DeLaval is adopting a different approach to milking groups with robots. We were able to take a closer look at the new batch milking concept in action.
KEEPING IT BRIEF
- After several years of development, DeLaval is presenting the VMS Batch Milking system.
- All of the air, milk and water hoses are routed overhead.
- Each robot in the batch milking set-up, averages 7.5 cows per hour.
- There is no forcing gate in the collecting yard.
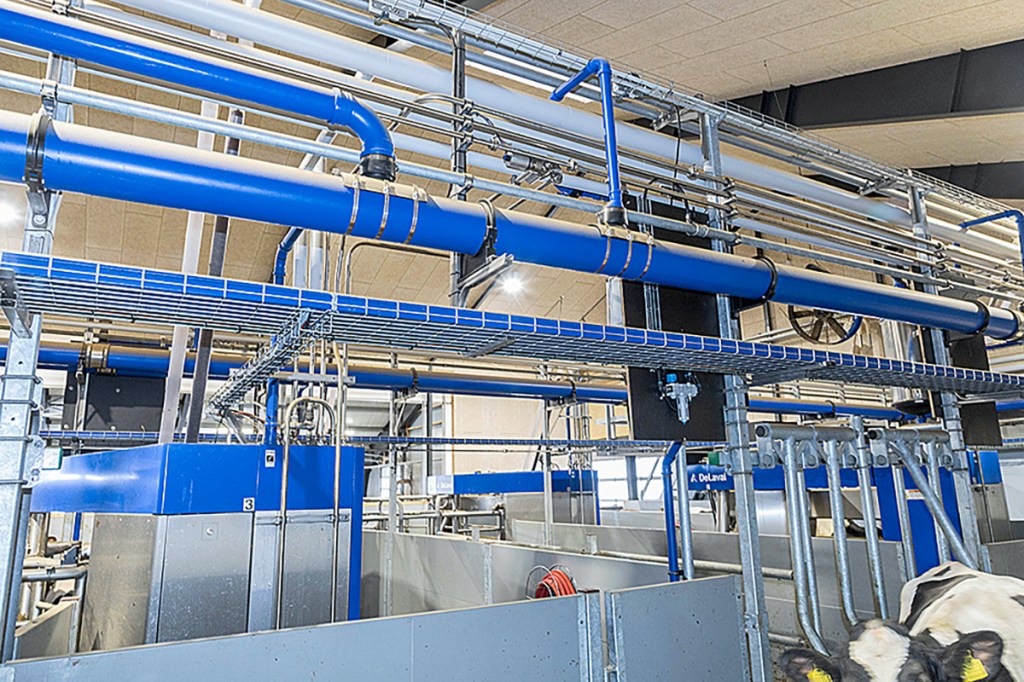
In the Batch Milking (BM) system, there are ten or more robots arranged side by side, and the cows are milked in batches — just as the name suggests. This approach is looking to appeal to dairy farmers who prefer milking in groups through a parlour and are not initially wanting to go down the conventional robot route.
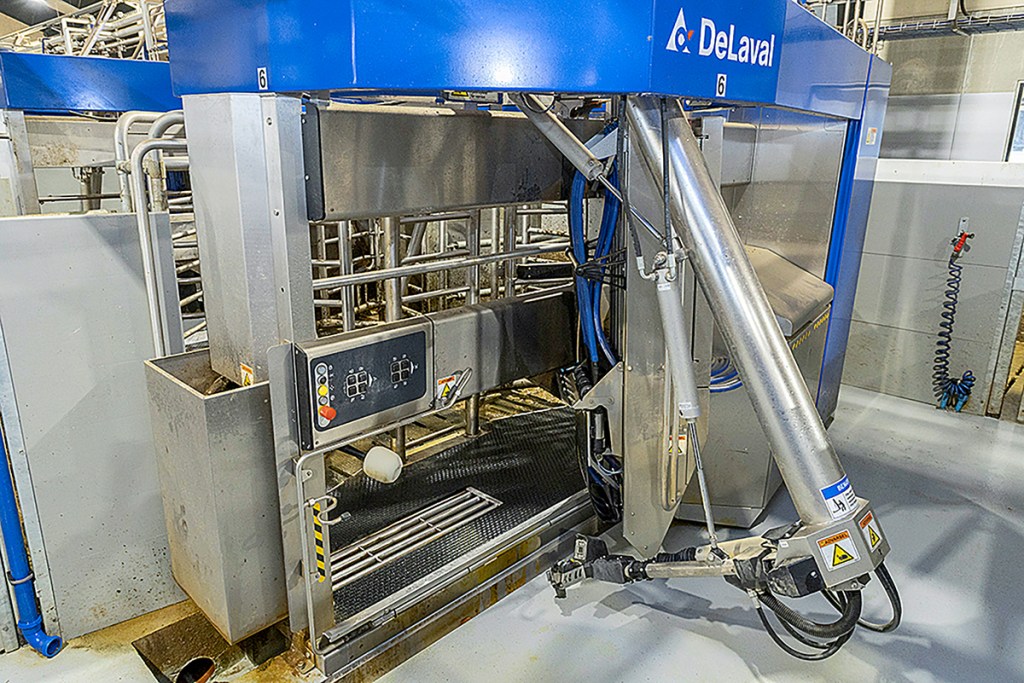
Compared to a conventional manned parlour the benefits are that you’re less dependent on skilled labour. Secondly, it eliminates the need to change the cow group sizes or feed management compared to individual milking robots. And lastly, opting for a batch milking system requires fewer modifications to your buildings.
Caught on the wrong foot
Batch Milking has been on the German market since 2018 — but not from DeLaval. In fact, the Swedish manufacturer struggled with the system for a long time — for several reasons. For example, DeLaval favours voluntary milking, and even with this new batch system there is no forcing gate in the collecting yard.
Another issue the manufacturer wanted to avoid was the higher cost of setting up the milking robots in a semi-circle. Circular builds tend to be significantly more expensive; for instance, routing of the curved pipes is more difficult than routing straight lengths. Furthermore, the company wanted to avoid needing to build an expensive basement to accommodate the milking equipment.
New solutions
The VMS Batch Milking system developed by DeLaval is based on arranging the milking boxes in either a U or in a double row layout. This allows them to install long, straight pipework.
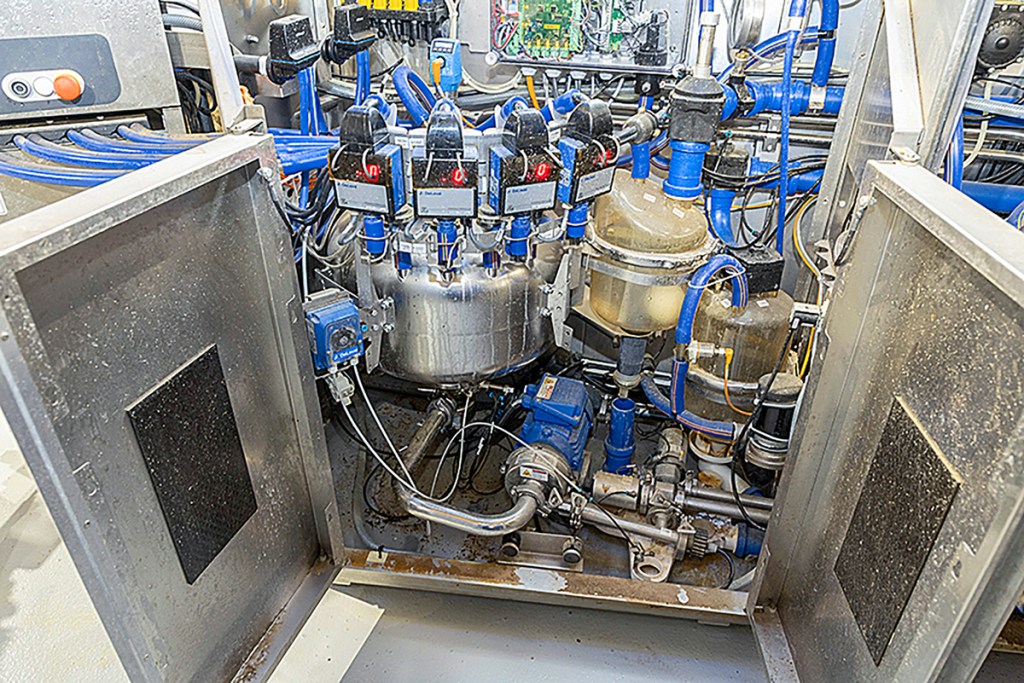
Another plus is that all of the pipework is above ground. Unlike a conventional milking parlour, the milk doesn’t flow downward into vacuum-operated milk pipes. Instead, the DeLaval set-up uses pressurised pipes to get the milk to the tank. For this to work, each robot is fitted with a 45-litre milk receiver jar which is then pumped into the pressurised line once the cow is milked. This approach ensures that there is a constant vacuum at the teat tip. This is mainly how DeLaval has been able to avoid building a ‘cellar’.
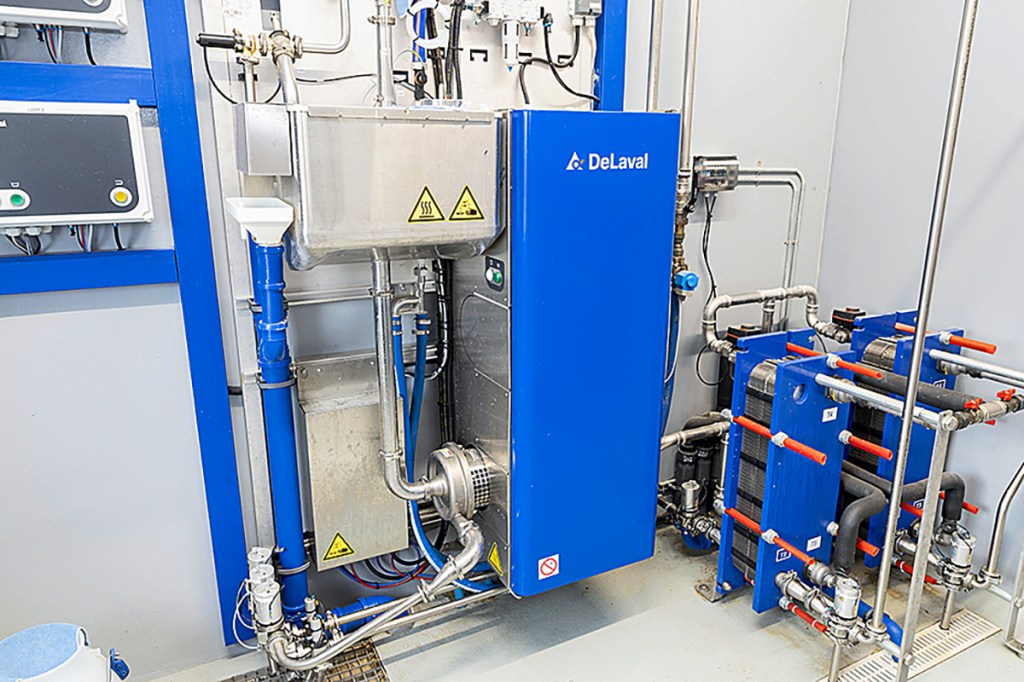
The 25mm pressure pipe, which is routed in a ring, is automatically cleaned with the so-called Q-Cleaner, something DeLaval has developed for cleaning the up to 200m long pipes.
Short waiting time
The farm we visited was milking 650 cows through a 14-robot system. The total space required, including the 6.0m wide waiting area, measured 34m by 18.50m.
According to DeLaval’s experience, the test farms have been achieving a throughput of 7.5 cows per robot unit, per hour. With a maximum waiting time of one hour, ten boxes should achieve a throughput of 75 animals per hour. To make the waiting time more comfortable for the cows, DeLaval is recommending a generous 2.20m² per cow.
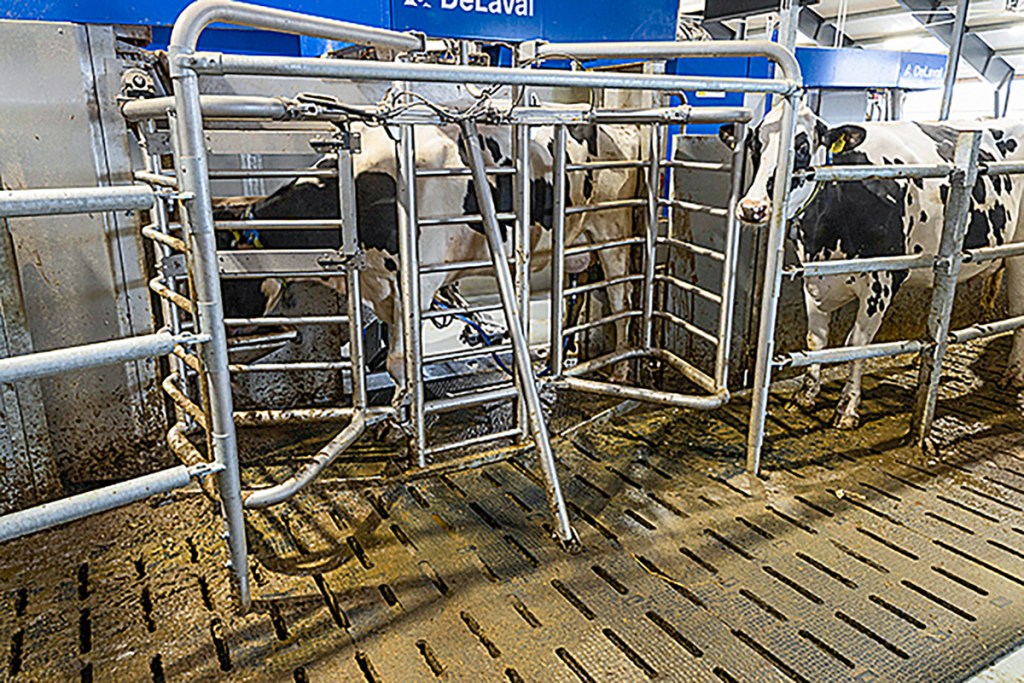
As mentioned, there is no automatic forcing gate in the collecting yard. Instead, DeLaval relies on the chaos principle and the so-called ‘pressure-and-no-pressure’ strategy. This means that new cows join the already waiting cows from the rear of the yard every 45 minutes, thus creating a natural pressure and encouraging the cows to voluntarily move on and get milked.
A close look at the system stats proves the manufacturer right: even without a forcing gate, the cows move quickly to the milking boxes, so hardly any time is lost between one cow leaving and the next one entering the box.
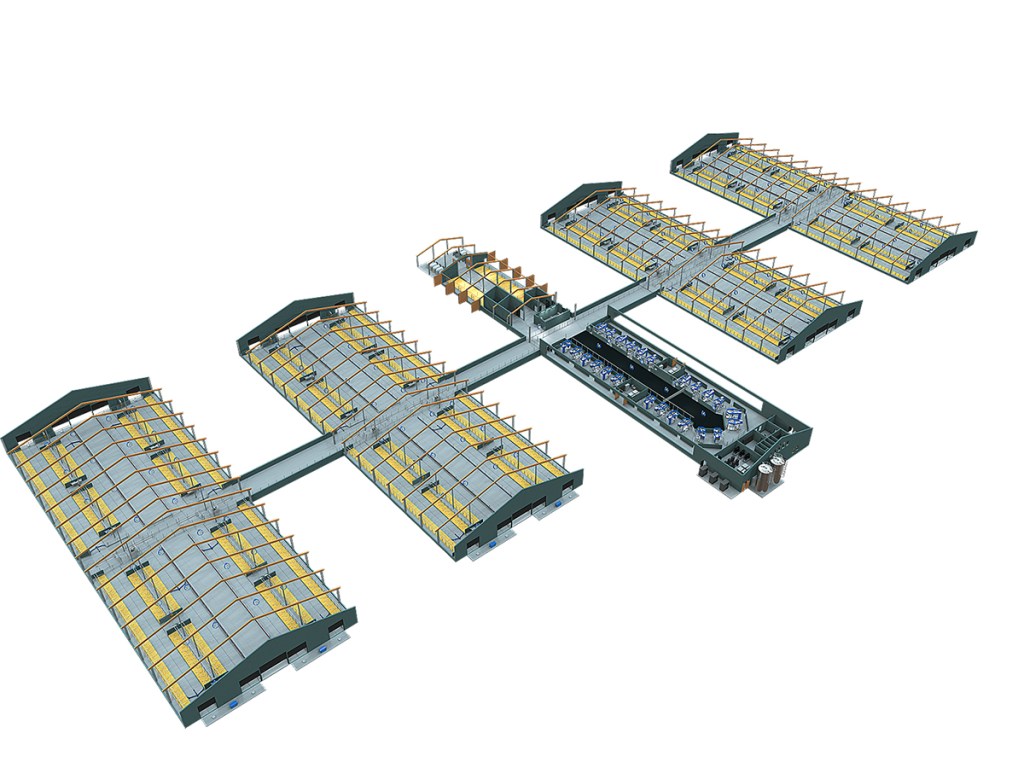
No searching for cows
As the groups are mixed during milking, it is important that each cow is then able to rejoin her own group after milking. DeLaval solved this by using its DSG5 drafting gates after the milking boxes. Once the animal is identified by its HDX transponder in its ear, the cow is released through one of the five gates.
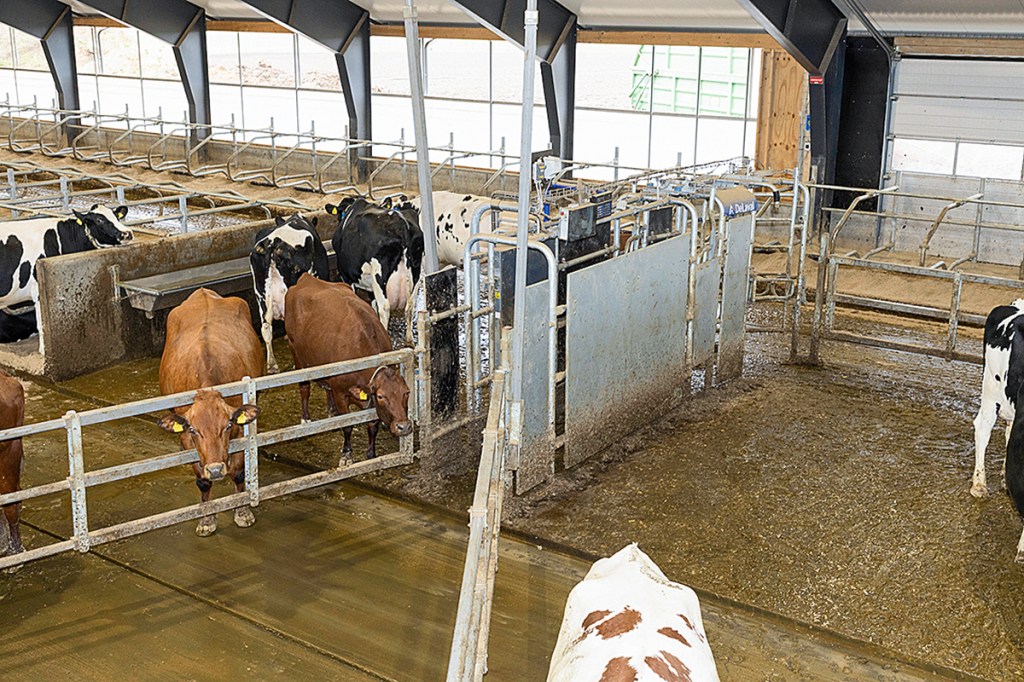
For a more rapid response, the gate locking cylinders are operated pneumatically. With only a few exceptions, the cows are sorted and returned back to their original groups. This means you rarely have to search for cows which ended up in the wrong group.
Problem cows milked first
The milk that is collected in the receiver is analysed for key quality parameters. If the measurements show that the milk is not suitable for going into the bulk tank, it is either diverted to the slurry tank or pumped to the calf barn.
Each milking robot has its own cleaning system. This allows each robot unit to be individually rinsed out with cold water or cleaned with hot water and chemical after milking an animal undergoing treatment — very effective.
The majority of dairy farmers in conventional milking parlours always milk their fresh cows etc at the end. DeLaval has turned this approach on its head, instead milking them at the start of the shift. The logic here is that the staff are still fit and more motivated to better attend the needs of sick animals. It also means that the milk for the calves is available much earlier.
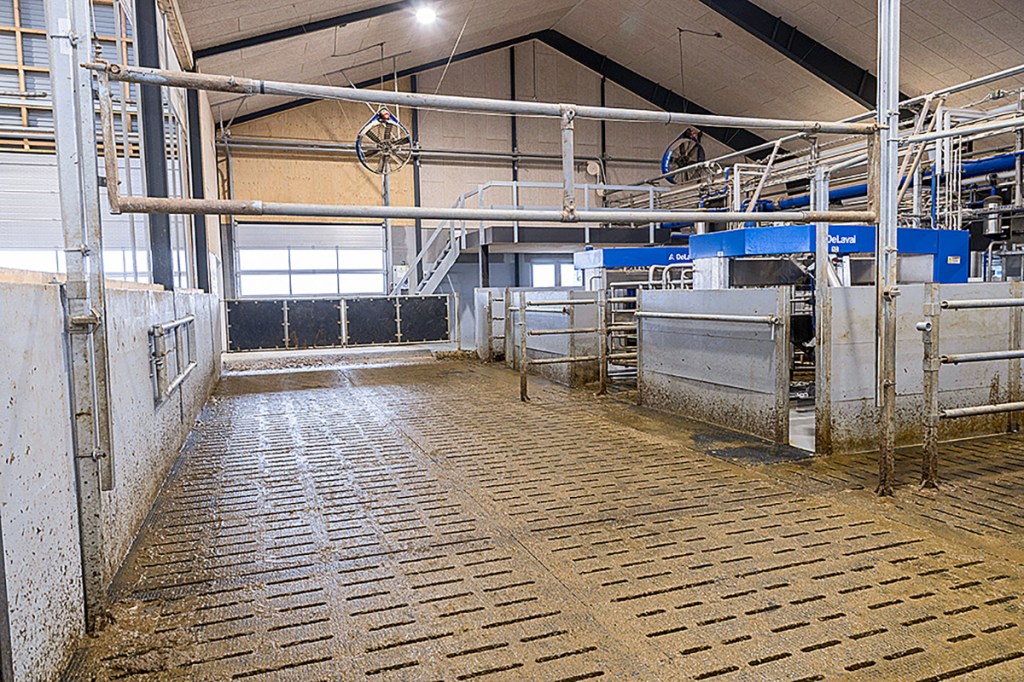
The special groups are brought to the front of the waiting area ahead of other cows. On the farm we visited, four of the 14 milking boxes were reserved for this purpose. This way, milking can still progress at a decent pace despite various rinses and system cleanings. As soon as the cows in the special group are milked, all the boxes are available for milking.
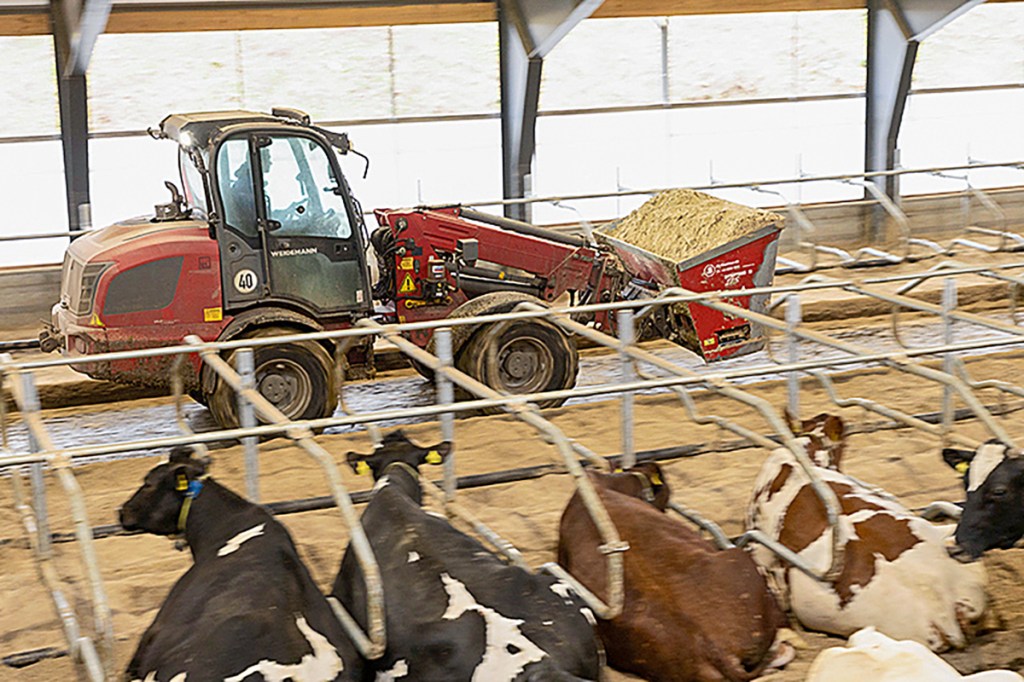
Milking in progress
For a herd of 500 cows with 14 robots, milking is recommended in two 5.5-hour shifts. The first shift starts at 4.30am, for example, and the second at 4.30pm. Two people are needed per shift to move the cows and look after the robots. The herd manager doesn’t need to be on hand all of the time.
Comparing man hours
When developing its VMS Batch Milking system, DeLaval focused on efficiency. A survey was carried out to assess if this was achieved. The result: when milking twice a day, the system requires 5.1 man hours per animal per year (this figure includes animal monitoring from the computer). With three milking shifts and an average of 2.5 milkings per animal, this results in six man hours per animal, per year.
By comparison, farms using a DeLaval VMS currently require 4.5 hours per animal per year, while the VMS models from 2010 are 7.5 man hours. Traditional dairy farms with a well-equipped 16-head milking parlour are up at 23 man hours, and according to the survey, milking in a rotary parlour requires 14.5 man hours.
Comparing costs
If you compare the process costs on a 500-head herd with three milkings per day, the following pictures emerges according to DeLaval’s figures: At 5.3 cents/litre milk, farms with eight decentralised VMS robots are the most cost-effective. The costs of milking in a 50-unit rotary are 5.6 cents per litre milk. A VMS Batch Milking system is 6.4 cents/litre (10 milking boxes), 6.6 cents/litre (12 boxes) and 6.9 cents/litre (14 boxes) for three milkings a day. The VMS Batch Milking system is slightly more expensive than the other DeLaval systems, but to make up, the farmer can make use of unskilled staff.
To achieve this, DeLaval has kept the batch milking robots relatively simple: for instance there isn’t a touch screen on each box.
Effective milk cooling
It is worth mentioning the milk cooling. DeLaval wants the dairy to be able to collect the milk at any time, day or night. This is achieved by various means — for instance, a small buffer tank. Alternatively, DeLaval now offers a storage system that consists of two large milk tanks and uses ice water fast cooling. We will have a look at this in a future issue of profi.
Summary
The VMS Batch Milking system, which has been developed by DeLaval, is aimed at farmers who want to manage their herd in groups rather than individually. Above all, however, batch milking offers the possibility of automating group milking without major alterations to existing buildings and already established group management.
Appealing aspects are the fact that DeLaval’s Batch Milking system milks fresh cows and sick animals first and that there is less of a need for highly skilled staff. In times of skilled labour shortages, this is a crucial factor that may help to overcome the 1 cent per litre or so higher investment cost.
USER EXPERIENCE: LENE AND MICHAEL JENSEN — THE BEST OF TWO WORLDS
Lene and Michael Jensen from Hammel in Denmark started using the VMS Batch Milking system in August 2024. Six months later, the two talk about their initial experience.
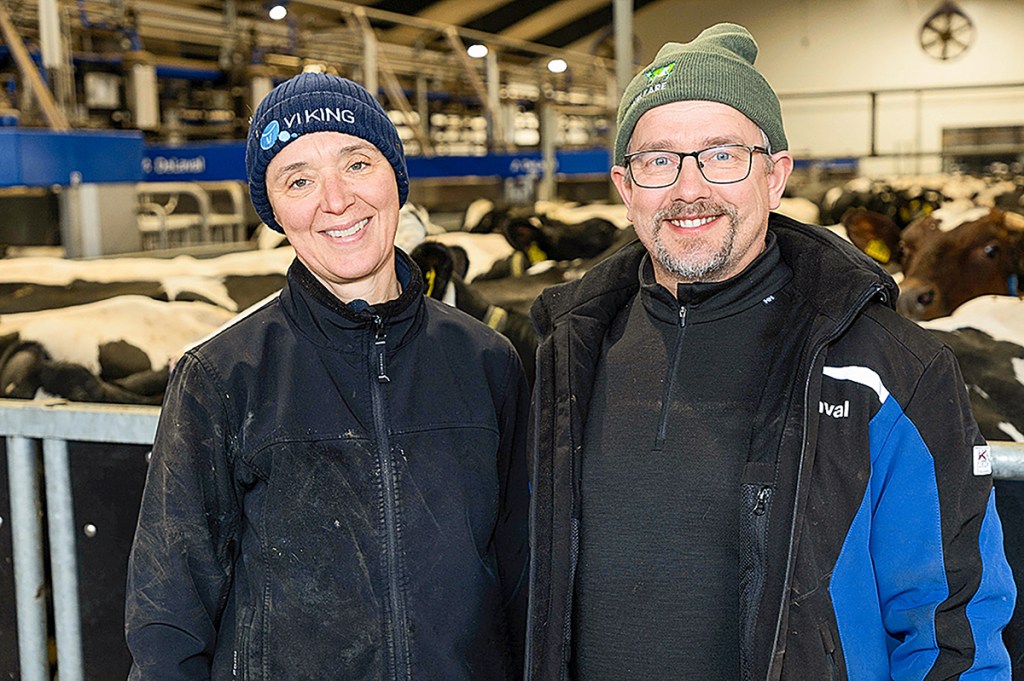
Well prepared
The farm has 650 milking cows with a herd yield of 14,073kg (fat-corrected; tested yields from February 2024 to January 2025). Despite the construction and installation work for the Batch Milking system, yields increased by 594kg over the previous year.
In 2021, the farmers were able to take over a farm with 100 cows. This expansion and new regulations on animal husbandry in Denmark were the reasons for constructing a new barn with space for 310 cows. At the same time, they decided to replace the 2 x 10 herringbone milking parlour with 14 milking robots.
The two 50-year-olds made the decision to automate milking with their own health in mind. The decision was also prompted by the fact that they are increasingly unable to find qualified milkers — even though the wage level is very high at €27-30 per hour.
Joint team breakfast
The decision to choose the DeLaval system was based on the farmers visiting a VMS Batch Milking farm in the Netherlands. Here, the Jensens realised that they could stick with their preference for managing the cows in groups and automate the job of milking giving the farming couple the best of both worlds.
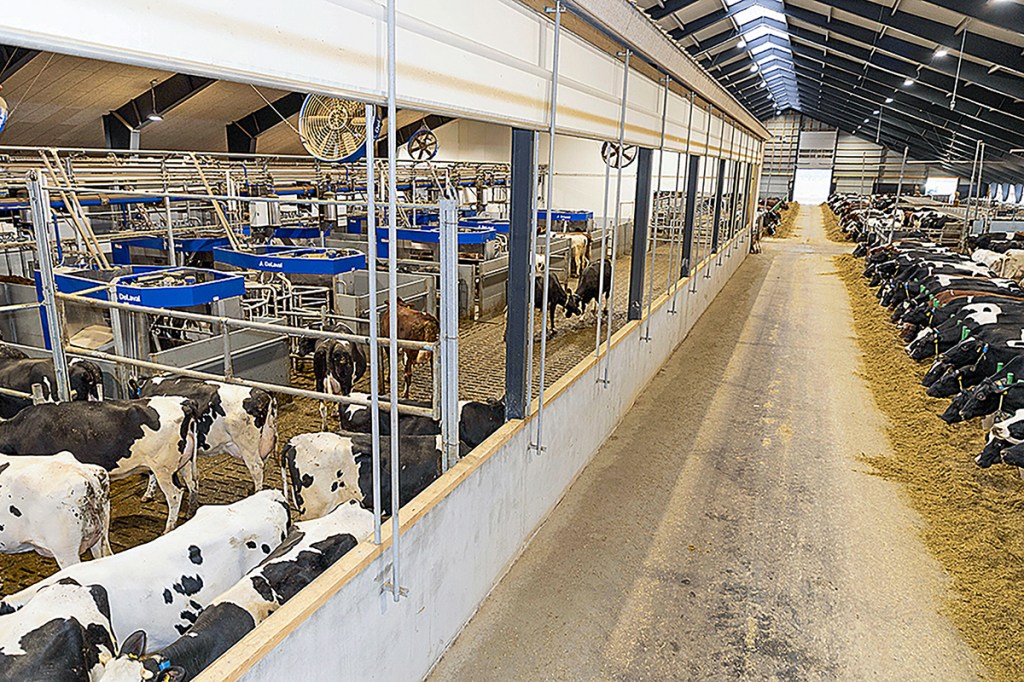
Their set-up currently has 14 robots — with the option of adding two more boxes to get them up to 16 in the future. The cows are kept in seven groups, each of them up to 110 animals.
Milking is done in three shifts: in the morning from 4.30 to 10.00am; in the afternoon from 1.00 to 7.00pm and at night from 9.00pm to 1.30am. Only the high-yielding cows are milked at night, which is five of the seven groups. This means the farm is achieving an average of 2.6 milkings per animal per day. The night shift is run by one person who also looks after the cubicles.
Lene and Michael Jensen introduced the tradition of a joint breakfast at 9.00am, while the last cows are being milked. “We wouldn’t have believed it, but the new ritual has helped us a lot in terms of team spirit,” says Michael Jensen.
The company currently employs seven to eight people, including Danish students and Ukrainian assistants. Lene Jensen is responsible for the herd management. In the medium term, they hope to reduce the team to just six people.
€10,000 per cubicle
The new barn for up to 350 cows was designed to meet the animal welfare regulations that will come into force in Denmark in 2034. This includes 8.0m² of space per animal, a cubicle length of at least 2.60m and slatted floor covering only 5% of the total space.
They estimate the total investment for the project is around €4.5 million. Around €3.8 million of this was spent on the new building, including milking robot and cooling technology. This equates to more than €10,000 per cubicle space.
With regard to his expenditure, Michael emphasises that this is now a high tech operation — with two milk tanks, an ice water tank and a special ice water cooling system as well as a small cooling tank for the calf milk.
Challenges remain
After seven months, Michael is satisfied with the system. However, he mentions there have been a number of challenges that primarily relate to communication between the various system components. And because the VMS Batch Milking system is relatively new for the manufacturer, DeLaval is still somewhat behind when it comes to integrating it into the management system. “But the company will certainly get that sorted soon,” says Michael confidently.
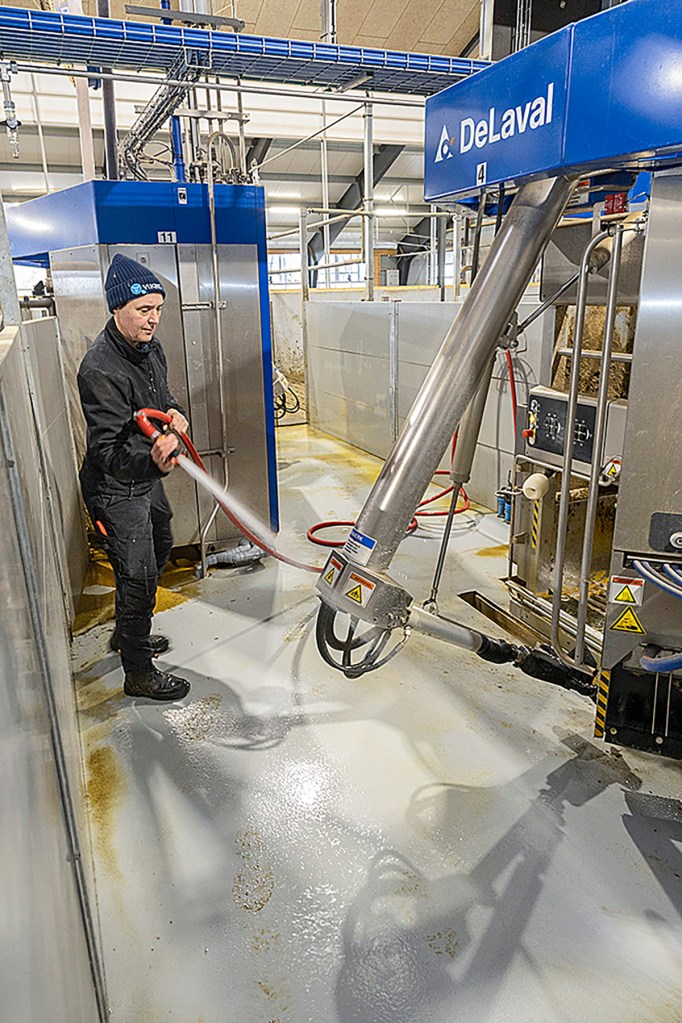
Lene and Michael Jensen underestimated the effort of cleaning the floors, including the perforated walkways around the 14 milking boxes. Cleaning takes 40 minutes. With three milkings, that’s two hours per day dedicated to cleaning. In addition, the associated water consumption is around 4.0m3 per day.
Herd management
In terms of animal health, they benefit from the Danish regulations that allow farmers to carry out certain treatments themselves. Michael also does all of the AI work, while a vet checks the herd every three weeks.
Future prospects
Lene and Michael Jensen planned their investment deliberately for the next 15 years of their professional lives. They wanted a system that was practical for them despite their age.
The Batch Milking system also offers them the opportunity for continuous growth. So, should their four children be willing, nothing will stand in the way of a continuous expansion of the business.
Summary
Lene and Michael Jensen love working with cows. By investing in the VMS Batch Milking system from DeLaval, they are able to continue running the farm largely independently of milking staff, with a view to their own health as they grow older.
Despite the high investment costs, the farmers calculate that production costs have not increased as a result of the changeover. One of the reasons for this is that labour costs have already been reduced — and will probably continue to fall. After six months of experience, the couple has no regrets.
Martin Zäh
For more up-to-date farming news click here and subscribe now to profi and save.