slow, and not to 100%, the Agrifac system functions best up to 80%. And because of the higher frequency, the working range with an 04 nozzle does pretty much every application Steve needs.
PWM brings individual nozzle control even with a 25cm spacing resulting in 144 sections and allows the booms to run at 25cm above the crop rather than 50cm which has seen the window of opportunity to spray widen significantly. “We get more spray days now, a marginal day with 50cm spacing is a day when you can get on just as well with 25cm and have less worry about drift,” points out Steve.
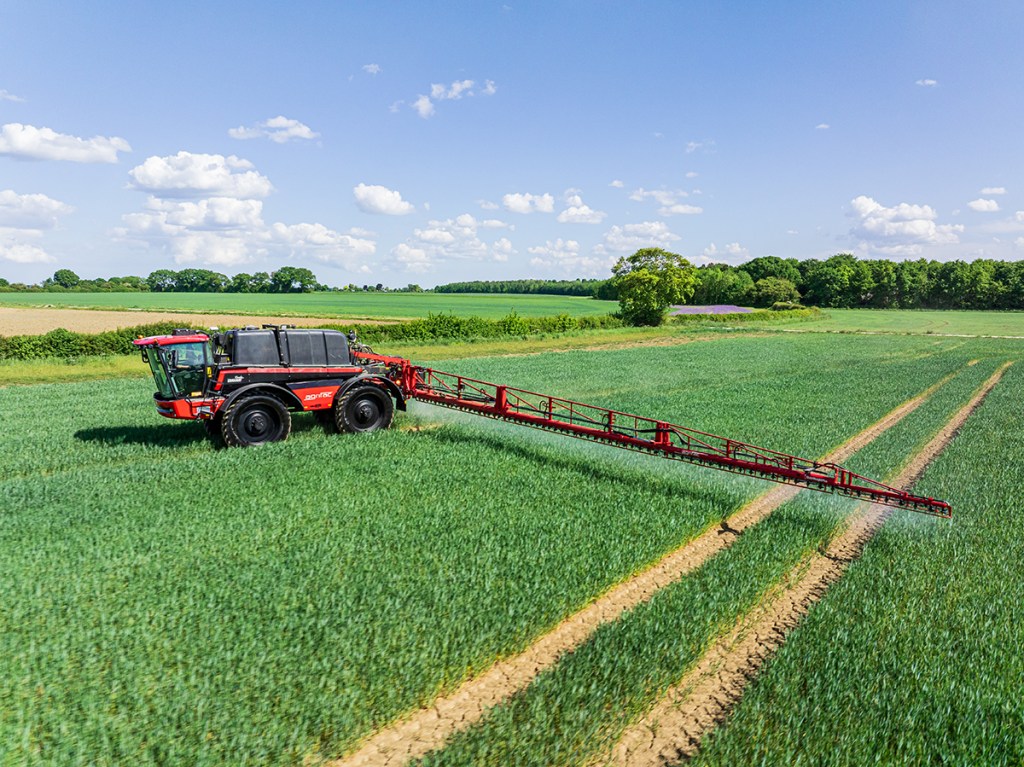
The PWM system also increases the working capacity on challenging days, and in sensitive places. “You can drop the pressure down to 2.0bar, and spray headlands which gets you 36m away from gardens, there’s minuscule drift that way,” he adds.
There has been a cost saving through accuracy. Adding to the PWM praise, the system also incorporates curve control and where the Beckett’s farm, some days there can be fields of four or five hectares with lots of curved boundaries and short runs so achieving an even application reduces scorching, in turn keeping weed infestations down.
“It’s really impressive, you can see the difference in what’s coming out of the booms in curves, the crops are much more even,” says the farmer.
Spraying cereals and potatoes also utilises the small sections, naturally in cereals the machine is working at 36m consistently in tramlines that are drilled into the crop. But in potatoes the working width is closer to 35m, which can be more precisely catered for.
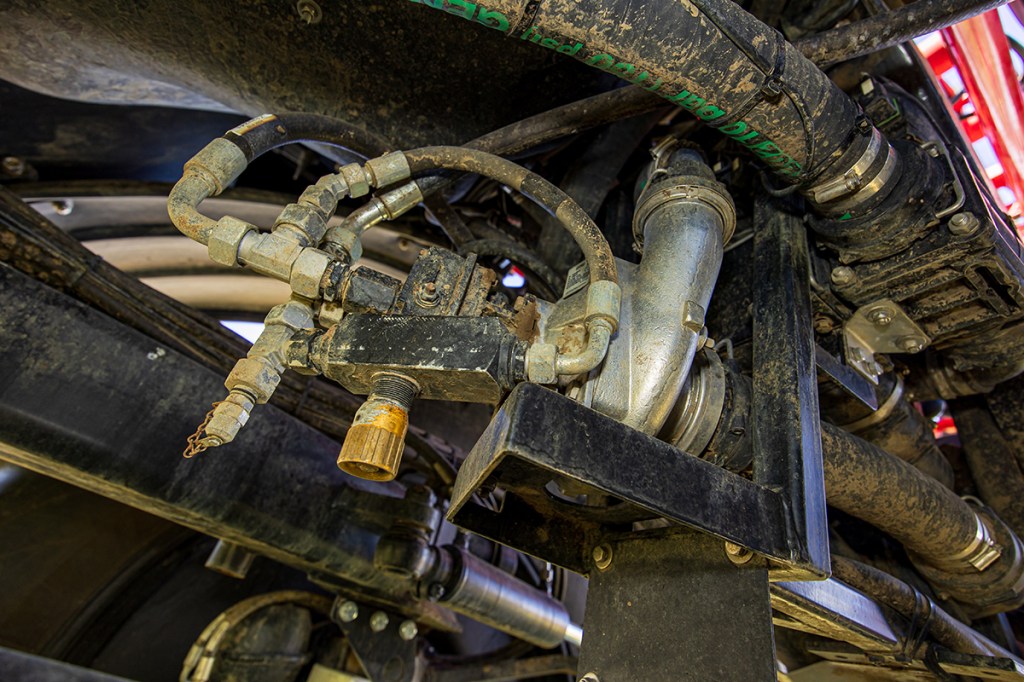
Another feature on this high spec machine is PurifyPlus, a pretty thorough automated cleaning system with several cycles, from a quick boom and nozzle wash, to a full boom and tank clean. Whether doing a nozzle clean or a full system clean out, there is the choice of spray out the washings or drain them. A useful feature if you have been spraying a particularly nasty product, that you don’t want to over apply, or just want to be sure you’ve cleaned the sprayer down. “It’s really good, you just select the cleaning option and press start, it does it all for you, a nozzle clean only takes a couple of minutes, points out Steve.
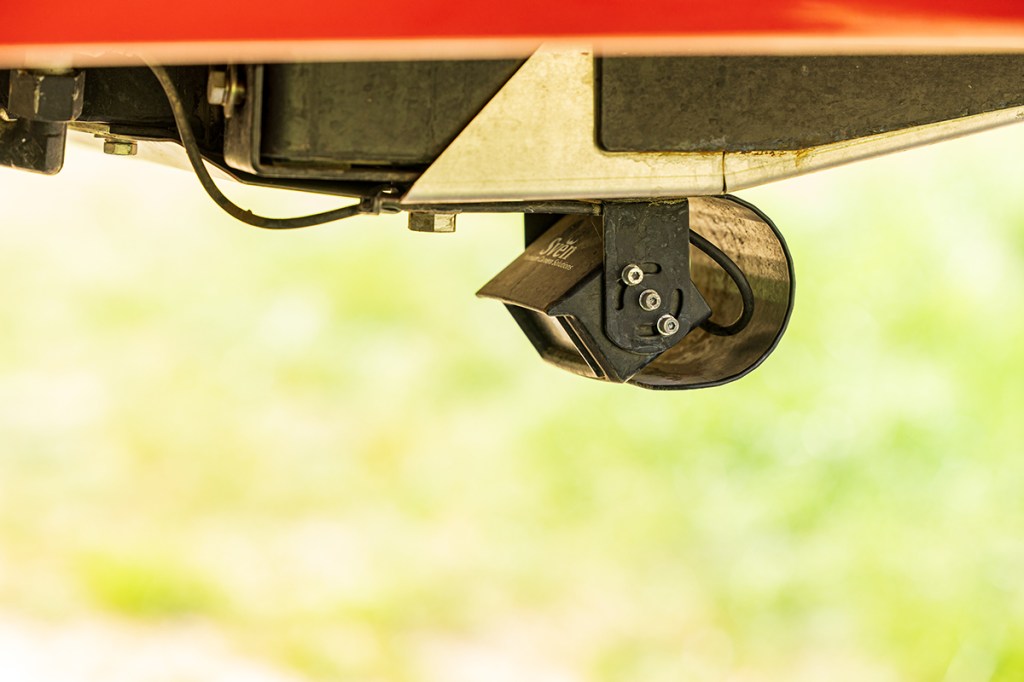

The nozzle body
Obviously, the system is not free, it’s a £20,000 extra, but in the grand scheme of things £20k more for a sprayer that retails for over £300,000 isn’t a huge step for what the system brings. It has moving parts, so there is a higher running cost too. But it can be turned off and used like a standard sprayer, so for jobs where you don’t need additional precision, like burning off or pre-emergence. The machine retains individual nozzle control if the operator chooses not to use the PWM system, retaining accurate shut off but loosing turn compensation.
Agrifac say that it costs about £25 for the parts to service a nozzle body, that ’s new piston, seat, and O-rings as well as the piston sleeve. But the maker stresses that these valves have thousands of hours service life depending on the type of work, and don’t require any special tools to strip them.
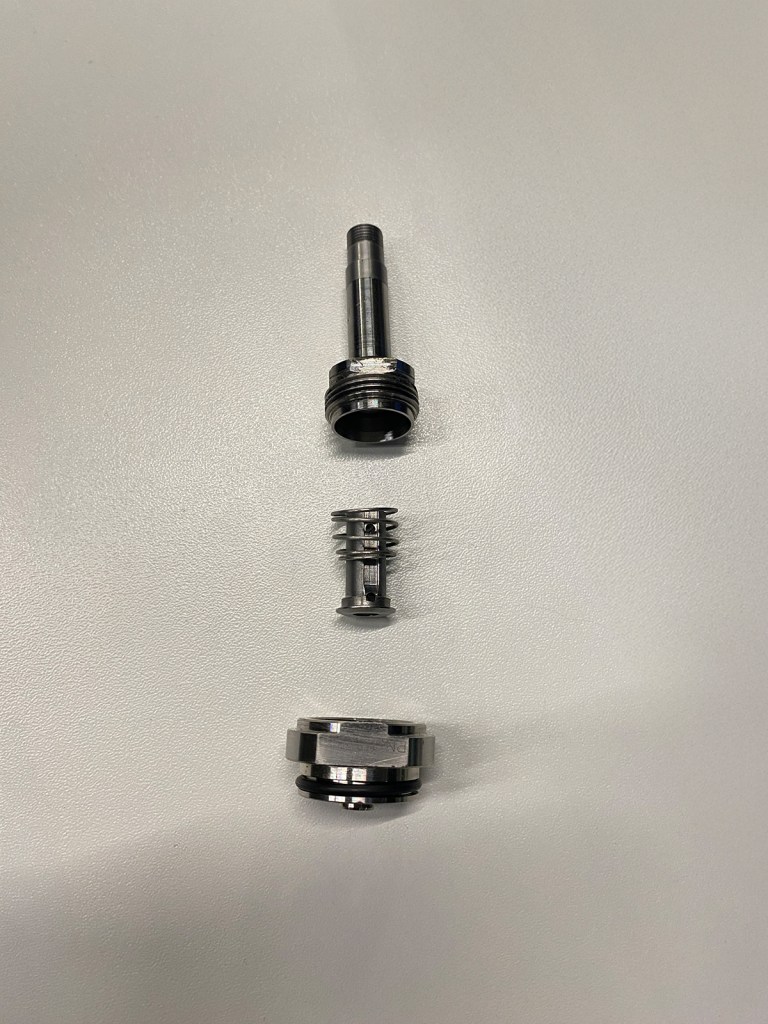
The latest system on this machine has seen a change to the CANBus, previously the valves were in strings of 12, they’re now in strings of four which keeps the signal speed up, and also makes diagnostics easier, as faults can be tracked down to smaller sections of the machine.
A feature many will like, is the fact the modules that control the four nozzle strings can be changed by the user, if there is a fault, traced to a module, the operator can tell the machine they’ve replaced it, input a code, and get back to work without dealer intervention.
Running at 54 volts instead of 24 was necessary for the 100hz system, so there are transformers on the machine to step up from the standard operating voltage of the sprayer. If a valve does decide not to work, there will be an error code but the machine can continue to spray, and with 25cm spacings, it will still give a workable application.
Along with the benefits of section and curve control, Steve has noticed the switching on is more accurate. “On previous machines you could watch the pressure build tens of metres into your bout before it was where it should be, the Vanguard is on quickly with negligible delay as soon as you’re over the boundary.”
Booms
The J-Booms are a fairly substantial structure, but the faster folding function sees the booms unfold in just under twenty seconds, a ‘I wouldn’t not have it now I’ve tried it’ feature for Steve, speeding up workflow when working in smaller fields.
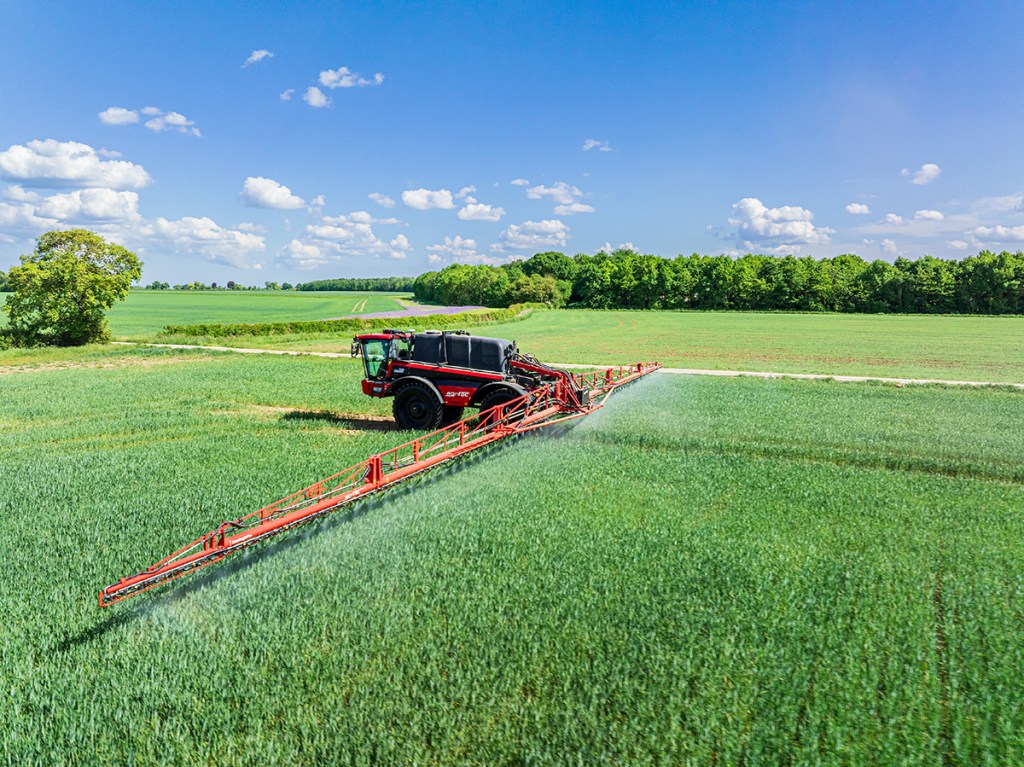
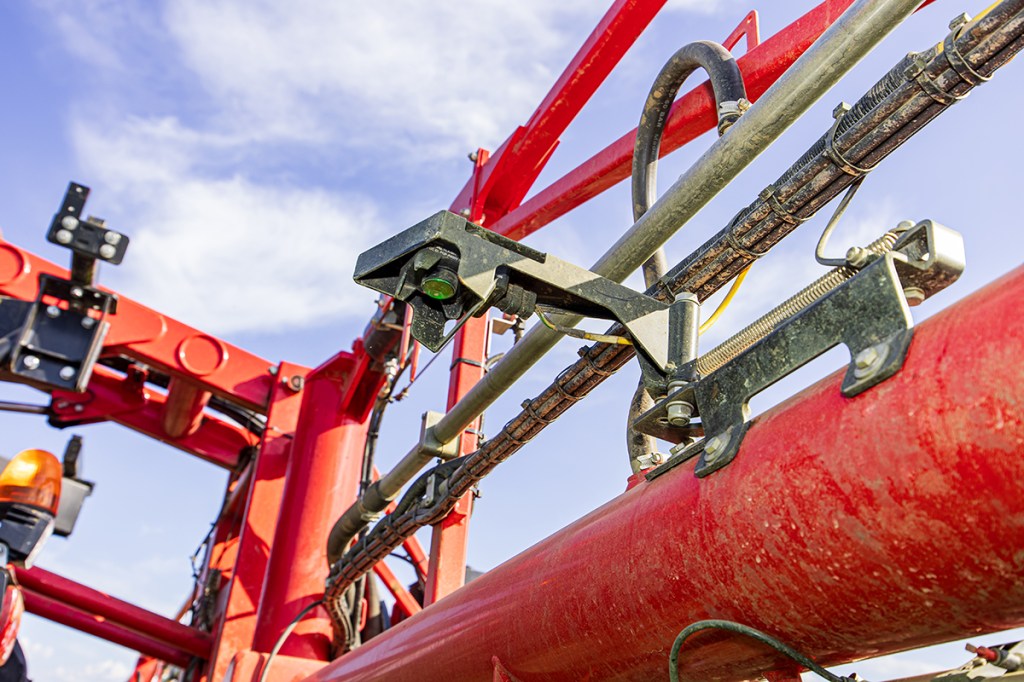
StrictHeightPlus is a necessity when using 25cm spacings because the boom needs to be lower and naturally needs greater sensitivity and response. The system is also new to Steve coming from the older acoustic system he’s been really impressed with the new technology. The key here are the radar sensors, they read the ground not the crop so are much more consistent at keeping the boom following the ground. The J-Boom only flexes at the tower point, so there are two radar units per side. “It’s night and day better than the older system, that would be tripped up by varying crops all the time.”
Chassis
The Vanguard is a narrower longer version of the Condor, initially intended for the French market, so they could get larger tank capacity without going wider. But fundamentally the Chassis design was lifted from the Condor and stretched to achieve this.
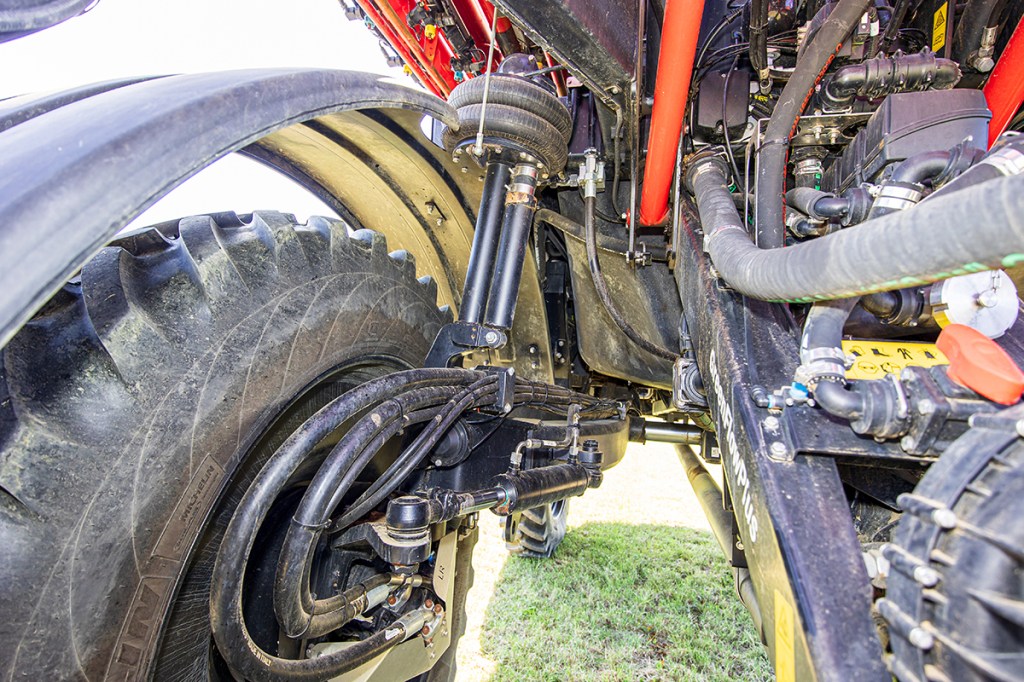
With a 1.80-2.60m variable track width, the machine can move on the road with maximum stability, and within a few metres tuck into 1.80m. The width adjustment happens at the centre of the machine chassis where the longitudinal beams pivot, so there is only one sliding component reducing the potential of wear.
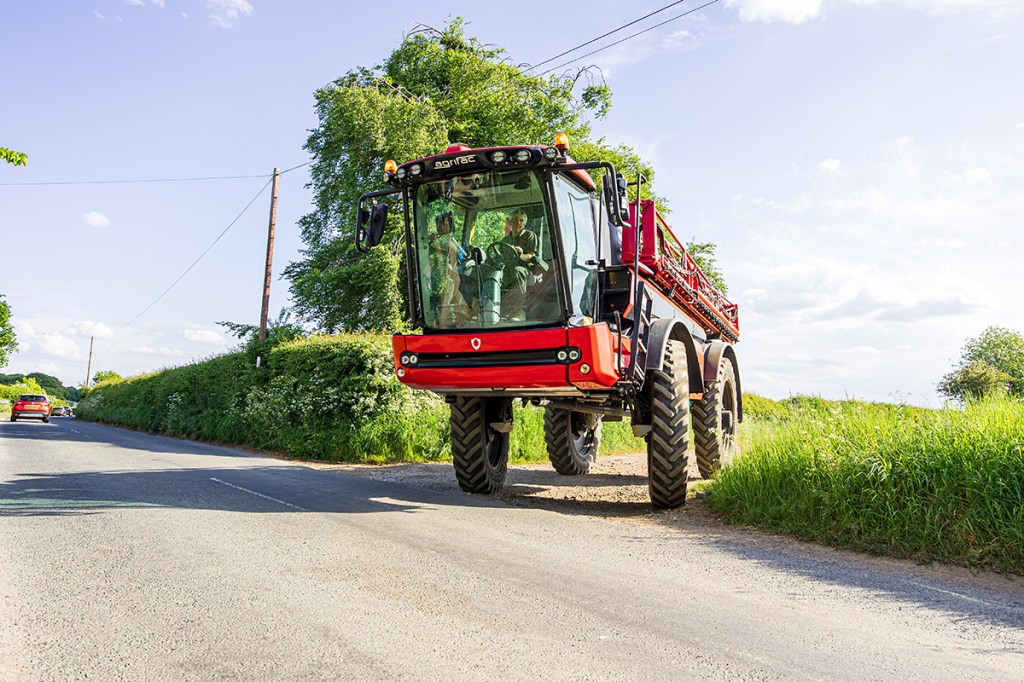
Steve points out the ASR traction control was also a marked improvement over his previous machines. “On the first model we had, it was just turned off, it was pretty much useless, but this machine it works quite well.”
The wheel motors just turn the wheel, they don’t carry the weight of the machine, that is done through the hub and a “proper” wheel bearing. With a 6,000l tank and a hefty boom the Vanguard weighs in at nearly twenty tonnes with a load of chemical, add another tonne for fertiliser.
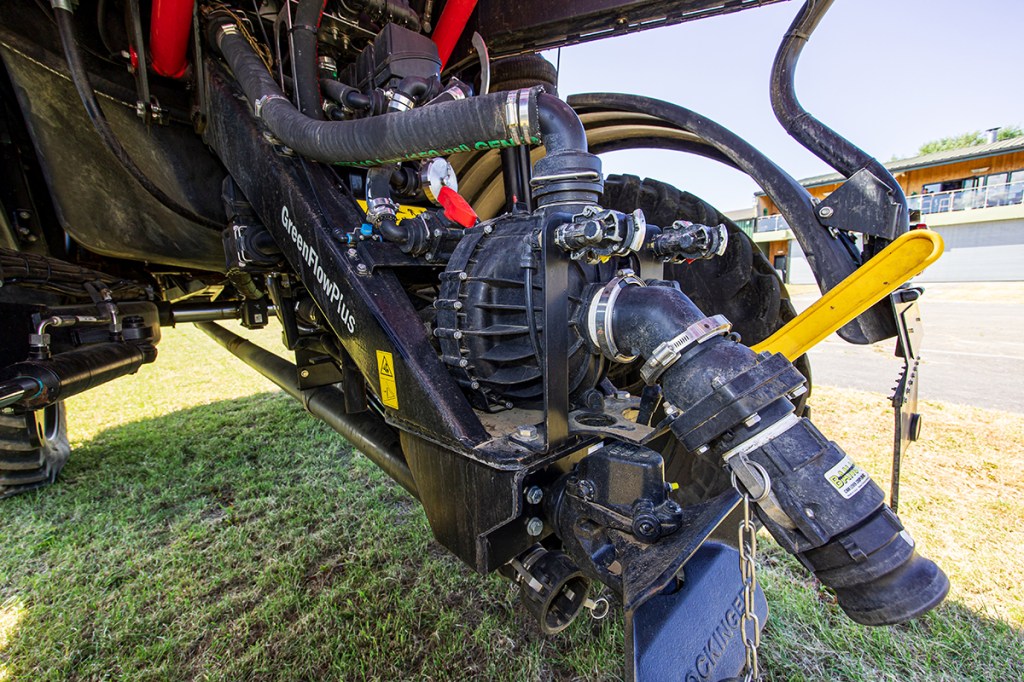
VF tyres are everywhere these days, they’re fitted to the Beckett’s sprayer too. There are four Fendt tractors on the farm, and all are equipped with Variogrip, so Steve is aware of the benefits of tyre pressure adjustment. There isn’t a CTIS on the sprayer, but Steve is of the opinion that the benefit of VF is being able to run the tyres at lower pressure without needing to inflate them for roading.
The Michelin SprayBib VF 420/95 R50 tyres are rated to carry a fully loaded machine at maximum permissible road speed. They will stay on until the end of potato protection season, then the “floatys” are fitted for autumn and winter spraying. The Vanguard can have the taller 710/75 R42 which offer a huge footprint and keep the machine up in soft conditions.
Power comes from a Stage V six cylinder Cummins engine producing 287hp, Agrifac stepping away from Volvo Penta where UK users often struggled to get out of hours service. B W S and other Agrifac dealers have Cummins diagnostic equipment which should improve backup markedly.
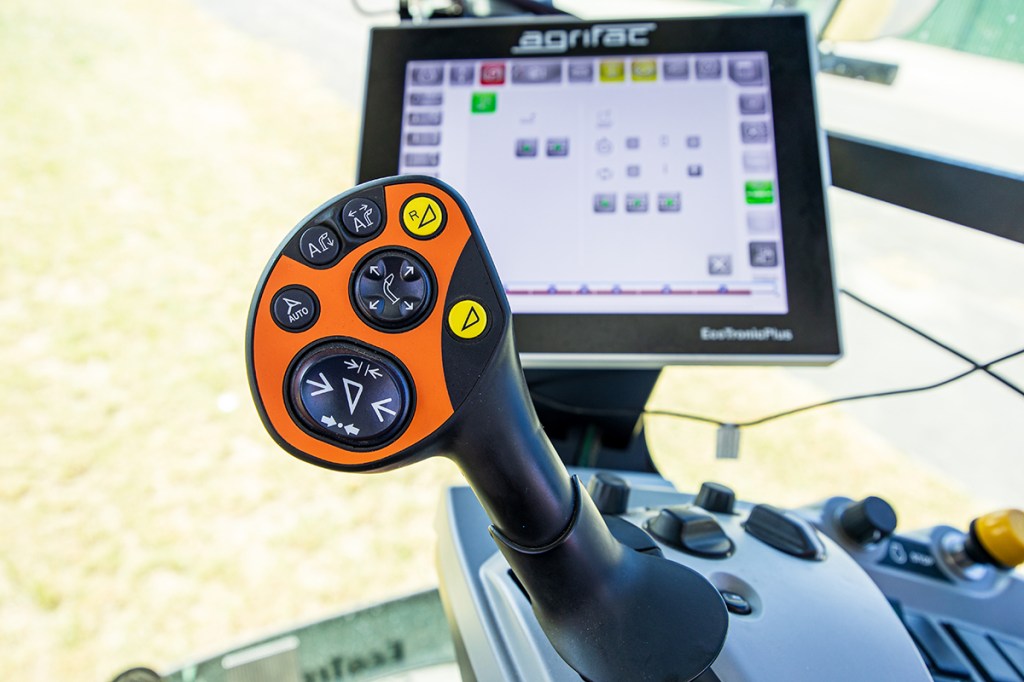
The cab
Cat 4 filtration is standard, an additional filter housing sits atop the roof with an automatic cab pressurisation system the operator is kept safe from airborne particles, there is an indicator light to show the system is operating. Because it’s a pre series machine the forage harvester instructions are on the multifunction lever, new machines come with a sprayer specific set of decals. Steve likes the lever with it’s analogue positioning rather than some machines that have a return to centre operation.

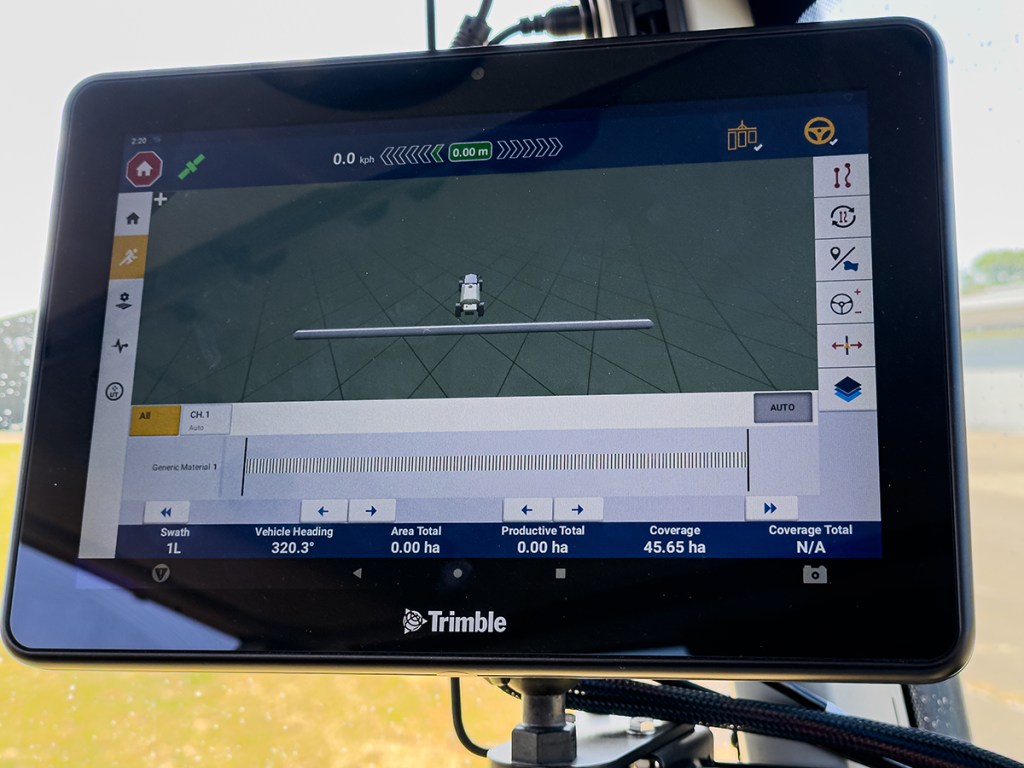
Precision Farming equipment comes from Trimble, with the latest GFX1260 screen and Nav 900 receiver. The system works with Centre Point RTX Fast correction which brings RTK accuracy without base stations, achieved through satellite connection.
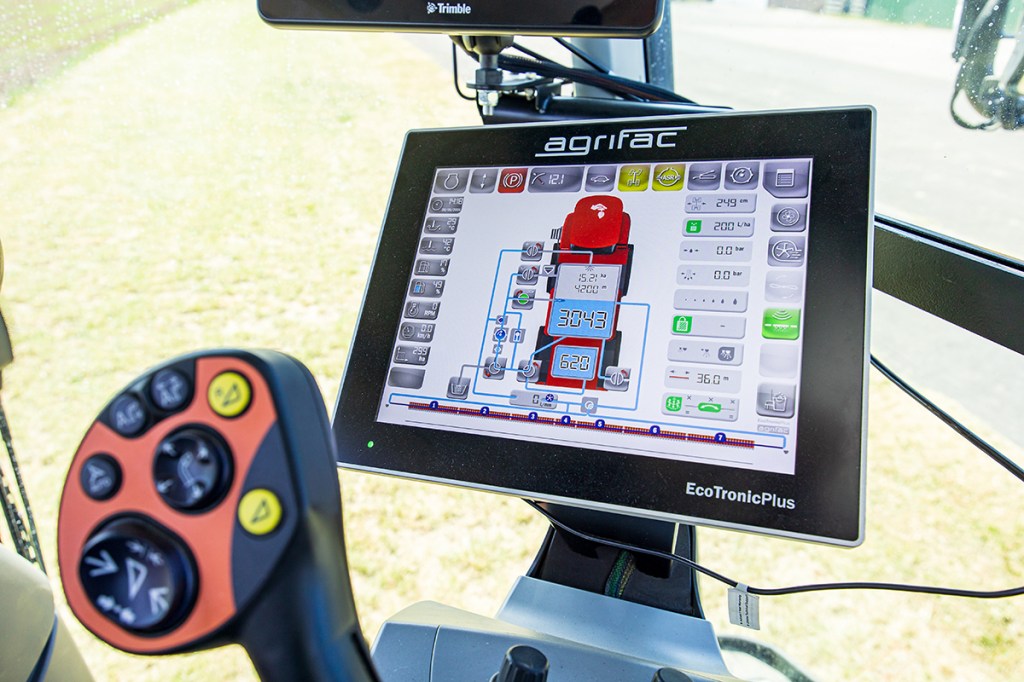
The GFX1260 looks after steering and rate control, able to handle 256 sections, it’s well in spec for the Agrifac. The system boots in 90 seconds from key on, Steve uses the same screens across his fleet, and in his combine, it provides a seamless system jumping from one machine to another, reducing stress
Using the Hutchinsons Omnia app for spray recs, that come to the sprayer from the agronomist digitally. Steve really likes the load calculator in the system. “That’s a very useful feature, particularly when you have some small fields, it tells you exactly what you need to put in the tank, and with PWM you can work down to the last litre.”
Summary
Replacing two sprayers with one wouldn’t logically sound like a way to increase output, but with advances in tech, Steve Beckett has done exactly that. The 25cm nozzle spacing combined with PWM has turned a challenging spray day into a day where he can still get on well, there is a money saving element too, with spray resolution so accurate the tank can be loaded to the litre.
Ken Topham
For more up-to-date farming news click here and subscribe now to profi and save.