Lichfield natives S P Robinson & Son had been squeezed on all sides by construction, on what was their home farm in Staffordshire. So, when a 350ha farm became available in neighbouring Shropshire they decided to move to a new home.
Just outside Market Drayton, the pedigree herd of Phildor Holsteins has a pretty swanky new home. S P Robinson & Son broke ground here in 2021 after a roller coaster with planning permissions which were mostly ammonia related, and what led to the underfloor manure handling system and haven’t had a negative impact on the day to day operation.
The barn floor design takes a wide area and drains the slurry into smaller channels, which reduces the amount of surface where the urine and faeces can mix, which causes the release of ammonia.
Robot decision
It’s not very often a new dairy farm is built from scratch, but when you do, it shows how building design, and materials combined with up to date equipment can make a super building. The two neighbouring sheds are 78m long, 35m wide and 14m high at the apex, are quite imposing buildings when you stand next to them.
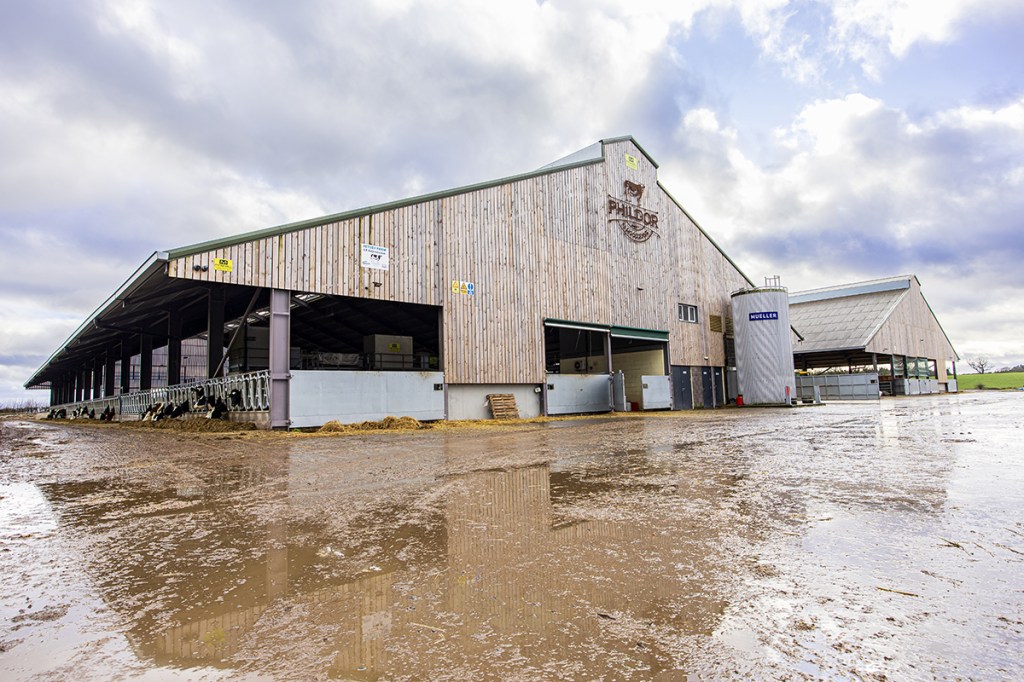
A covered passage makes it easier for shifting animals between the sheds and means the cows don’t have to go out on the yards. Likewise, people can use the slip gaps between posts in several places so there is no need to open gates, increasing safety.
When at full capacity the aim is to have 300 cows, all milked by robots, currently there are five, three in one building and two in the second. The choice of robot came down to a Fullwood Joz system, the main driver was the flexibility in the service.
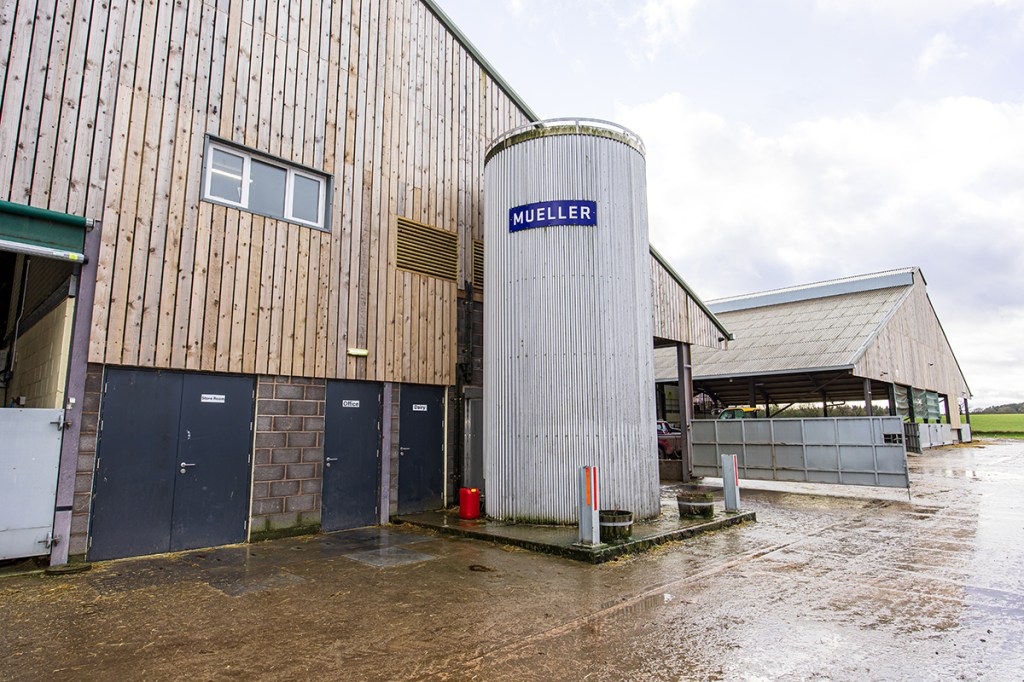
“Some of the other systems are very controlled, from chemical contracts to service,” points out, Henry Robinson. “We wanted to be able to do basic repairs to have some independence and buy cleaning products where we wanted.”
And this flexibility hasn’t changed since Fullwood was bought by Joz in the time since the Robinson build started. The Merlin robots are built in the Netherlands, with the more traditional Fullwood milking parlour equipment coming out of the Ellesmere base.
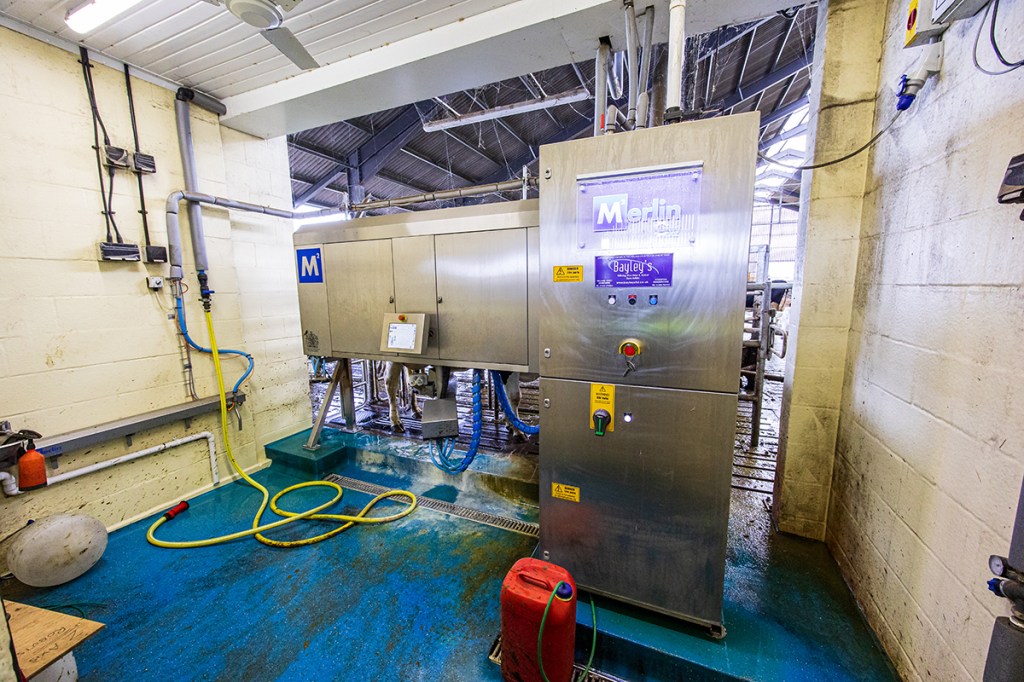
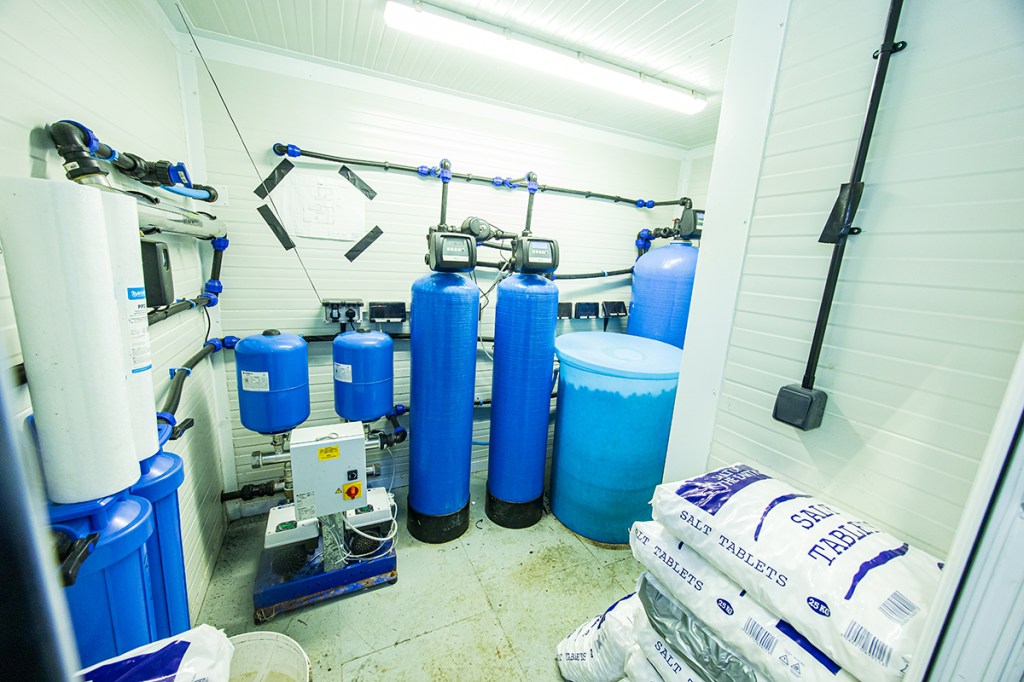
Slurry strategy
There is almost as much going on under the slatted floor as above. The Robinsons wanted sand bedded cubicles, but you will have no doubt noticed the slat covered passageways in the photos. Under each slatted alleyway, there are two 1.5m wide channels, each with automatic scrapers to prevent sand laden slurry from settling. Designed and installed by Midlands Slurry Systems, the setup largely looks after itself.
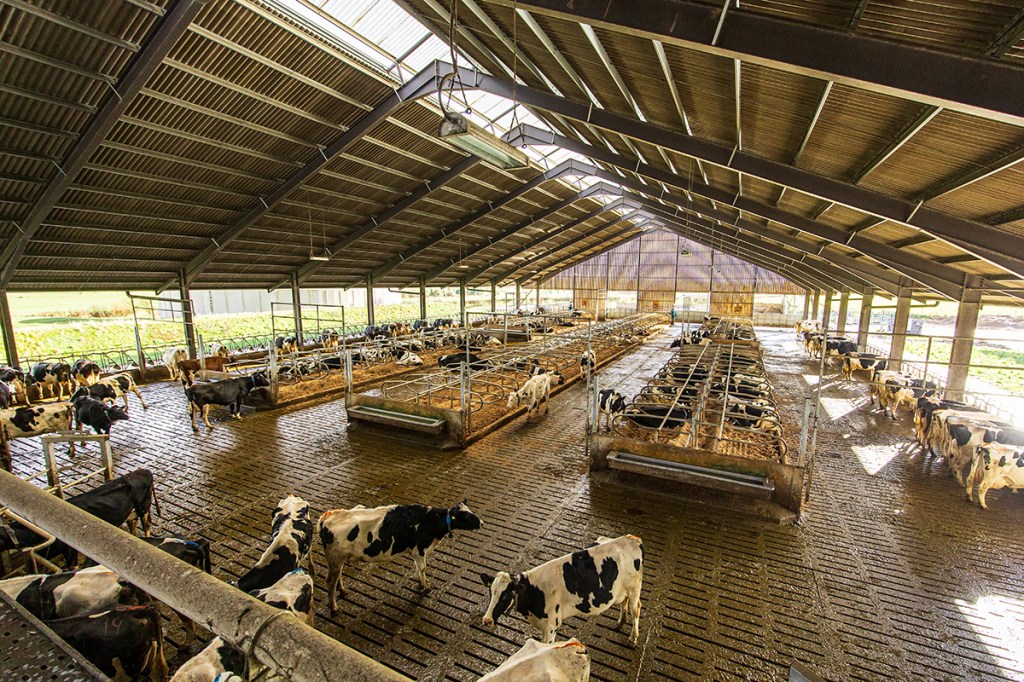
Runny material drops through, while stickier dung and sand is scrapped out once per day using an Avant mini wheeled loader. Meanwhile the automatic scraper system utilises a wire rope system from LJM. Each building has two cable units each operating four scrapers in an alternating action. These pull the slurry to one end of the building where a turning chain then moves the material from both barns to a central point where gravity then takes over and the material flows to a reception pit next to the separator.
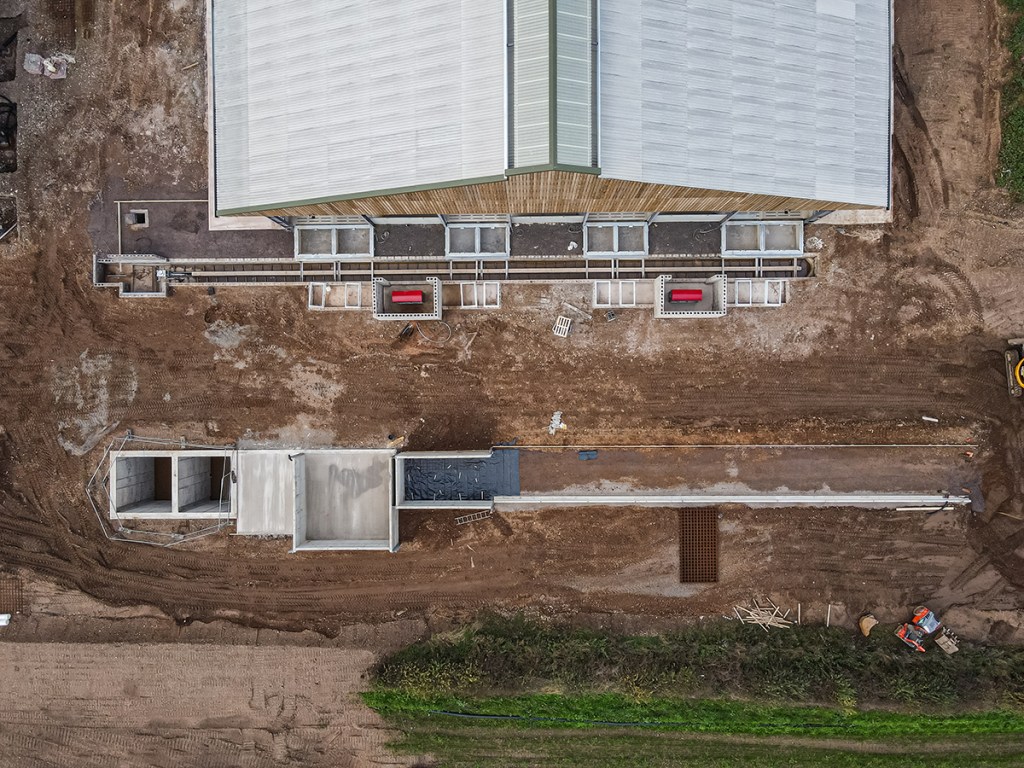
From here, the slurry is pumped to a Sperrin Optiflow separator which is well suited to a sand bedding format, with a rotary screen and rubber roller system to extract the fibrous material. Naturally there is sand in this element, as there is in the liquid – there is about 30% loss of sand through the whole manure system.
A sand lane was part of design from the outset, the separated liquid runs down a slight incline, depositing the sand as it meanders down the 30 metre slope. At the end of the sand lane is a drain that is slightly raised.
“We get quite a lot of fibre and some sand in the separated liquid which we still consider slurry rather than dirty water,” explains Henry.
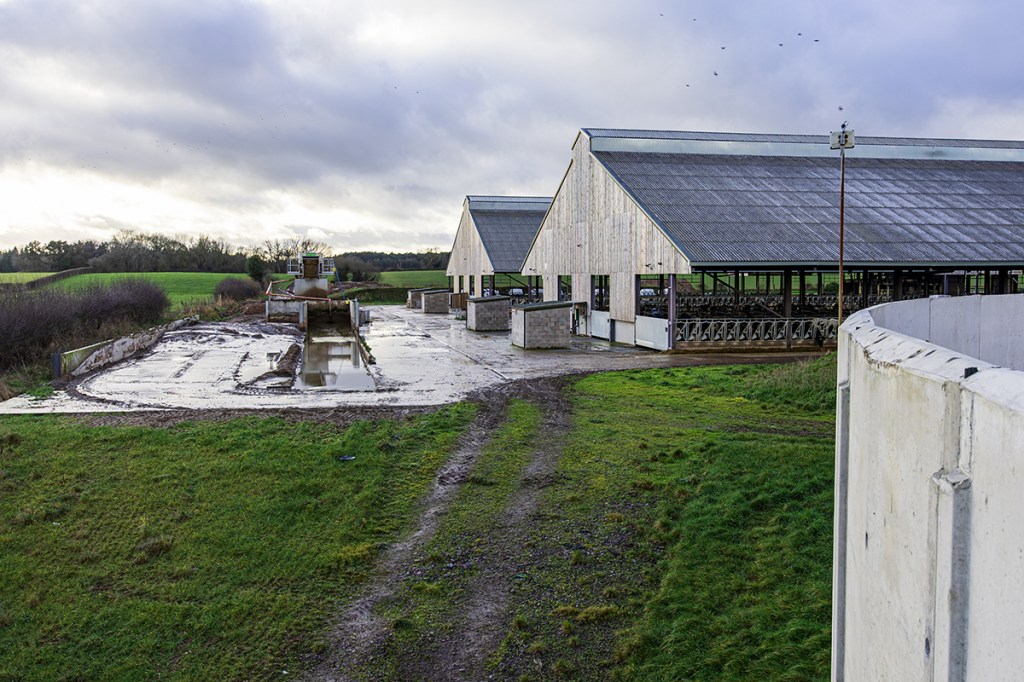
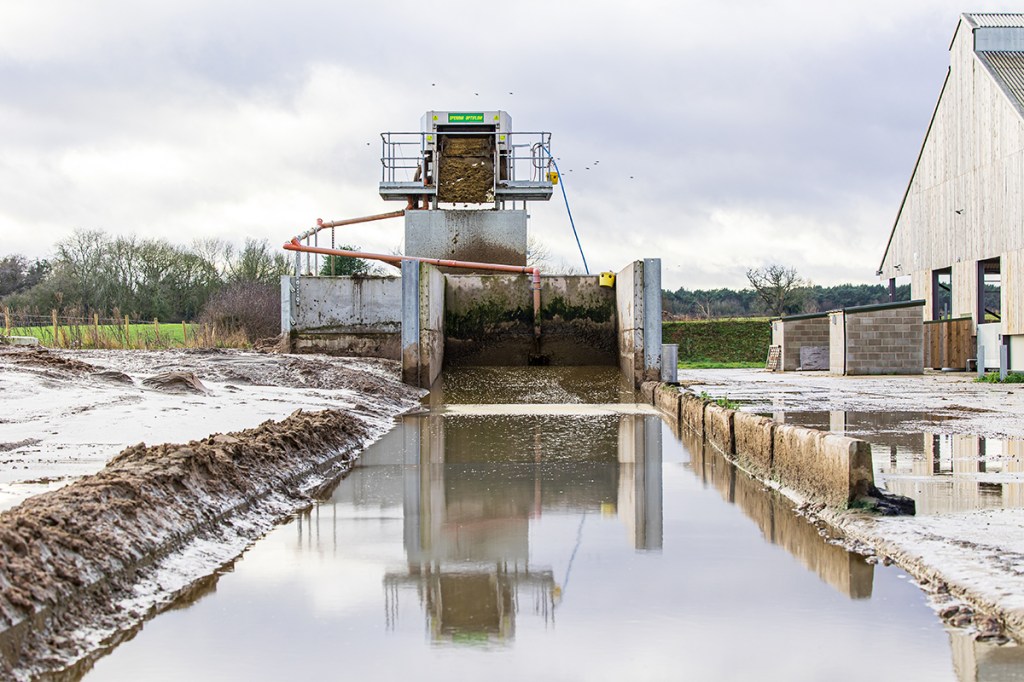
The settlement lane needs a weekly clear out, the sand is heaped on drained concrete pad next to the separator and then moved to a stockpile in the field next to the yard, this allows the sand to dry to a re-usable state which takes about six months. Recovering about 70% of the sand put in each week, the current head count uses in the region of 25 tonnes per week, of that five has been recycled.
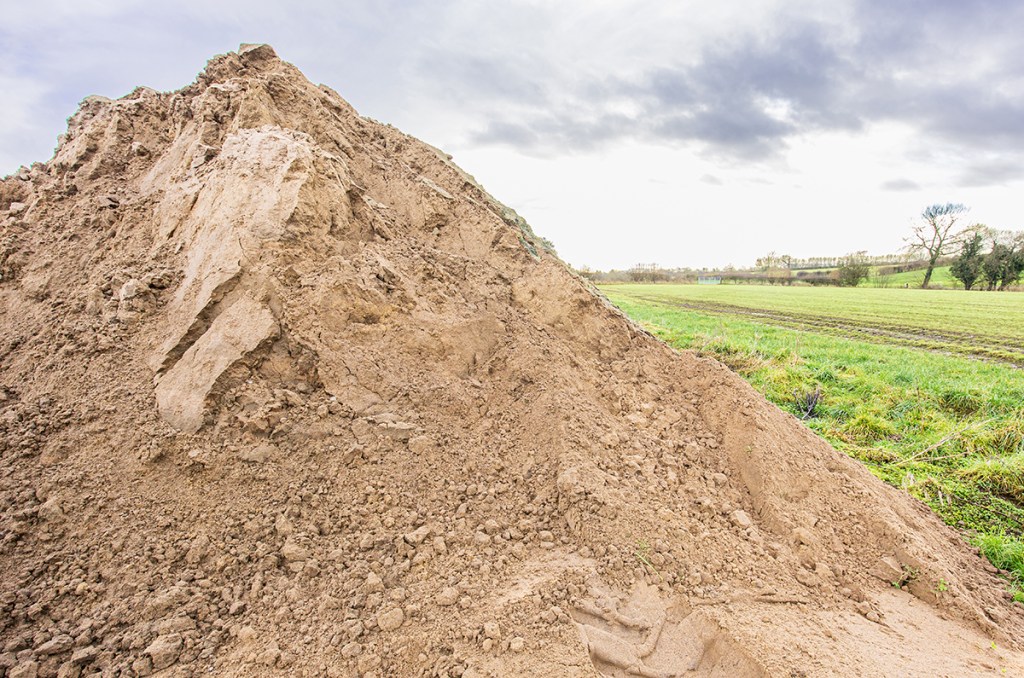
The effort is minimal as far as reclaiming sand is concerned, the lane does much of the work, and cleaning it requires less than an hour a week, including the time it takes to shunt some drained sand to the field pile. Recovering sand also reduces the amount of abrasive material going through the spreading equipment.

The farm is in an NVZ so there is six months’ worth of storage in a 6,100m³ concrete store. This was calculated for the target herd size of 300 cows, the store and separator should be self-managing, one of the few hiccups on the farm are the float switches, that switch on pumps when pits get full, so these are due to be replaced with a radar eye instead of mechanical units to improve reliability.
Sand isn’t a massive issue, Henry recons there is 30-40cm in the store, after over two years of milking, he anticipates it will require digging out every five to seven years. There are two pto driven agitators in the bottom of the store, these help to move some of the sand around when there is opportunity to spread, and get some of it suspended in the liquid, and onto the fields.
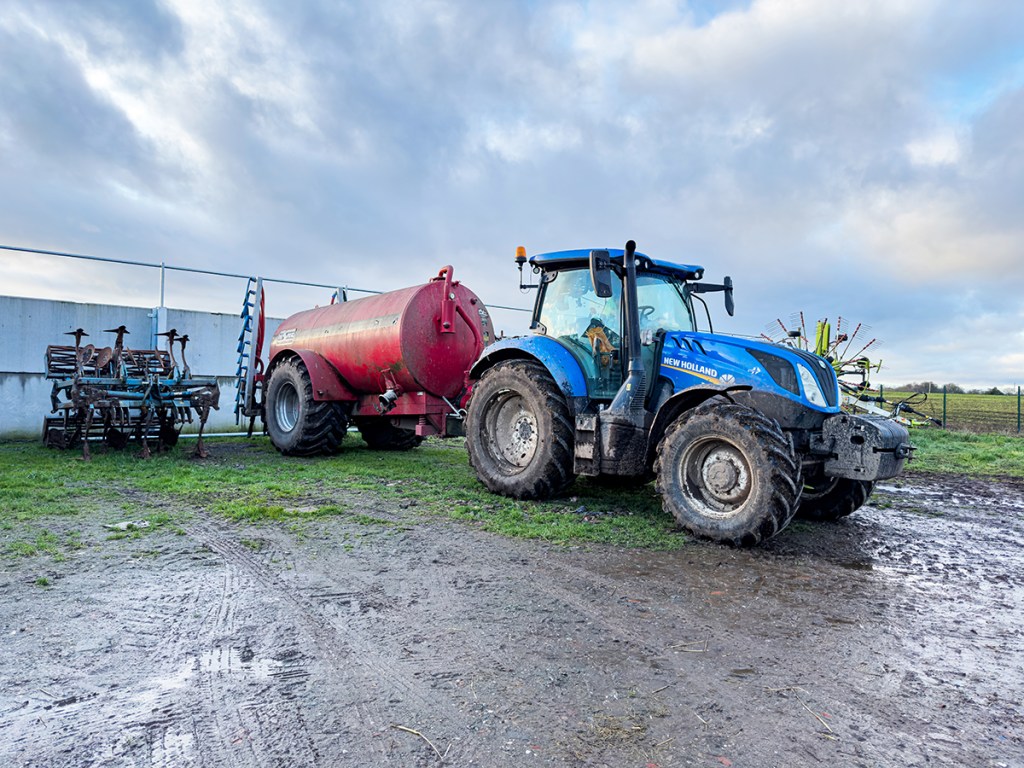
With a 11.8m³ (2,600gal) Hi Spec tanker equipped with a 7.5m dribble bar there are approximately 534 loads in the store, so the tank is more of a level management tool, used to chase winter grazing sheep off the silage pasture in early spring, and to cover silage ground after cuts. Contractors come in with an umbilical system at least once a year to empty the store or as close to as land availability permits.
Fields of feed
The business is almost self-sufficient in its farming operations, running three New Holland tractors and a Valtra. Grass silage is made with a forage wagon, with the 55ha of maize harvested by a local contractor. The farm makes around 45ha per cut of grass silage, five times a year.
Currently around half of the 350ha holding in Market Drayton is rented out. Some of this will be brought back as the head count reaches its target, and more fodder is needed.
Growing in the region of 80ha of wheat and barley, which is combined. There is a grain store on the yard and with their home farm in Lichfield they are self-sufficient in straw. There is a block of 25ha under the low input grass SFI scheme, which is made into hay once a year, this is used in the dry cow ration with straw.
The farm aims to only plough for maize, with a mix of black and red sand they can use a cultivator and Weaving tine drill for cereal establishment. The same equipment is used for cover crops after maize, planting Westerwold ryegrass so a cut of silage can be made in favourable years before the next arable crop.
The mixed feed contain grass, maize and for dry cows hay from the SFI low input pasture, straw is used in the dairy ration, this is processed into the farms new 20m³ Siloking tub feeder from a Kverneland 863 Pro straw chopper.
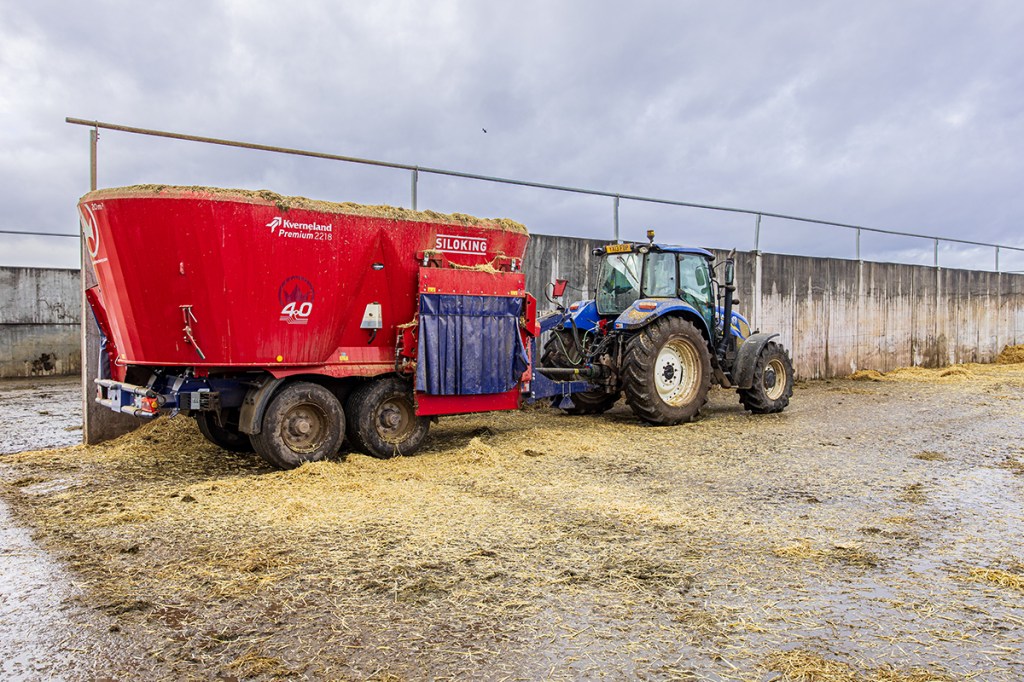
Grass silage is gathered with a Pöttinger Torro 6510, the flexibility of the robot milking system allowing the family team to do this job themselves. They also carry out as much of the field work as possible, with only maize drilling and harvesting as well as combining and the umbilical work contracted out.
With five 2,000m³ silage clamps, the aim is to always have one empty, one for maize and the others segregated with cuts of grass silage. The silage is regularly analysed to ensure the TMR is optimal. The farm uses membrane sheets with a cover sheet and a mix of rubber mats and pallets to hold it down.
Using the Cow Connect system, the cow ration is easily adjusted as well as the head count. Henry says they’re currently working on 51kg fresh weight ration per cow per day, of that 12.5kg is forage dry matter. This yields 34l per cow per day, with a target of 40L when they’re at full numbers and can tweak ration further.
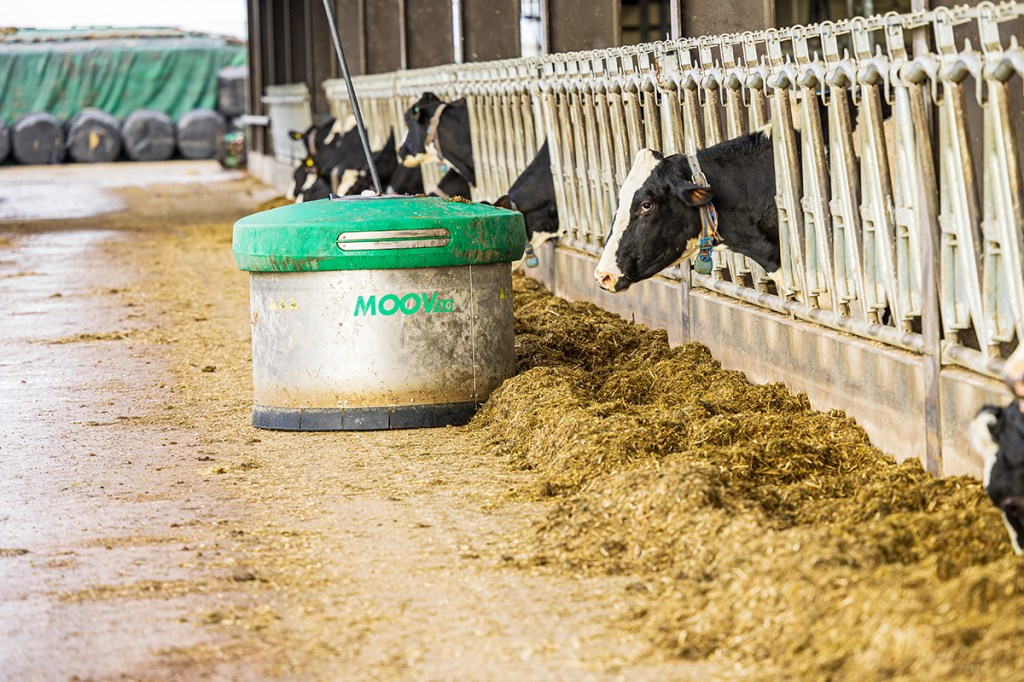
There is a Joz Moov 2.0 robot pushing the feed up on an hourly cycle, keeping forage close to the barrier from the once a day feed out. There will be one pushing robot per shed, although the second shed hasn’t had it’s pushing robot commissioned yet so this is done with the JCB and tyre pusher, which has highlighted how much time this chore tan take. All of the feed fences are along the outside, so there is no cow wrangling to feed, it’s all designed to be easy and have minimal stress on staff and stock alike.
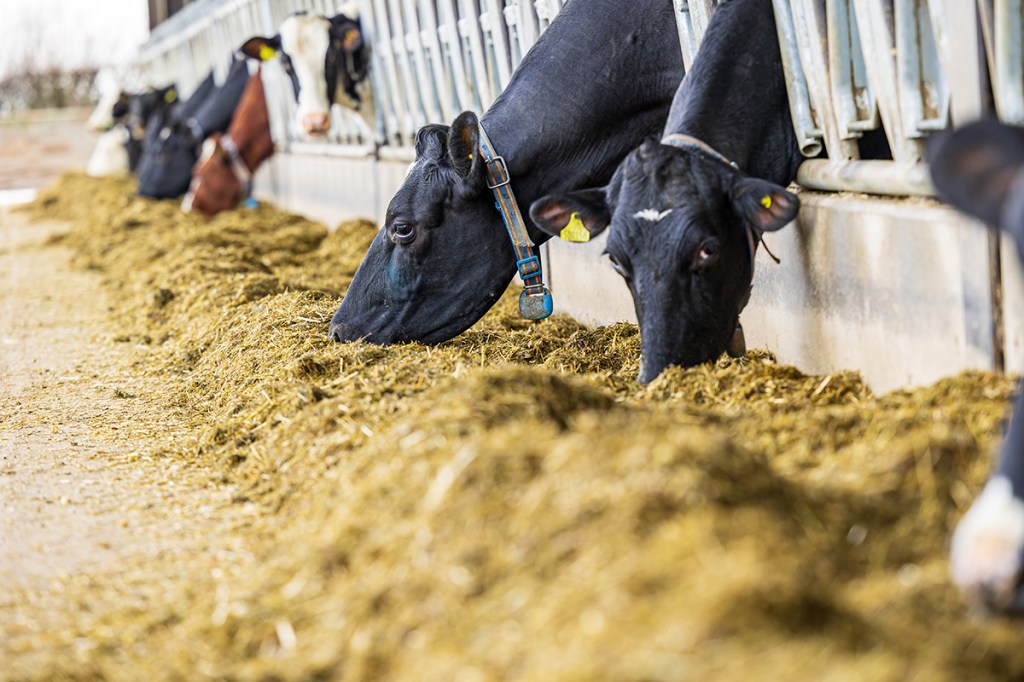
The sheds
Built by Minshall Construction along with the gates, cubicles and gantries, the top of the buildings is 14m, with a 25° pitch. At the apex the roofs there is a ventilation cap the full length of the building, this and the profile of the roof keeps airflow high, and negates large electric fans for the summer, saving energy.
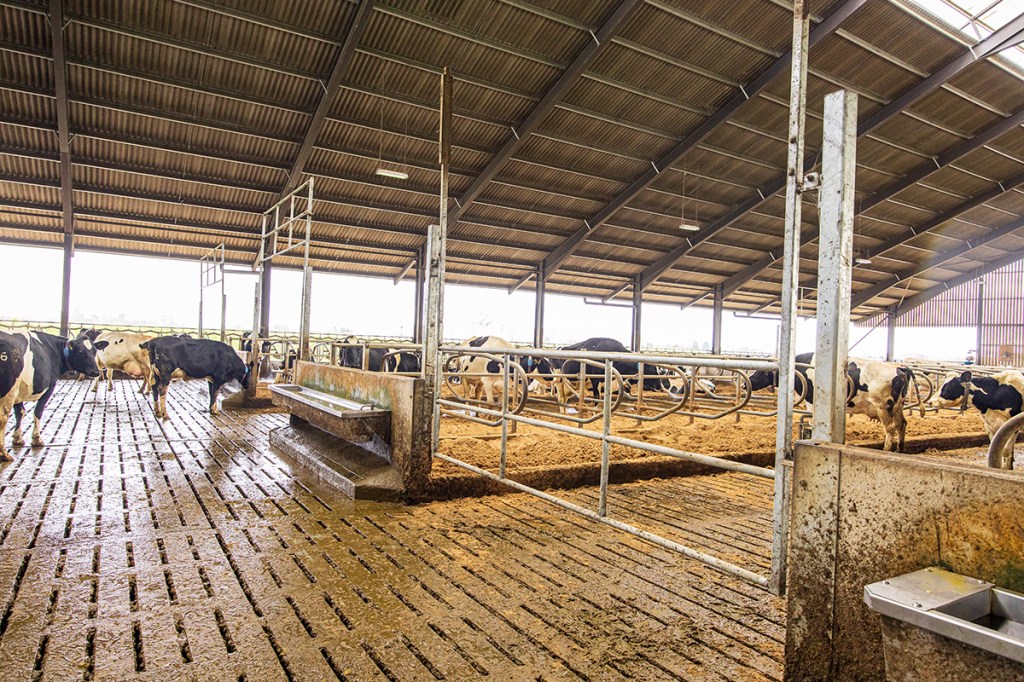
Solar panels on the roof is the next step, which would suit the system well, the farm can draw down during the day as everything is running, and use mains at night. Probably one of the best suited farms for solar use. There are projects ahead of this, but it’s on the radar.
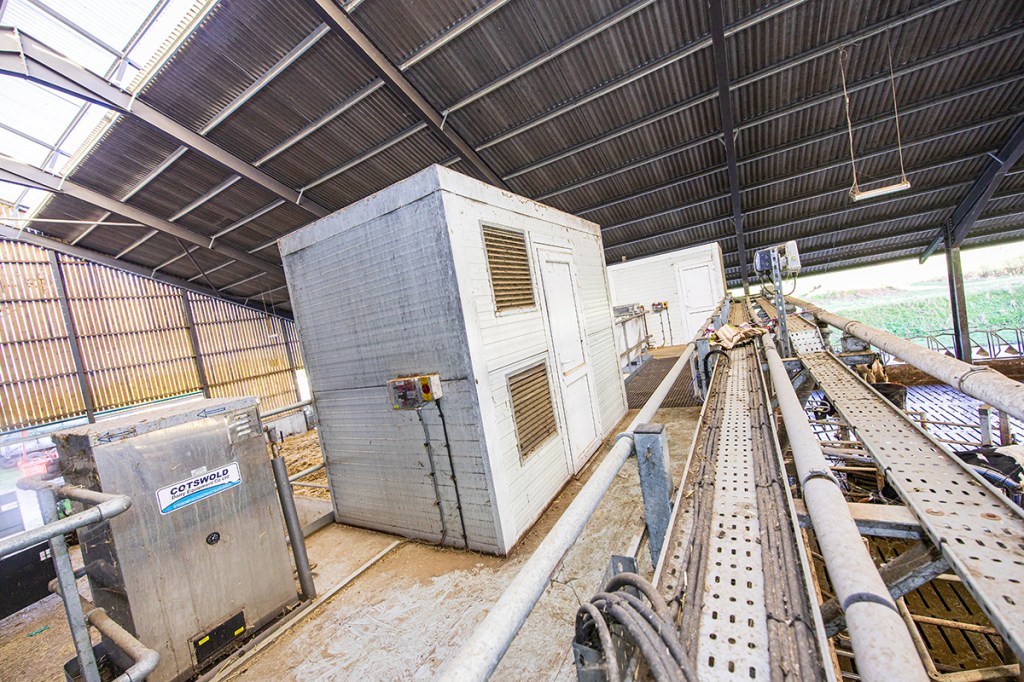
Above the robot boxes are little plant rooms for compressors and vacuum pumps, these are constantly running and use energy 24/7, which is the downside to robot milking, everything is always on. This does make the farm energy dependant, to mitigate power cuts there is a 160KVA diesel generator on site.
Though everything “is always on” much of the pump equipment is running in an on demand manor, from inverters, spreading the peak load over the system. The aim is to have a 10% wait time on each box, that is the time it’s ready and waiting, this means the system is at optimal usage.
The cows do have to wait but not so long they get bored and walk off, which means human intervention to come and encourage them into the robot. Each cow is averaging 2.9 milkings per day, and 6.1kg of nuts per day, dispensed when they enter the robot.
The passages can be partitioned with gates, these have been made as a swing over arrangement, so they are up out of the way when not needed, and have a counterbalance so they’re easy to manage. It’s all about ease of use in the shed, the water troughs have a drain plug rather than a tipping set-up, this was deemed a simpler solution, a quick swill out with a hand brush is all that’s needed.
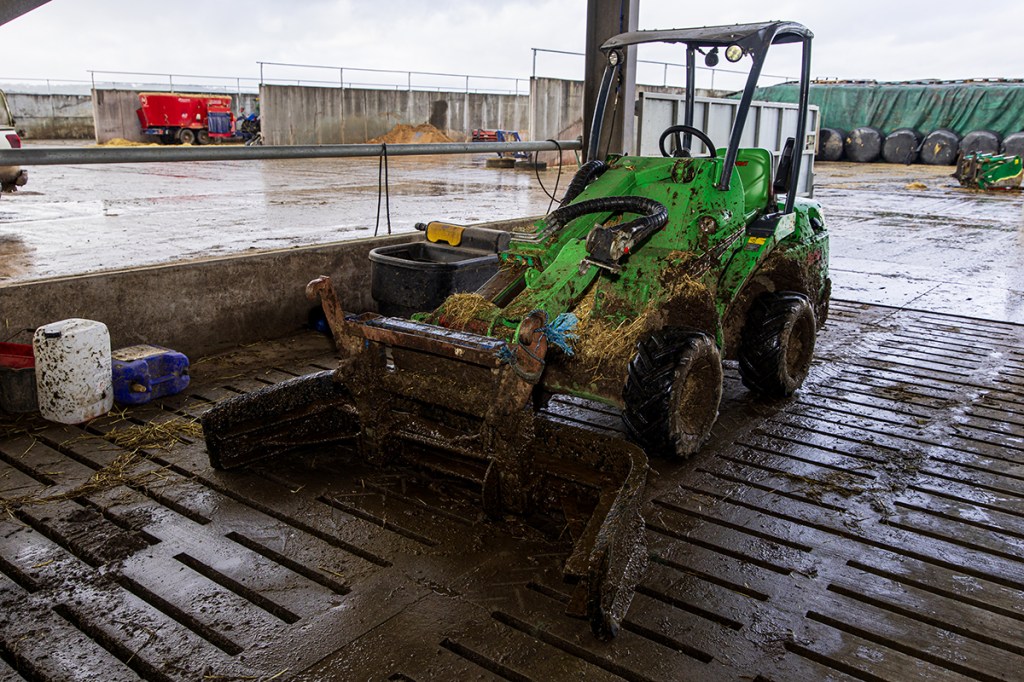
An Ag Dispenser 150 is used on the farm’s JCB 538-60 to top up the beds, and in between re-fils the Avant 523 is equipped with an off-set rake that fits under the cubicles, so the operator can freshen up the beds.
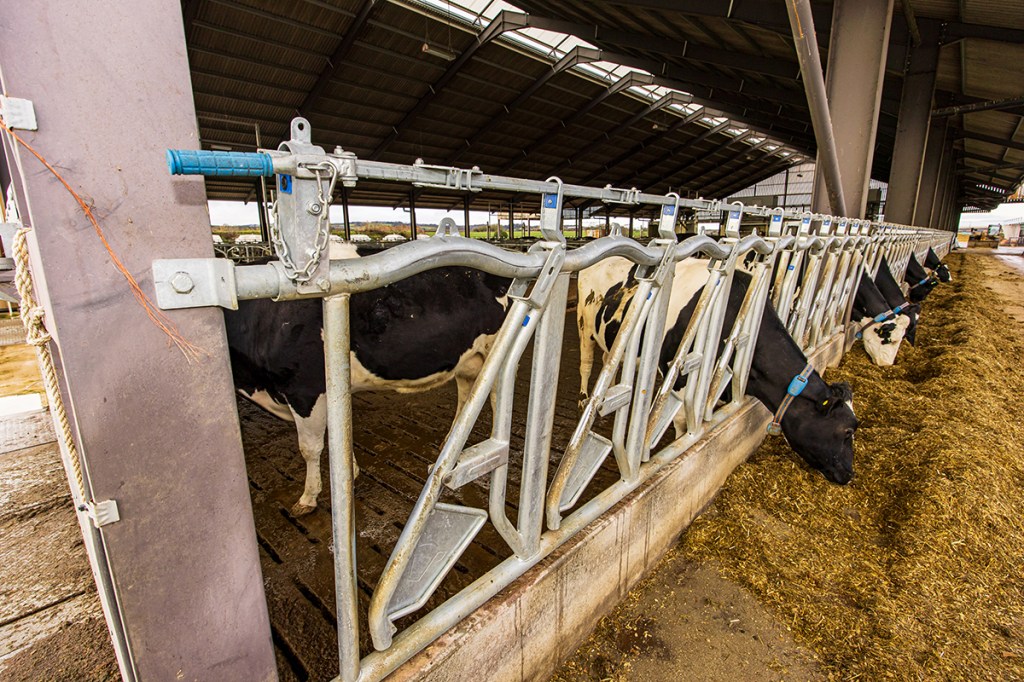
The feed barriers are From Agri-Kit, the self-locking yolks are in batches of five, but each run is separated so that only three levers need to be moved to lock a passage of the shed in. These are used for routine health checks and vet visits, reducing the need for handling equipment. However, at the build stage, Richard Robinson did spec a pit to use for drying cows off, and heath checks on udders.
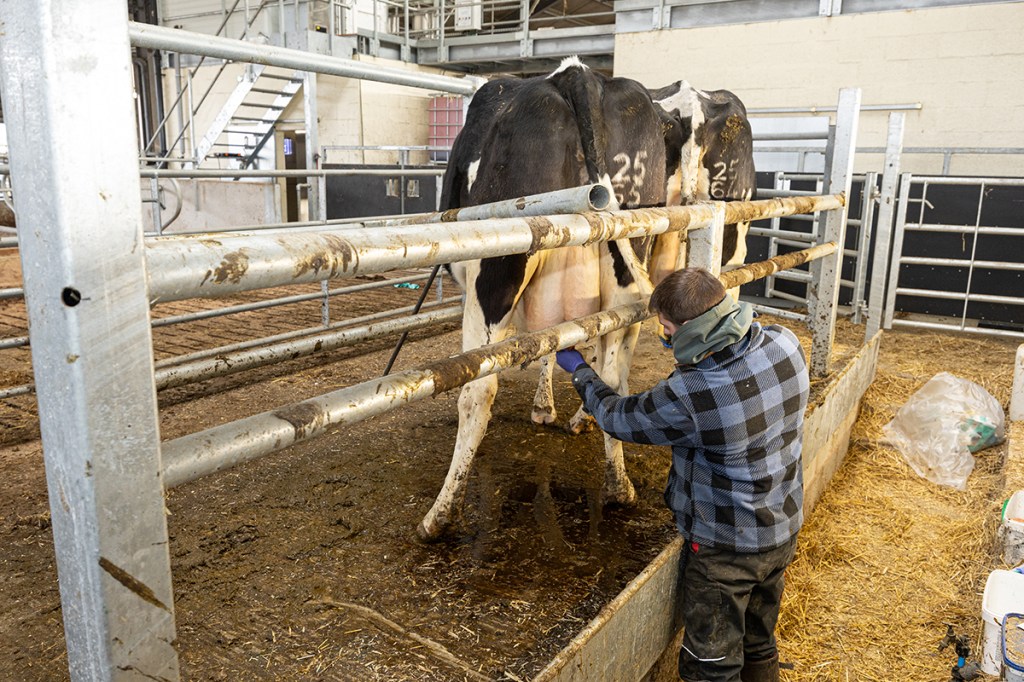
“It’s great to have it, but because we don’t have a parlour the cows can be a little twitchy, but they soon settle, it means we have a controlled space, and don’t have to bend down to work on the cows,” says James.
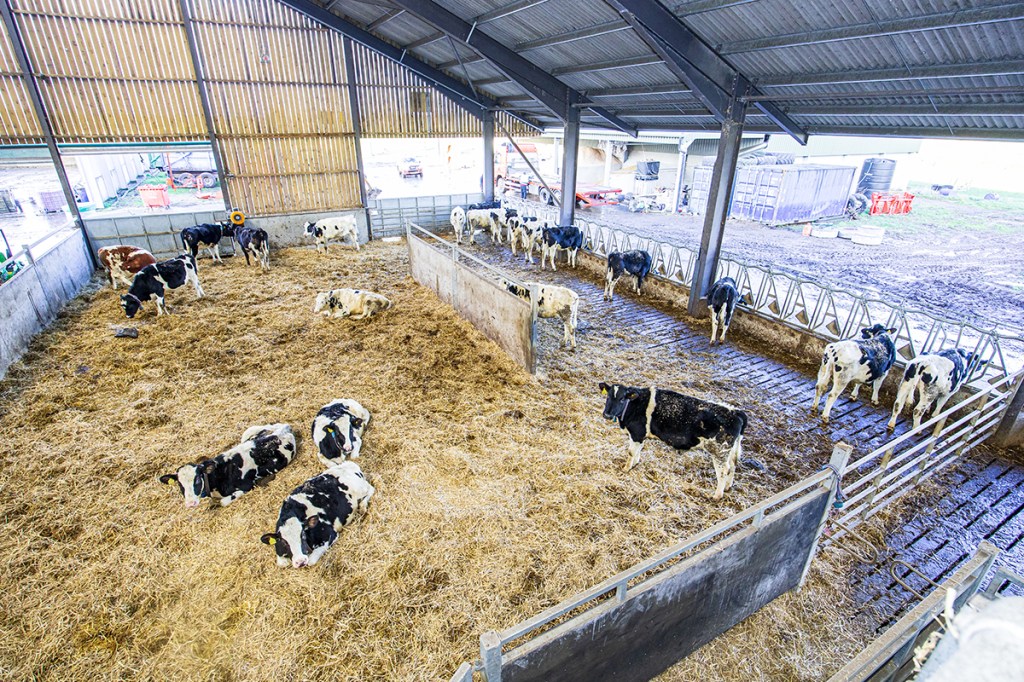
In each shed there is a non-milking area, one has the dry cows, which is where the handling crush/pit is, so the animals don’t have to be shifted around, fresh calved cows and their calves are on the other side of that shed. The other shed has the heifers, the dry cows and heifers are bedded on straw, while the cows with calves are on paper, which helps with hygiene and is warm for the newborns.
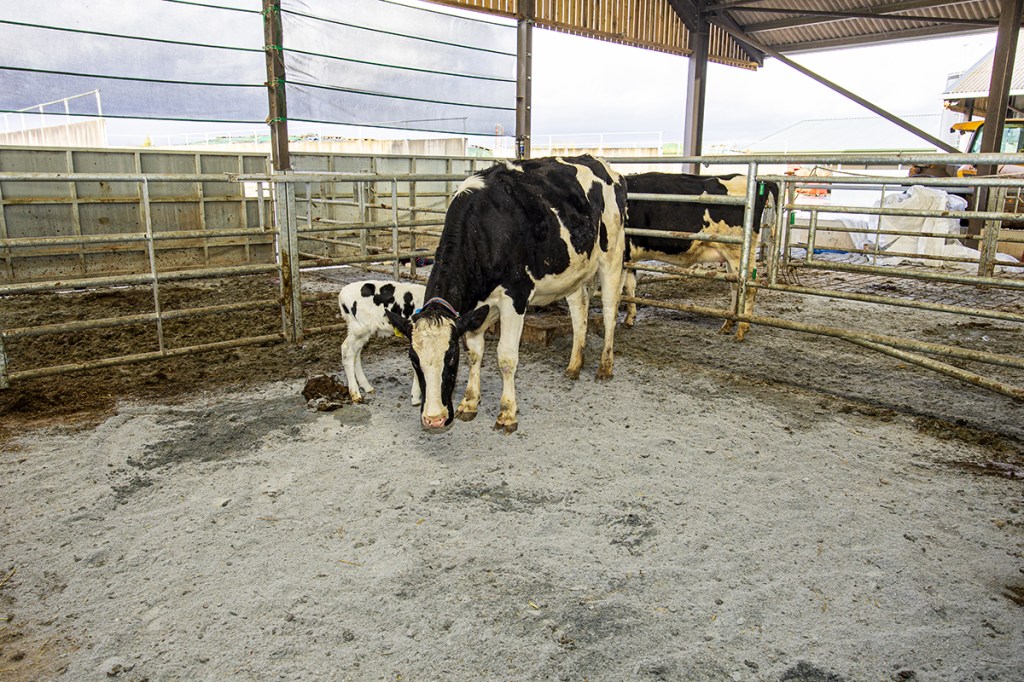
Animal welfare is high priority, the herd is dried off using selective dry cow therapy, changing diet and environment, along with applying a sealant to the teats. This reduces antibiotic use and improves efficacy when it’s actually needed. Speaking of herd health, there are foot baths after milking, there is CZF and Formalin in the water, which is changed every sixty cows/milkings.
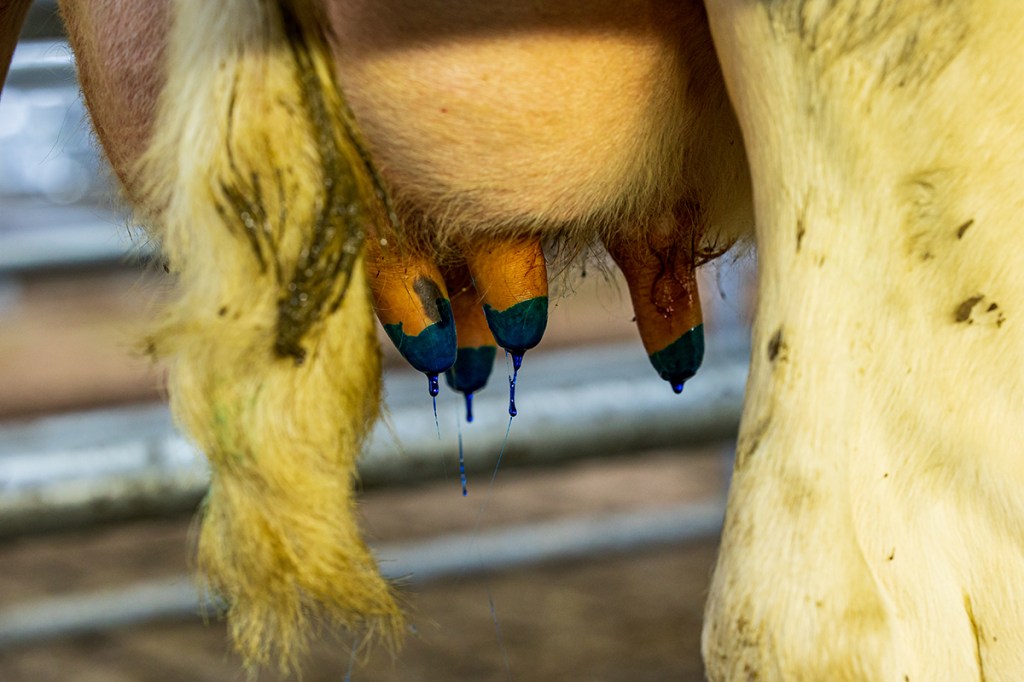
“We get the odd bruised hoof, and occasional damage from slats, but mostly foot care is routine trimming,” points out Henry.
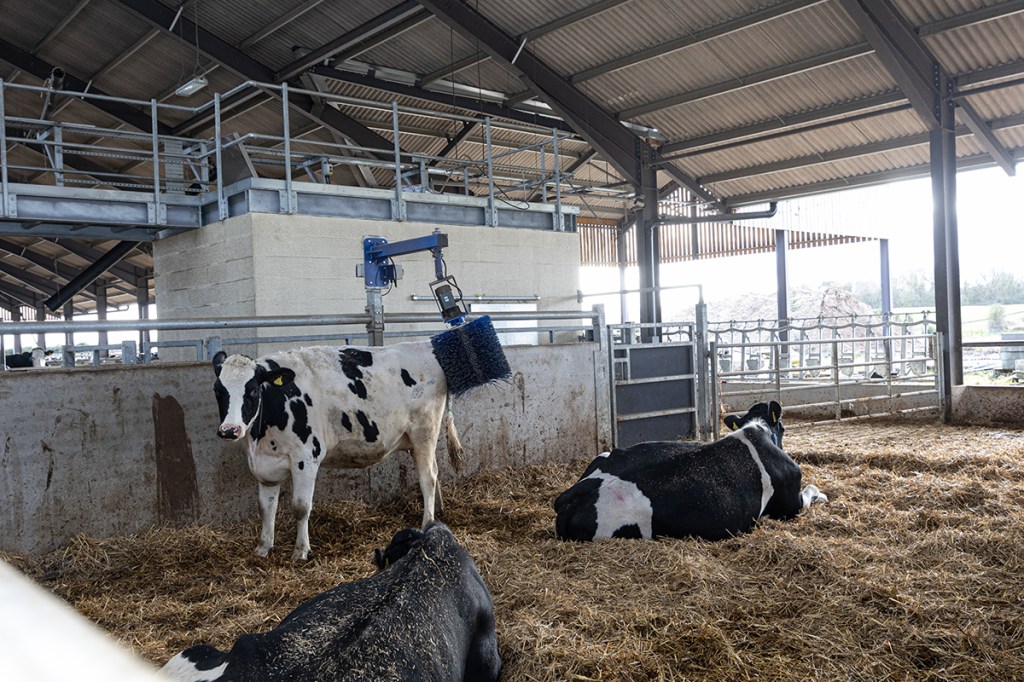
There are Sveaverken brushes dotted around, enough that there isn’t a cue or any competition for some grooming time.
Labour factor
There are four people looking after the whole operation day to day, dad Richard, sons Henry and James, and an apprentice, Harry. It can be done with two people on quiet days, at weekends James and Henry’s partners work with their other halves, so the other couple can take the weekend off.

When there is field work to do a full team is required, the robots allow levels of flexibility traditional system doesn’t offer. And because the farm is in control of much of the work, jobs can be mixed and swapped accordingly.
Ken Topham, aerial images thanks to Nigel Aldritt.
For more up-to-date farming news click here and subscribe now to profi and save.